粉末床熔融金属增材制造中的缺陷和异常(2)
时间:2023-01-06 11:03 来源:长三角G60激光联盟 作者:admin 阅读:次
1.2.2. 电子束粉末床熔化
E-PBF使用电子束作为热源,选择性地烧结/熔化粉末。该工艺能够制造出近乎完全致密的金属零件,其机械性能可与传统制造的零件相媲美,例如铸件或成型件。因此,E-PBF部件可以在许多应用中用作承重结构。商业化的 E-PBF 系统的操作经过优化,可最大限度地减少缺陷,就像在 L-PBF 中一样。然而,这些系统为过程修改提供了较少的自由度,并且缺乏对功率和扫描速度等的直接控制。
E-PBF系统有三个主要组件:电子输送,粉末扩散系统和构建室。顾名思义,E-PBF和L-PBF之间的主要区别在于热源。E-PBF工艺使用电子枪作为热源,其位于粉末床的正上方(图5)。电子是通过加热灯丝产生的,灯丝可以是钨丝或六硼化镧LaB6阴极。然后,电子被施加的电压加速,由一系列电磁透镜聚焦和引导。与激光光学相比,E-PBF工艺中的电磁透镜可以无惯性地移动电子束。结果,电子束的峰值扫描速度可以达到102m/s,明显快于激光器的速度,激光器的速度被扫描光学元件限制在几米/秒。
E-PBF工艺通常在预热步骤后具有两种熔化模式,如图4所示。剖面线是填充体积区域的熔化模式,并使用光束沿着平行扫描路径来回扫描,由预定义的剖面线间距距离分隔。之后,轮廓勾勒出每个横截面的边缘,并提高表面光洁度。可以更改的一些常见参数包括光束电流,焦点偏移(控制光斑大小)图案填充间距距离等。
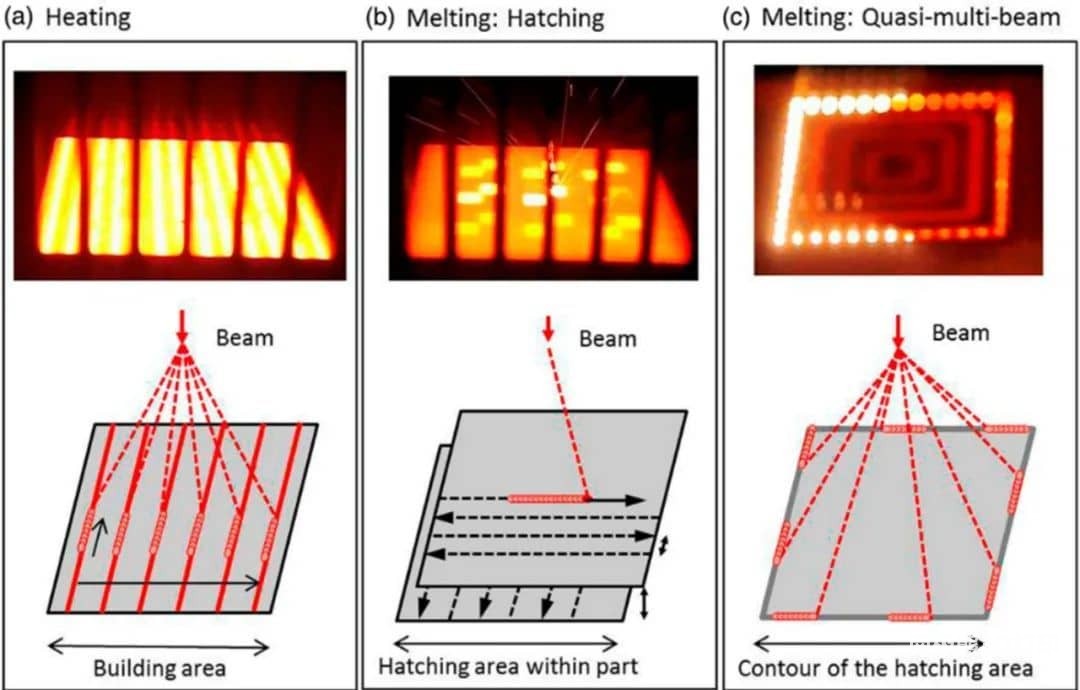
图 4 E-PBF工艺中三种熔融模式的实际图像和示意图。
E-PBF机器中的另一个关键模块是粉末扩散系统,其基本目标是在熔化步骤之前将粉末从储液罐输送到构建板上均匀的层上。在Arcam E-PBF系统中,两个料斗和一个耙子被协调以完成上述任务。标准 E-PBF 粒径范围为 45–106 μm,比 L-PBF 中使用的原料更粗糙。较粗的粉末减少了吸烟,因为颗粒质量更大,这意味着需要更多的动能来喷射任何给定的颗粒。此外,由于在E-PBF工艺中,工艺分辨率(即熔池尺寸)通常较粗糙,因此不需要使用更细的粉末。当然,使用较粗的粉末更具成本效益,因为标准雾化技术产生的粒径范围比AM中使用的颗粒范围更广。
由于球形、特定粒径范围和化学纯度的要求,目前市场上用于SLM和EBM工艺的Ti粉末主要通过气体雾化(GA)或等离子体旋转电极工艺(PREP)生产,两者的运营成本都很高。此外,一些增材制造设备供应商为其特定机器提供自己的专有粉末套件。因此,对于大多数AM操作和应用,粉末和成品零件的成本很高。对于Ti AM的更广泛应用,需要适用于AM的具有成本效益的球形Ti粉末。
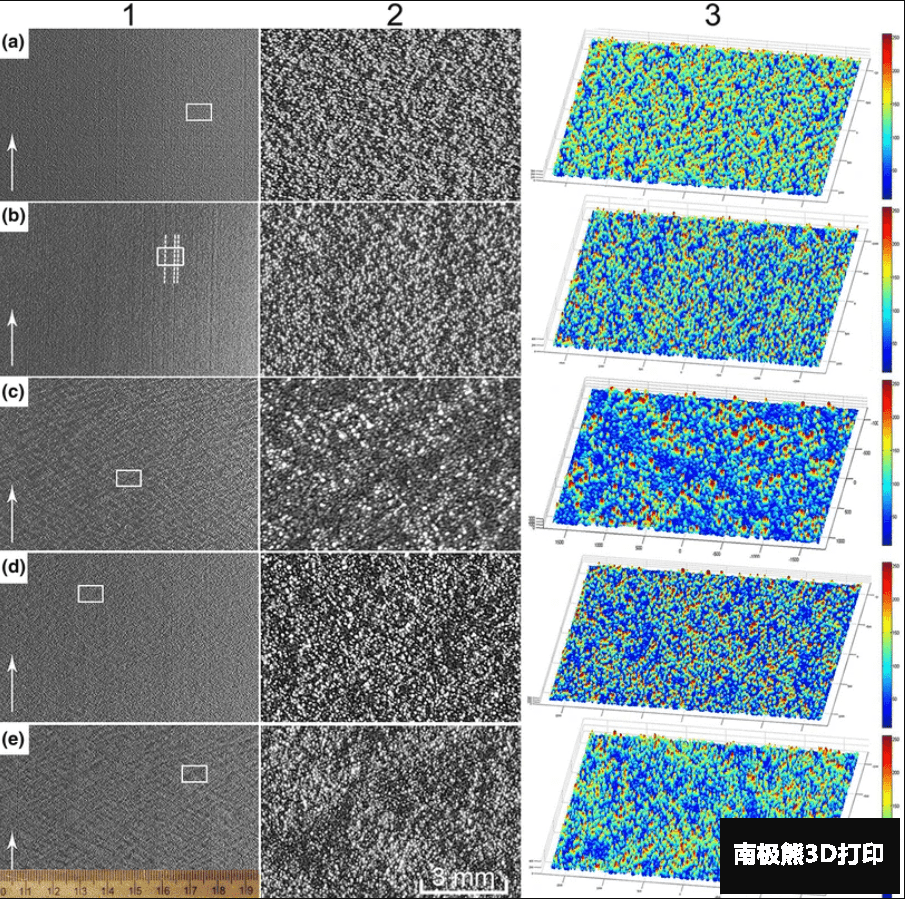
UPB系统中收集的不同粉末的宏观表面轮廓:Arcam Ti-6Al-4V(a)原始粉末和(b)用过的粉末,经PMT处理的新型Ti粉末(c)45–106μm,(d)75–106|μm和(e)45–75μm。
同样,悬垂需要支撑结构,就像在L-PBF过程中一样,但用途不同。与后一种工艺不同,E-PBF中使用的高预热可能储存的残余应力很少。然而,总是有可能在未熔化的粉末包围的悬垂物中积聚热量,这些粉末具有较低的导热性。局部过热会导致熔池尺寸过大,并与预期的构建条件(和尺寸)发生偏差。E-PBF中的支撑结构用于为从悬垂物中提取热量提供固体通道。
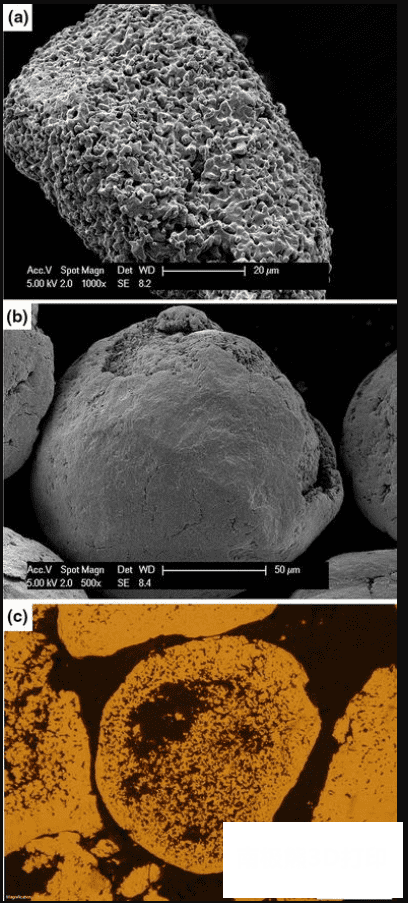
显示新型Ti粉末表面特征的扫描电镜图像(a)在PMT处理30分钟之前和(b)之后和(c)以及(c)PMT处理的粉末颗粒横截面的光学显微照片
1.3. 熔化模式
基于粉末的增材制造(AM)利用移动的能量源(例如,电子束或激光)以逐层方式选择性地熔化金属粉末,以构建所需的3D(3D)结构。下图显示了从有限元模型获得的温度等值线和熔池边界。FE计算的热结果可以进一步计算熔池尺寸,凝固速率和温度梯度,从而可以预测凝固微观结构。
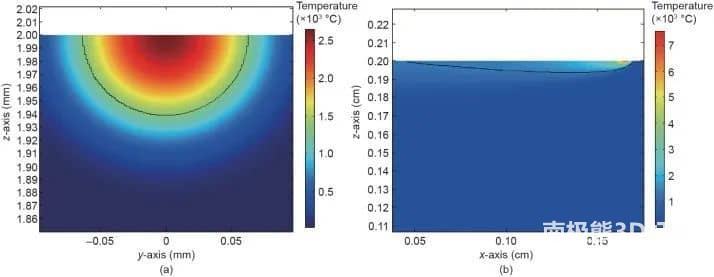
(a)有限元模型温度轮廓(°C)和熔池边界(黑线表示)的横截面图(y–z);(b)有限元模型温度轮廓(°C)和熔池边界(黑线表示)的纵向视图(x–z)。模拟激光功率为200 W,扫描速度为960 mm·s−1,吸收率为0.5。
在一些研究中已经报道了测量温度和模拟之间的直接比较。Peyre等人构建了一个由20层组成的薄壁,其中三个热电偶放置在基板上。通过温度测量验证了热预测,显示了热量积聚(来自连续层)对熔池尺寸的影响。Denlinger等人使用数值模型来估计包含38层的块状几何形状的热历史,以便与Inconel 718粉末床融合期间的原位温度测量进行比较。预测的温度与测量结果吻合良好。
图5显示了假设的高斯激光束在传导和锁孔模式下的激光能量吸收之间的比较。除纯传导模式外,激光与液态金属相互作用,粉末熔化成熔池前部的液体。此外,散焦(在L-PBF中)或焦点偏移(在E-PBF中)会影响打印模式和孔隙形成,即散射激光会降低功率密度,这有助于避免不稳定的锁孔和孔隙形成。
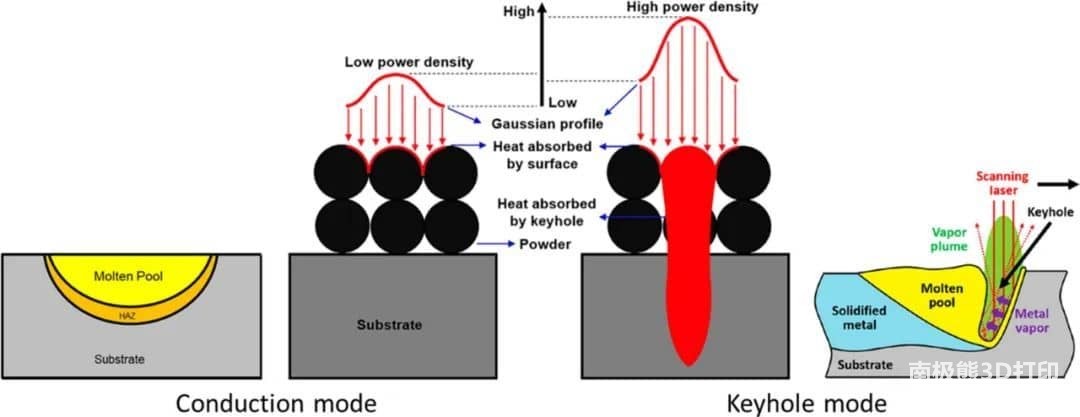
图5 初始时刻激光在传导模式和锁孔模式下的能量吸收示意图。假定激光具有高斯分布。在传导模式下,激光能量被上表面吸收,而在锁孔模式下,激光能量主要被吸收在蒸汽腔的内表面。
1.3.1.传导模式
传导模式通常与熔池有关,其中汽腔及其相关影响可忽略不计。传导模式通常会产生半圆形熔池或长宽比较小的熔池,如图5所示。基板中的能量密度足够低,以至于基板温度不会升高到沸点以上,因此不会形成汽腔。Bag等人采用了仅传导传热模式的假设,他们使用自适应体积源成功地对点焊进行了建模。在他们的研究中,熔池都显示出与导电模式焊接相关的特征,近似半圆形。在另一种方法中,Russo等人将传导模式焊接描述为熔池运动或扩展(去聚焦)热源不会干扰热分布。
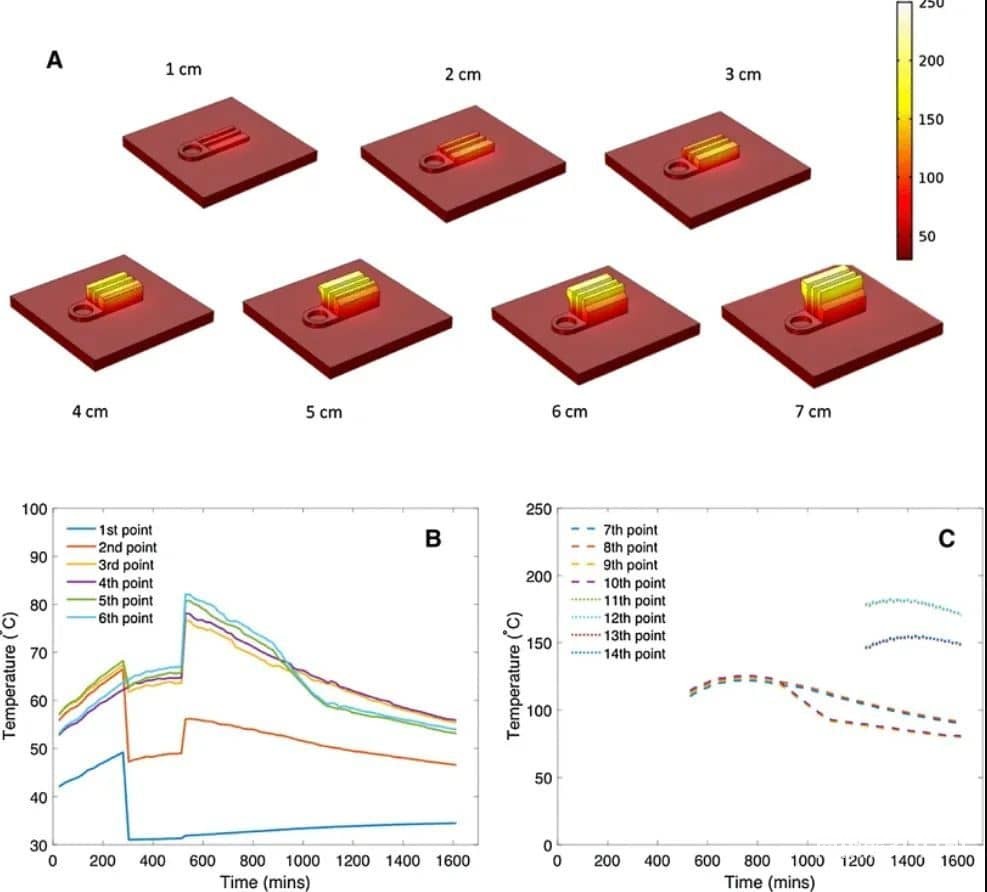
a显示从数值模型获得的热演化的三维温度等值线图;感兴趣点的b和c温度。温度显示在下一粉末层沉积之前。
上图a显示了当上表面温度相对均匀时,下一粉末层沉积前的层温度。图a还表明,由于建造过程中的热量积累,建造的高层具有局部较高的基础温度。预计室温的最大温升约为250°C。图b、c显示了所有14个点的预测温度历史(在层沉积结束时)。该图说明了整体能量输入、几何特征和制造时间对整体温度升高的影响。例如,图b显示了几何图形左侧的薄区域建造完成后,在点1和点2上方没有进一步的直接热量输入的情况下,约300分钟左右的层温度突然下降。由于扫描面积较小,一层的扫描时间从70秒减少到50秒,导致约500分钟的层温度突然升高。
1.3.2. 锁孔模式
当激光功率强度增加到约1 MW/cm2以上时,就实现了锁孔模式。激光冲击材料表面会提高温度,导致熔化。随着温度进一步升高并达到沸点,金属蒸汽的形成会产生反冲压力。反冲压力将熔融金属向下推,形成一个细长的气体腔,称为锁孔。激光进入锁孔后,在被吸收(或部分反射出去)之前,会经历来自前后锁孔壁的多次反射。如图5所示,与传导模式相比,在PBF过程中,已经凝固的零件将经历更多的再熔化和冷却热循环。
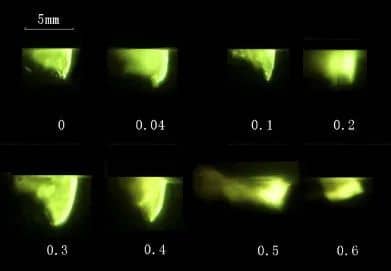
钥匙孔形状各异的照片。铝膜厚度为0至0.6 mm。激光功率:1000 W,焊接速度:1 m min−1,离焦:0mm,保护气体流量:2m3h−1。
上图显示了铝膜厚度范围为0至0.6 mm的锁孔形状的清晰照片。关于相机的曝光时间设置为1/1000 s,激光束和锁孔都可以在如此短的时间内被视为静止。实验结果表明,气液界面清晰可辨,锁孔弯曲方向与焊接速度相反。锁孔弯曲的原因是由于激光束与工件之间的相对运动,在实际的深刺激光焊接中。锁孔的形状由锁孔等离子体的密度控制。当两块玻璃之间没有夹住铝膜时,钥匙孔的形状狭窄而深,具有可变横截面的细长毛细管。随着铝膜厚度的增加,这意味着锁孔等离子体的密度更高,孔径增加以及更深的锁孔形成。当薄膜的厚度增加到0.3毫米的中间厚度时,钥匙孔达到5.3毫米的最大深度。继续加厚铝膜,孔径继续扩大;然而,锁孔的深度急剧减少。这种现象表明,锁孔等离子体的过量密度阻碍了入射激光束向内部材料的传输。多余的锁孔等离子体会阻挡激光束,反射并重新聚焦激光束,导致锁孔塌陷。
(责任编辑:admin)
最新内容
热点内容