激光粉末床熔合增材制造缺陷结构工艺流程图(1)
时间:2022-01-28 15:12 来源:江苏激光联盟 作者:admin 阅读:次
准确的缺陷检测、表征和预测在全密度和无缺陷金属增材制造(AM)中具有巨大的潜在影响。因此,本文提出了缺陷结构过程图(DSPMs)作为一种量化孔隙率作用的手段,在粉末床印刷材料中作为一个示例缺陷结构。利用同步加速器微计算机断层扫描技术(μSXCT)研究了激光粉末床熔合(LPBF)材料的金属AM缺陷在加工参数空间内的可预测趋势。利用激光功率、扫描速度和舱口间距的变化,在EOS M290上制作了ti - 6al - 4v测试块。μSXCT在低激光功率、高扫描速度的过程空间区域发现了典型的欠熔或欠熔缺陷。
这些缺陷与相邻熔体轨迹之间的不足重叠有关,可以通过应用熔体池几何建模的缺乏熔合准则来避免。大规模的钥匙孔缺陷也被成功地缓解了与浅钥匙孔前壁角相关的熔体池形态估计。与ti - 6al - 4v的标称(制造商推荐的)加工参数相比,工艺变量的选择导致深孔,即高激光功率和低扫描速度,球形孔隙率大幅增加。在完全致密的过程空间内也发现了缺陷,这与激光-粉末相互作用过程中气体孔隙转移到AM测试块有关。总之,这项工作表明,通过选择适当的工艺参数,可以成功地预测LPBF材料中的大规模缺陷,从而减轻/最小化缺陷。
1. 介绍
激光粉末床融合(LPBF)金属增材制造(AM)技术目前为零件生产提供了最好的再现性和尺寸精度,因此在工业界和学术界都得到了很好的研究。一般来说,LPBF技术使用以下步骤来制造组件:(1)在机器内的构建板上铺上一层指定厚度的金属粉末;(2)用激光束选择性地熔化粉末层内所需的区域;(3)将构建板向下移动,在构建板上铺上一层新的粉末。这个过程一层一层地重复,直到零件制造完成。LPBF金属AM构建的积极工艺结果是由各种工艺参数控制的,包括但不限于束流功率(P)、扫描速度(V)、舱口间距(H)、层厚(D)和扫描模式等许多其他参数。
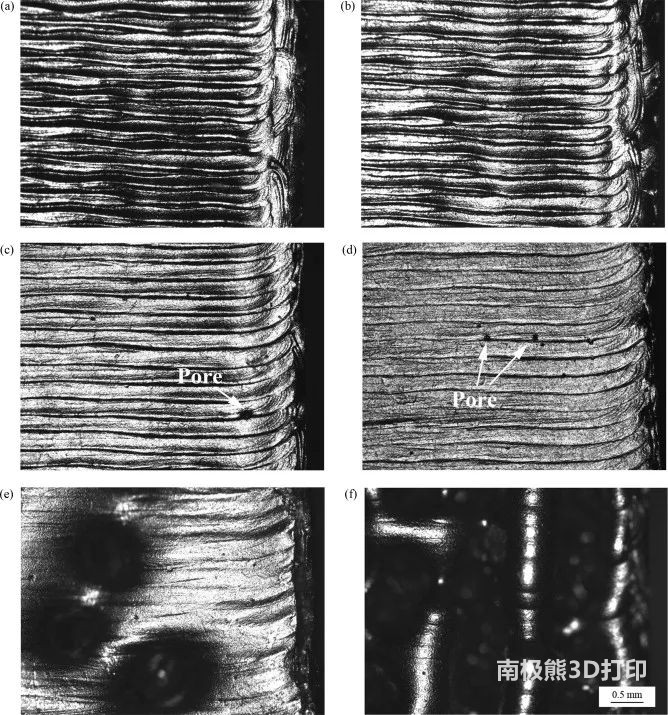
EBM样本与聚焦偏移的顶部表面表征(所有图像都是相同的放大倍数)。 (a) 4 mA. (b) 8 mA. (c) 12 mA. (d) 16mA. (e) 20 mA. (f) 24 mA.
EBM Ti-6Al-4V样品的表面拓扑如上图所示。与激光束相比,小的焦差值(4 mA)会导致光束斑集中,且在粉末层的穿透深度较大。以前的熔槽线部分熔化形成熔池,以确保熔槽的一致性和重叠。每条固化的舱口线形成一个山脊形状,造成粗糙的表面拓扑结构。但是,增大焦距偏移量会改变熔池的形态。焦点偏移显著提高了表面粗糙度,如图(c)和(d)所示。可以观察到细小的气孔,这可能是由于熔化的粉末释放出气态的氩气包裹在粉末颗粒中。然而,这些缺陷用阿基米德方法无法检测到,当下一层在z方向过熔后再熔前一层时,这些缺陷可能消失。当焦差增加到20 mA或24 mA时,肉眼可以看到大毛孔。
大量研究表明,这些工艺参数的组合在很大程度上决定了熔体熔池的几何形状、局部组织、缺陷尺寸和缺陷形态。重要的是,不必要的LPBF缺陷,如孔隙度、夹杂物和氧化物,对金属AM组件的结构完整性和耐久性有害,特别是在航空航天和生物医学应用中,过早失效(如疲劳)主要由缺陷结构控制。Edwards和Ramulu发现,由于存在有害缺陷,无论表面条件或构建取向如何,L-PBF Ti-6Al-4V的疲劳性能强度比变形合金低约77%。Masuo等确定,加工缺陷(包括表面粗糙度)将预制试样的疲劳强度限制在锻造ti - 6al - 4v疲劳强度的1/3左右。因此,将相关的工艺参数与产生的缺陷分布联系起来,以认证金属AM工艺和部件,尤其是结构材料和生物医学应用,过程-缺陷-性能关系是很重要的。
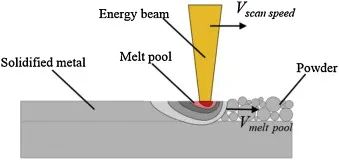
SLM过程中激光熔化金属粉末的原理图。
SLM中Zone III边缘参数和EBM中超线或焦点偏移导致的孔隙主要是熔体池重叠不足造成的。当激光或电子功率扫描粉末层时,粉末颗粒在瞬态过程中形成熔池,如上图所示。熔融材料与未熔粉的界面温度在熔点附近(Ti-6Al-4V为1660°C)。
一般来说,缺陷的产生或转移到成品零件有三种具体的方式,即:(1)从原料粉末中转移;(2)熔化过程中激光-粉末-金属相互作用;(3)后处理。结果表明,LPBF中存在4种不同类型的缺陷,即熔合孔隙度、锁孔孔隙度、球化和气孔率。为了限制金属AM内部缺陷的产生,必须考虑所有三种孔隙形成或转移机制,并通过适当的工艺参数选择加以控制。其中,激光-粉末-金属相互作用是金属AM加工过程中最常见的孔隙转移方式,在这一过程中,通常可以观察到“keyhole”和“lackof - Of -fusion”(LOF)孔隙等缺陷。熔体池之间是否有足够的重叠,以保证所有点至少熔解一次,从而确定未熔合孔隙度边界。
最近的研究也表明,LOF孔隙的形成是由于喷射粒子/溅射粒子中激光和熔池的相互作用。在激光扫描过程中,大的溅射可能没有完全熔化,因此溅射周围会产生一串未熔合的孔隙,从而成为潜在的孔隙生成位点。相反,锁孔孔隙边界对应于深锁孔的不稳定性,导致孔隙被夹断。第三个边界(称为“向上”边界)是由流体流动模式和熔体池的毛细管不稳定性的组合确定的,它是LPBF AM系统中在保持精度(例如,同时增加速度和功率)的同时提高产量的限制因素。整体的LOF、锁孔和珠状孔隙边界,特别是定义了一个有效的“过程窗口”,用于生产具有名义上全密度的零件;在该过程窗口内,孔隙度从粉末转移到零件。因此,LOF和锁孔孔隙边界将是本文的主要重点,以及孔隙含量随粒度变化的方式。全密度可以量化为具有>99.9%的体积密度,但应该注意的是,仍然可能存在较大的缺陷。其目的是优化工艺参数,减少LPBF AM材料中不必要的缺陷,并最终证明在缺陷内容定义的工艺窗口内操作LPBF机器是可行的。
本研究在前人研究的基础上,对ti - 6al - 4v合金的LPBF中缺陷分布的影响进行了研究。在此基础上,本文初步研究了基于熔池几何模型的全致密Ti-6Al-4V金属AM零件的制备方法,以及最近获得的Ti-6Al-4V合金在高速动态x射线扫描过程中小孔形态趋势和孔隙形成的信息。由于不同的合金在LPBF中响应的方式相似,因此期望缺陷结构过程图(DSPMs)方法可以应用于所有易熔合金。这将通过映射出激光功率扫描速度(P-V)空间[6]内的缺陷密度变化来完成,包括Ti-6Al-4V立方体的标准(制造商推荐的)加工参数的比较。这项工作的第二个目标是研究ti - 6al - 4v粉末和预制组件中气体孔隙的形成和保留,这是由单个粉末颗粒中捕获的气体引起的,如Cunningham等人[25]所示。因此,这一知识的预期应用将用于LPBF Ti-6Al-4V全致密零件级结构的dspm的构建,从而通过控制缺陷密度来提高打印这种材料和其他材料的可靠性。
2. 材料和方法
2.1. 实验装置
等离子体原子化的EOS Ti-6Al-4V合金粉末被用于在EOS M290 LPBF机器上制造测试块(立方体)。利用激光功率P、激光速度V和舱口间距H等工艺参数的变化,共生产了12个测试块,如表1所示。对于ti - 6al - 4v,推荐的EOS标准值P = 280 W, V = 1200 mm/s用于制作样品1,作为基线,与使用表1给出的加工参数制作的其他样品进行比较。工艺参数对这些样本选择p - V空间跨度在名义(制造商推荐)值用于EOS Ti-6Al-4 V为目的的理解速度的影响(样品2 - 5)、电力(样品6、7、8和9),和舱口间距(样品5、8、10、11、12)在缺陷密度(表1)。
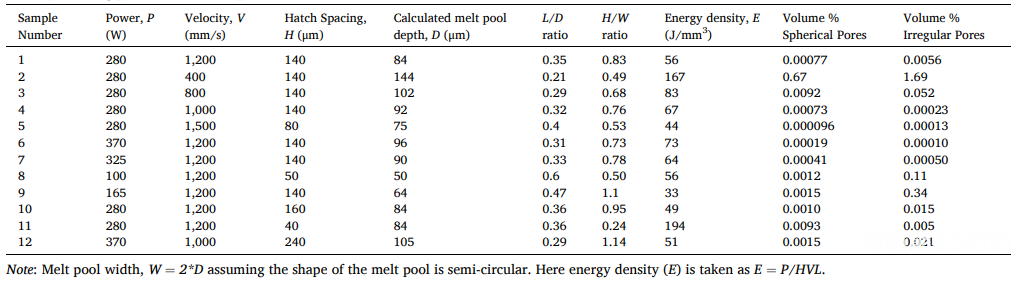
表1 LPBF ti - 6al - 4v测试块的加工参数表。
在试样2-5中,速度以280w的名义功率变化,试样5在1500 mm/s的高速下,根据几何模型减小了舱口间距,以避免熔合孔隙的缺失。在标称速度为1200mm /s的变功率样品中,样品8在较低功率为100w时,根据几何模型减小了舱口间距,以避免熔合孔隙的缺失。除样本5和8外,样本10、11和12的舱口间距也发生了变化。在标称功率和速度下,样品10的熔点间距增加,以引入几何模型中缺乏的熔体孔隙度;样品11的熔点间距减小,以使相邻熔体轨迹的重叠深度增加一倍,重叠深度增加四倍。另一方面,在样本12中,功率、速度和舱口间距与标称条件不同。根据几何模型,功率的增加和速度的降低伴随着舱口间距的增加。其思想是利用几何模型来避免LOF孔隙度和单熔体轨迹实验来了解小孔边界,然后选择工艺参数来提高沉积速率。对于所有样品,所有测试块的切片层厚度为L =30 μm,标称光斑尺寸为~ 100 μm(根据机器制造商提供的技术规格)。
2.2. 基于同步辐射的显微层析成像
在高级光子源(APS)上进行高能μSXCT,以测量粉末和印刷Ti-6Al-4V试块中缺陷(孔隙)的大小和形态,如Cunningham等人所述。从每个测试块的顶部1.5 mm3体积中提取尺寸为1 mm × 9 mm × 15 mm的预制μSXCT样品,其尺寸与构建方向平行。μSXCT是在白束模式下进行的,共有1500个投影以50°的角度拍摄180°以上毫秒曝光时间。体素大小为0.65 使用μm,导致最小可检测孔径约为1.5 μm。使用TomoPy0.0.3.15和FEI的AVIZO重建三维μSXCT体积™ 9.1.1软件。使用Avizo 9中的“各向异性”函数确定孔隙形态(即“球形”与“非球形”名称),0.5是“球形”的截止值。
虽然形态学不是确定缺陷形成机制的决定性指标,但可以合理地假设,高度球形的孔隙可能是由凝固过程中捕获的不溶性气泡(例如,气体或锁孔孔)形成的,而大部分不规则的孔隙可能是LOF缺陷。在该分析中,使用了以下孔隙度指标:(a)LOF孔隙(>40 微米和球形,(b)钥匙孔(>40 微米和球形)和(c)气孔(<20 微米和球形)。每个重建的3D数据集包含2560个 × 2560 × 2100个三维体素,总数据大小超过40GB。这个数据量意味着自动分析方法对于提取特征特征和相关静态数据是必要的。
2.3. 基于机器学习的圈闭气体孔隙度分割与分析
作为建造材料分析的初步步骤,对各种原料粉末进行了检查,以确定孔隙统计数据。根据工艺参数,相当一部分粉末孔隙似乎会被带入到内置零件中,因此,了解初始孔隙数量并在考虑最佳参数选择的过程中消除此类孔隙至关重要。至少有数千个粒子被用于构建宏观零件和样本,因此任务艰巨。机器学习(ML)技术用于在断层数据集中定位和分割粉末颗粒。对于自动化程序,第一项任务是识别粉末颗粒,并在具有各种信噪比的重建3D数据集中将其与背景分离。
与ImageJ或ilastik等其他软件相比,机器学习算法之所以方便,至少有三个原因,即:(1)提高了内存效率,(2)可能将优化的批处理移植到并行处理,以及(3)存在用于训练模型的简单图形用户界面(GUI)格式。本文概述了本研究中使用的ML技术。首先,对重建的μSXCT数据应用一组n3-D图像滤波器(通常基于使用不同掩模的卷积),以便考虑表征体素邻域的信息。然后在每个体素位置生成长度为n的强度I(x,y,z)和合成特征向量F(x,y,z)。例如,F(x,y,z)的第i个元素Fi(x,y,z)是使用应用于位置(x,y,z)的第i个滤波器获得的值。接下来,为训练数据集中的每个体素指定一个标签l,以向模型提供粉末材料体素和背景体素的示例。材料体素标记为1,背景标记为0。该过程用于在每个体素位置生成一组标签l(x,y,z)以及相应的特征向量。
在完成上述步骤后,利用样本体素对应的标签和特征向量对模型进行训练,自动学习标签和特征之间的复杂关系。最后,利用该模型从体素的特征向量为整个数据集中的体素分配标签。这样就得到了分割后的三维图像的二值输出:粒子材料为1,低密度、背景或空洞区域为0。粉末颗粒内部的孔隙被识别为三维空间中被颗粒体素包围的空隙区域。最后,利用商业软件AVIZO对这些二进制数据集进行了很好的处理,进行了统计分析。统计信息包括粉末大小,孔隙度分布和形态提取这些体积数据集。
(责任编辑:admin)
最新内容
热点内容