激光粉末床聚变:技术、材料、性能和缺陷以及数值模拟的最新综述(5)(2)
时间:2022-09-14 13:55 来源:长三角G60激光联盟 作者:admin 阅读:次
Luo等人指出,对LPBF进行的大部分建模工作使用移动高斯热源来建模熔池轮廓,很明显,这种模型需要大量时间和计算成本,不能用于较低的水平。为了减少计算时间和成本,提出了一种线热源,通过增加时间步长和减少单元数量来加速LPBF过程中的传热模拟。线热源代替移动的激光源。仿真结果表明,替换对开发没有任何更显著的影响,但可以大大减少计算时间。
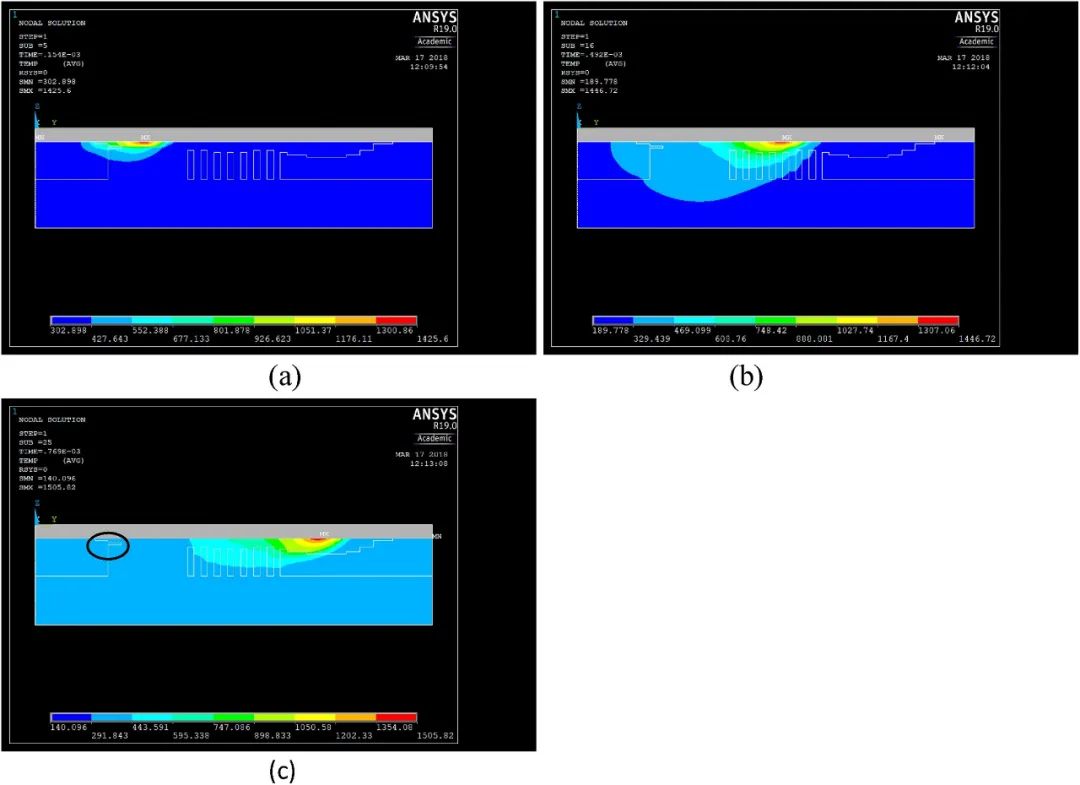
(a) 3、(b) 4和(c) 5区域中部370 W、1300 mm/s的温度分布。
已经进行了大量研究,通过建模和仿真优化LPBF工艺。但由于过程的高度复杂性,在结果中总是存在一些差距。许多研究人员现在正在尝试不同的模拟方法,以尽可能提高精度。
LPBF的主要障碍之一是理解加工参数与最终零件性能之间的关系。因此,研究人员开发了过程模拟作为优化过程参数的迭代。控制方程是任何模拟工作的数学背景。不同的目标可能需要使用不同的模型。模型必须考虑过程对温度的依赖性。由于实际世界中的相似性,热机械和热流体模型在研究人员中很受欢迎。热源建模也非常重要。注意,激光的最大能量强度集中在激光的中心,并沿激光光斑的周边逐渐减小。因此,高斯分布模拟了中心具有最大强度的热源。大多数模型的解是使用有限元法提取的。许多研究人员选择有限元法作为求解热方程的主要方法。但任何模拟仅基于计算数字给出结果;因此,有必要用实验结果验证模拟结果。
7.3.预测LPBF工艺特性的机器学习方法
由于其能够制造复杂的几何零件,LPBF是最普遍的金属增材制造工艺。它背后有大量的学术研究和工业投资。尽管使用有限元分析对LPBF进行了广泛的数值模拟,但仍然需要进行过程监控,以确保可靠的零件制造并减少制造后质量评估。为了使LPBF过程高效,需要基于人工智能的机器学习和深度学习技术。图37显示了实现基于机器学习的预测模型的方法。
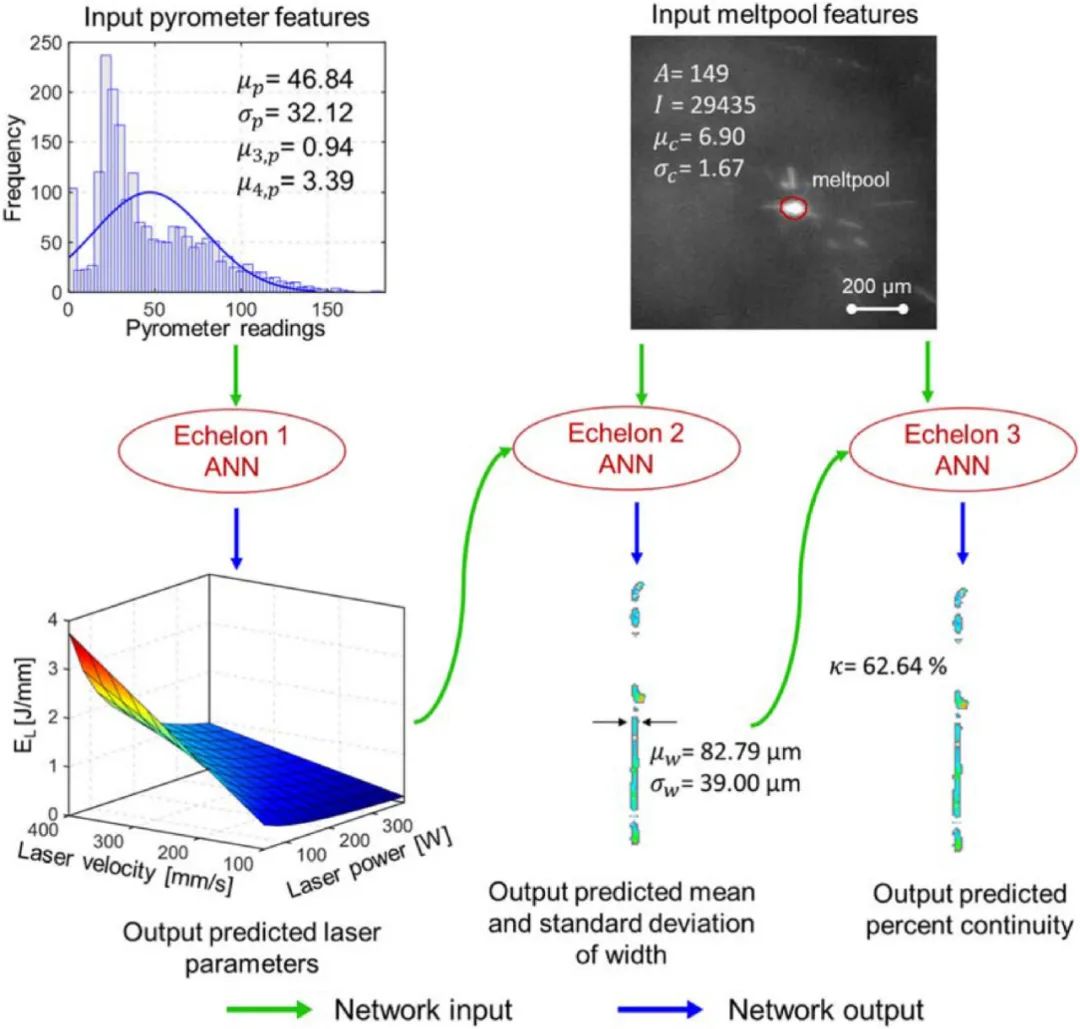
图37 顺序决策分析神经网络(SeDANN)示意图。上面所示的传感器数据和高度图属于以0.33的线性能量密度(EL)沉积的单个轨迹,即成球状态。从高温计中提取的统计概率分布特征用于第一级人工神经网络(ANN)中,以预测激光工艺参数(P和V),然后是从高速摄像机中提取的熔池特征,以预测更高层的平均宽度和标准偏差以及单道连续性。
本文研究了将ML纳入LPBF工艺链的多个阶段,从而提高质量控制的问题。ML可用于L-PBF之前的零件设计和文件准备。然后,机器学习技术可用于优化工艺参数并实时监控。最后,机器学习可以包括在后处理中。Okaro等人提出应用ML系统自动预测AM产品中的缺陷/缺陷。使用了半监督学习方法,该方法可以使用来自两个构建的数据,其中生成的组件被认证,并且在训练期间生成的组件的质量不确定。这使得该方法具有成本效益,尤其是当零件认证昂贵且耗时时。
Ogoke等人提出了深度强化学习,用于预测LPBF工艺的热特性和最小化缺陷的可能性,如图38所示。在熔化过程中,开发的控制算法改变激光器的速度或功率,以确保熔池的一致性,并最小化成型产品的过热。通过精确模拟不同激光路径下粉末床层的连续温度分布,对控制算法进行了训练和验证。
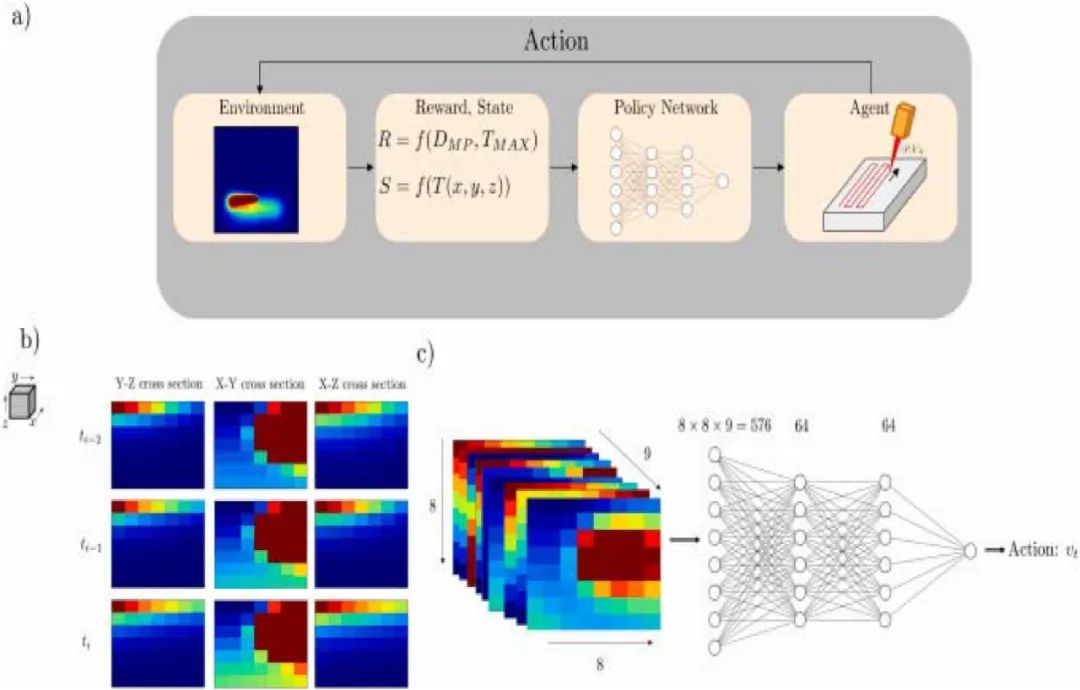
图38 深度强化学习框架。(a)在强化学习中,代理基于当前状态s和将每个状态映射到动作的策略π来选择动作。(b)对于模拟的前三个时间步,该状态由激光器位置附近的x-y、y-z和x-z平面中的域横截面表示。(c)策略网络是一个完全连接的神经网络,它接收状态的当前表示,并预测一个行动以最大化预期回报。策略网络被实现为两层多层感知器,具有双曲正切激活函数和每个隐藏层64个神经元。
Baumgartl等人提出了基于神经网络深度学习的模型和热成像离轴成像的集成模型组合,作为预测印刷缺陷和工艺监控(如熔池或离轴红外监控)的数据源。所提出的方法在预测分层和飞溅方面的准确率为96.80%。此外,该模型非常小,计算成本低,即使在功能较弱的硬件上也适合实时操作。大多数缺陷,如键孔、气孔和成球,都发生在熔池本身的尺寸和时间尺度上。对此类缺陷的监控至关重要。Scime和Beuth提出了一种深度学习方法,该方法提出了现场检测此类重要缺陷的可能性。使用固定视场的高速可见光相机研究了Inconel 718材料系统中LPBF熔池的形态。
Sanchez等人利用ML的潜力建立了工艺、结构和性能之间的关系,以预测LPBF工艺生产的78个合金基零件的蠕变率。使用包括LPBF工艺参数和从图像分析技术获得的材料几何特征(孔隙率图像)的输入数据来训练ML算法。该模型显著且准确地预测了LPBF的最小蠕变率,高达98.60%。Zhang等人开发了一种混合机器学习模型,用于预测LPBF工艺的可制造性评估。在设计方面,使用基于体素的卷积神经网络(CNN)模型,在工艺方面,使用神经网络(NN)模型。然后,将这两个模型集成在一起,以预测所选LPBF工艺参数下的体系结构的可制造性。
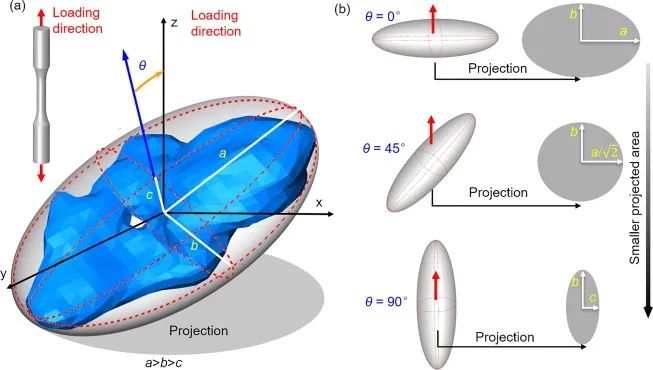
Peng等人使用ML的能力来预测LPBF处理的AlSi10Mg合金的疲劳寿命。发现极端梯度增强模型能够准确预测疲劳寿命。这些变量在限制疲劳寿命中的重要性按上述顺序进行评级。该模型预测了不同的样品寿命,这意味着微观结构起到了适度的作用。当平行于施工方向进行测试时,发现断裂面上的缺陷的巨大投影面积是观察到的寿命缩短的主要原因。更通用的双变量村上模型充分预测了疲劳寿命,而ML模型验证了经验相关性的经验模型更接近预期。
Zhang等人使用基于神经模糊的机器学习方法预测LPBF处理的316L不锈钢的高周疲劳寿命。创建了一个训练数据集,其中包含经受不同处理条件、后处理和循环载荷的样本的疲劳寿命数据,以模拟复杂的非线性输入-输出环境。Bao等人利用ML技术的潜力来确定缺陷位置、尺寸和形态对LPBF处理部件疲劳性能的影响。使用特征化技术识别导致高周疲劳失效的关键和重要缺陷,并使用支持向量机(SVM)作为训练的输入数据。选择具有测试数据的网格搜索策略来拟合模型参数,以加快优化过程。Moon等人建立了Ti-6Al-4V合金基试样疲劳性能的表面粗糙度和孔隙特征之间的关系。这些数据进一步用于训练用于预测部件疲劳寿命的机器学习模型。Hassanin等人提出了一种深度学习神经网络(DLNN)模型,用于合理化和预测LPBF处理的Ti-6Al-2Sn-4Zr-6Mo合金的致密化和硬度。开发了工艺参数和输出特性之间的关系,并将其用作训练DLNN模型的输入数据。创建的模型经过验证并用于创建流程图。训练的深度学习神经网络模型具有最高的精度,孔隙度和硬度的平均百分比误差分别为3%和0.2%。根据研究结果,深度学习神经网络被发现是从微小数据集预测材料质量的有效技术。
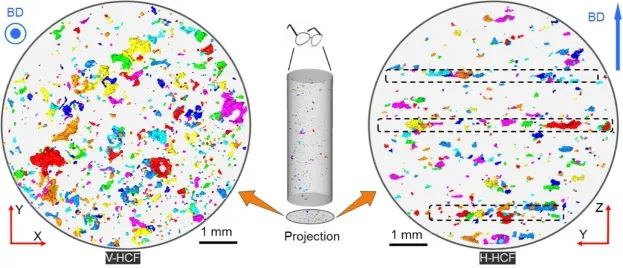
8.总结
增材制造是工业和学术领域中普遍存在的话题。本综述涉及对LPBF工艺的理解和最近的升级。LPBF已成为一种适用于多种金属及其合金的通用方法,因此受到了广泛关注。对LPBF过程进行了全面审查,并出现了一些关键点,这些关键点非常重要。还讨论了各种工艺参数的重要性,以最小化最终产品中的缺陷。
•对于任何材料上的LPBF工艺应用,为了在LPBFed零件上实现尽可能高的密度和所需的机械性能,最重要的是精确监控工艺参数。
•金属/合金暴露于LPBF工艺已经解决了与传统制造工艺相关的许多问题。LPBFed样品所继承的特性表明,LPBF可以生产出性能优于常规方法生产的样品。
•金属的致密化行为主要受激光能量密度变化的影响,激光能量密度的变化由若干其他工艺参数控制和改变。致密化可以直接与由于工艺参数的变化引起的激光能量密度的变化相关。
•在LPBF中,粉末粒度和分布的影响被认为不太重要,因为所有颗粒都经历完全熔化。与发生部分熔化的SLS不同,粉末参数对零件致密化的贡献可以忽略不计。
•通过选择性激光熔化加工的零件的微观结构特征受到其热历史的强烈影响,包括加热和冷却速率的变化、温度梯度、温度升高等。生产后处理方法对于细化微观结构非常重要,标准工艺包括退火和热机械加工。
•热历史,主要是凝固速率、冷却速率和热梯度,也决定了LPBFed零件的机械性能。大多数机械性能归因于晶粒微观结构的细化,因此取决于热历史。
•由于完全熔化是LPBF的一个重要特征,该工艺极易发生熔池不稳定。如果工艺参数选择不当,这也可能导致微观结构缺陷。所有缺陷都会对零件的性能产生不利影响。此外,较大的粉末颗粒难以熔化。因此,当使用较粗和较大的粉末进行LPBF时,观察到表面光洁度较差。
•决定缺陷的一个关键因素是与层数增加相关的“阶梯”效应:缺陷,特别是表面粗糙度,随着层厚度的增加而增加。因此,我们的想法是平衡表面粗糙度和产品成型时间之间的平衡。
•基于人工智能的机器学习和深度学习技术用于过程监控、预测产品质量和优化过程控制。
来源:Laser Powder Bed Fusion: A State-of-the-Art Review of the Technology, Materials, Properties & Defects, and Numerical Modelling, Journal of Materials Research and Technology, doi.org/10.1016/j.jmrt.2022.07.121
来源:Beese, A. Wilson-Heid, A. De, W. Zhang, Additive manufacturing of metallic components – Process, structure and properties, Progress in Materials Science, 92 (2018), pp. 112-224, 10.1016/j.pmatsci.2017.10.001
(责任编辑:admin)
最新内容
热点内容