创造波音历史四个第一:777X机翼靠3D打印模具
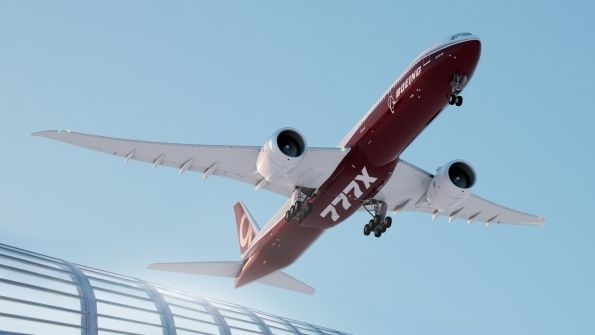
图:波音777X,来源:波音。
2019年年初,备受关注的波音777X宽体客机将实现飞行试验机的下线和首飞,并计划于明年完成试飞和首架交付。作为波音最新款的飞机产品,777X的生产集成了当今最先进的复合材料制造技术、金属加工技术和机器人装配技术,体现了数字化和自动化技术的全球最高水平。777X机翼的制造,更是因为波音及其供应商的创新,创造了若干世界之最,以及波音历史上的数个第一。
一、细数波音777X机翼制造的世界之最和史上首次
波音777X机翼创造了四项世界之最——最大尺寸的复合材料机翼,最大尺寸的热压罐,最大尺寸的3D打印模具,最大的机体部件生产建筑。同时,777X机翼也创造了波音历史上的四个第一——首次采用可折叠翼梢,首次采用整体翼梁,首次采用自动丝束铺放技术制造机翼蒙皮、翼梁和桁条部件,首次采用近乎全自动化的工艺完成机翼部件铺放成形。
1、四项世界之最
机翼尺寸。波音777X复合材料机翼的翼展达到了创纪录的71.8米,比A350WXB的翼展长7米,是世界上最大的复合材料机翼,也是世界上最大的双发客机机翼,翼展甚至超过了777-8型机身69.8米的长度。波音777X翼根宽度达6米,机翼面积467平方米,展弦比超过11,机翼拥有明显的翘曲,这对其蒙皮制造造成了一定的挑战。
热压罐。对于追求整体成形的复合材料部件来说,机翼尺寸直接影响其制造体系的尺度。为了固化尺寸创纪录的777X复合材料机翼部件,波音供应商ASC公司为其打造了世界上最大的热压罐。热压罐长36.5米,宽6.5米,重达544吨。为了检验其密封性和焊接强度,波音还要对其进行压力测试,注水2578立方米,这将使其总重超过3175吨!
图:热压罐在波音进行内部设备安装 图片来源:波音
3D打印模具。2016年8月29日,由波音和美国能源部橡树岭国家实验室联合开发的3D打印模具,获得了吉尼斯世界纪录。这个3D打印模具用于波音777X机翼部件修边和钻孔,长5.33米,宽1.68米,高0.46米,重784公斤,是世界最大的实心3D打印物体。模具使用混合20%碳纤维的ABS塑料制成,依托辛辛那提公司的大幅面增材制造(BAAM)设备,制造时间仅用了30小时,而制造传统上的金属模具则需要至少3个月。
图:吉尼斯认证人员测量3D打印模具 图片来源:橡树岭国家实验室
生产建筑。2013年,华盛顿州以16年减税87亿美元,以及让机械师签署不涨养老金的长期劳动合同为价码,赢得了波音的青睐,将777X复合材料机翼中心(CWC)设在波音双通道客机总装大本营埃弗雷特。CWC建设耗资10亿美元,让埃弗雷特同时拥有了世界第一大和第四大建筑,CWC建筑可用空间370万立方米,仅次于波音埃弗雷特总装厂、沙特麦加大清真寺以及空客图卢兹A380总装厂,也是世界最大的机体部件生产建筑。
2、四个史上首次
翼梢小翼。国际民航组织将翼展65米以下的飞机定为代码E,对于超过这一长度即代码F的飞机,机场将会额外收取航空公司费用。为了便于机场运营和降低航空公司费用,波音777X采用了长3.5米的可折叠翼梢,飞机在跑道上减速滑行时翼梢将向上折叠。采用折叠机翼在舰载机上已经屡见不鲜,波音自己制造的F/A-18就是折叠机翼,但这在客机历史上还是第一次,第一代波音777研制时,波音就考虑过这个方案从而设计更长的机翼,但是由于航空公司拒绝而放弃。在解决了技术问题,以及与美国联邦航空管理局(FAA)和欧洲航空安全管理局(EASA)展开多年后,FAA于今年5月批准了可折叠翼梢的商用,从而实现了这一历史性的突破。
整体翼梁。波音787和空客A350的复合材料翼梁都是分三段制造,然后装配成完整翼梁的。而波音777X则破天荒地采用了整体翼梁的设计,翼梁长达破纪录的32米,每架777X上的4根翼梁需要几乎640公里长的碳纤维丝束。这离不开技术的进步,也是缩短运输物流的考虑,同时,这种设计也可以极大减少紧固件数量和装配工作量,达到减重、缩短生产周期、降低寿命周期成本的效果。
图:装配中的整体翼梁 图片来源:波音
丝束铺放。波音选择与美国Electroimpact公司合作,引入其创新的龙门式高速AFP设备,制造蒙皮和翼梁;同时,西门牙MTorres公司也在埃弗雷特设立先进制造创新中心,向波音提供桁条AFP设备,该公司还同时向波音提供777X机翼翼梁装配单元和机翼桁条连接装配单元。值得注意的是,这次是Electroimpact公司击败MTorres公司,为其AFP设备赢得的首个机翼制造订单,设备最高单价可能高达2500万美元,而且波音预计最多会订购12台。
图:价值2500万美元的自动丝束铺放设备 图片来源:波音
全自动化。当前,全自动化铺放还未完全实现,瓶颈就在于人工检测环节。以往的人工检查必须在每一铺层铺放之后停机,检查人员根据投射在模具表面的激光轮廓通过肉眼与铺层进行对比,确认丝束末端精度,之后使用手持放大镜扫描缺陷,这个过程费时费力且存在一定的漏检率和错误率。波音通过研究发现检测和返工时间占到了生产周期的63%,是铺放本身的2.5倍,而且,这些时间的分布还是在波音实施了多年工艺改进、检测时间和总周期已经下降了不少的情况下得到的。波音777X机翼庞大的尺寸决定了在铺放过程中不可能采用人工检查,因此Electroimpact公司通过三年多时间开发了自动化原位检测系统,目前这是唯一被复合材料部件生产商完全认证的系统,让波音777X机翼制造向着全自动化和工业4.0迈进了一大步。
(责任编辑:admin)