Nature:超细晶粒高强度钛合金的增材制造
时间:2023-01-16 11:21 来源:长三角G60激光联盟 作者:admin 阅读:次
增材制造,通常被称为3D打印,是一种逐层构建零件的过程,是创建接近最终(净)形状的组件的一种有前途的方法。对于复杂度高、材料浪费低的产品,该工艺正在挑战传统制造工艺的主导地位。通过增材制造制造的钛合金已应用于各个行业。然而基于熔融的金属增材制造工艺的固有的高冷却速率和高热梯度通常导致非常精细的微观结构和几乎完全倾向于柱状晶粒,特别是在钛基合金中。优化增材制造的工艺参数的尝试表明,很难改变条件以促进钛晶粒的等轴生长。与其他常见的工程合金(如铝)相比,目前还没有能够有效细化微观结构的商业钛晶粒细化剂。为了应对这一挑战,本文报告了钛-铜合金的发展,这些合金在凝固过程中由于合金元素的分配而具有高的过冷能力,这可以克服增材制造过程中激光熔化区域中高热梯度的负面影响。在没有任何特殊工艺控制或额外处理的情况下,打印的钛铜合金试样具有完全等轴细晶粒微观结构。与在类似加工条件下的常规合金相比,它们还显示出良好的机械性能,例如高屈服强度和均匀伸长率,这是由于利用制造过程的高冷却速率和多次热循环形成了超细共析微观结构。预计该方法将适用于其他共析成形合金系统,并将在航空航天和生物医学行业中应用。
根据相关性理论,控制晶粒尺寸的关键因素包括:(1)ΔTn,成核的临界过冷度;(2)ΔTCS,提供成核过冷的生长固体前方的构成过冷量;和(3)xsd,有效成核颗粒之间的平均间距。然而,在增材制造的金属中,激光熔化区域的尺寸,加上高的热梯度,显著抑制了构成过冷区的范围,使血肉模糊VS哦制造的钛合金难以获得细晶粒尺寸。多个研究小组已经探索了添加溶质元素(如铍、硅或硼)以停止外延生长的可能性。然而,这些溶质元素只会减少增材制造的钛的柱状晶粒的宽度,或仅实现部分柱状到等轴转变。因此,通过传统的晶粒细化模式,增材制造的钛合金中的完全等轴晶粒结构是否可以实际实现仍然是一个悬而未决的问题。
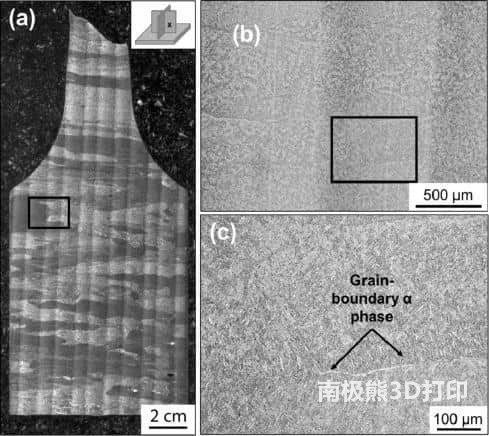
蚀刻微结构的光学显微照片,其中构建方向是水平的。(a)宏观结构的图像,其中构建层是垂直的,长而窄的先β颗粒是水平的。(b)(a)中插图的显微照片,显示构建线(垂直)和先前β颗粒(水平)。(c)(b)中镶嵌的显微照片,显示微观结构的针状特征以及晶界α相的存在。
基于粉末的增材制造(AM)是一种近净成形的生产方法,其中通过将连续的金属原料层熔化到工件上来构建组件。在这些增材制造工艺中,聚焦的激光或电子束以预编程的模式扫描,以熔化金属原料材料并产生所需的形状。材料可以通过在粉末床熔融(PBF)工艺中扩散和选择性熔化单个粉末层来输送到工件,或者在定向能量沉积(DED)工艺中通过同轴喷嘴连续引导到熔池。AM理论上可以产生具有高度复杂几何特征的完全致密的三维零件。它还提供了使用同一台机器制造具有不同几何形状或成分的零件的能力,使该技术对短期生产具有吸引力,否则需要非常昂贵的工具。
PBF 和 DED AM 工艺的特点还在于热输入、热历史和传热方法的显著差异。比较这些基于激光的过程的简化指标是近似线性热输入,其定义为激光功率除以扫描速度。虽然该指标没有考虑激光吸收率的差异或由于环境和边界条件引起的传热差异,但它确实为比较两个过程提供了一个基本的起点。激光-粉末相互作用位置的传热主要通过构建周围未熔化的粉末进行传导。
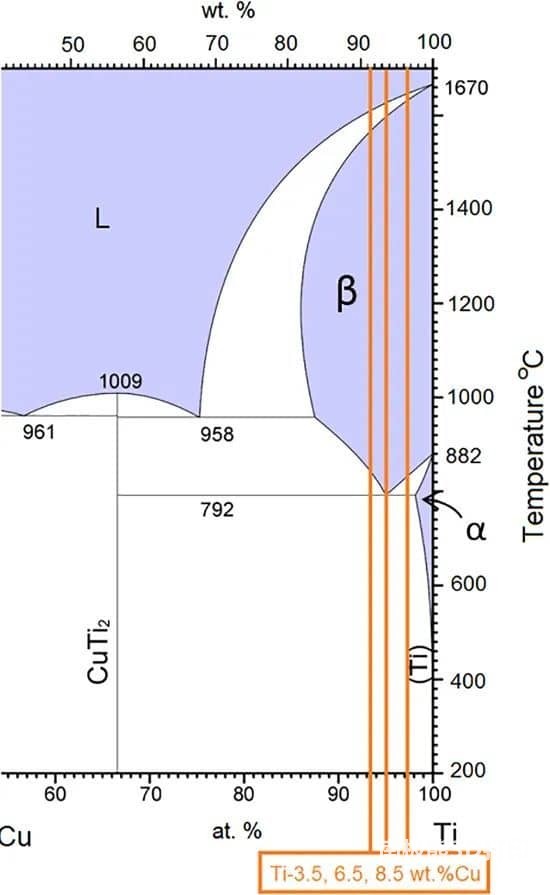
扩展数据图1 Ti–Cu相图。
铜除了具有提炼β相钛晶粒的潜力外,在792℃β→α + Ti2Cu的钛二元合金体系中,铜也是一种典型的共析形成元素。由于铜在钛中迅速扩散,即使在水淬后,也不能轻易防止这种共析反应的发生。这种特性有利于增材制造过程中的高冷却速率,并可能产生非常精细的共析微观结构,从而提高印刷试样的强度和延展性。因此,在本研究中,我们旨在开发增材制造的钛-铜合金(扩展数据图1),以在一步工艺中形成完全等轴β相钛晶粒和超细共析微观结构。
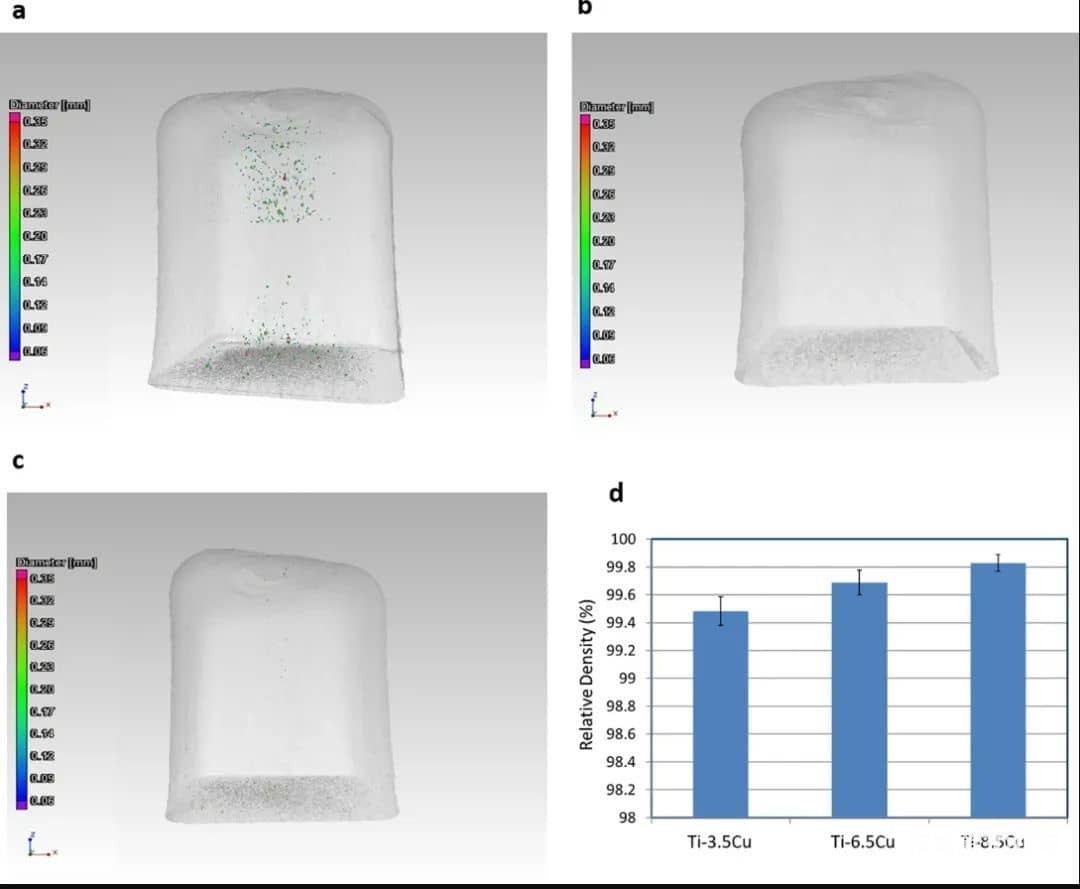
扩展数据图2 xyz坐标系中制造试样孔隙率的三维可视化。

扩展数据图3 Ti–8.5Cu合金沿构建方向的铜含量XEDS结果。
打印Ti–8.5Cu样品的光学显微照片显示完全等轴的前β晶粒(凝固过程中形成的原生Ti晶粒,如图1b所示),没有任何明显的裂纹,且具有小体积分数的封闭孔隙率(见扩展数据图2)。打印后的样品沿建筑方向也具有优异的化学均匀性(参见扩展数据图3)。先前的β晶粒具有双峰分布,平均晶粒尺寸为9.6μm。相比之下,在相同的激光加工条件下,打印态Ti–6Al–4V合金的微观结构以粗柱状晶粒为主(图1a)。可以看出,铜的加入不仅使柱状晶粒完全转变为等轴晶粒,而且使先前的β晶粒细化了两个数量级。通常观察到的外延生长也完全消除,如等轴晶粒的尺寸所示,其远小于约200μm的层厚度(图1b中的黄色箭头)。还值得注意的是,与迄今报道的其他增材制造的钛合金相比,我们目前的工作产生了通过增材制造制造的最小等轴在先β钛合金晶粒,如图1d所示。打印态钛-铜合金的晶粒细化效率源于铜溶质的高容量,以在固-液界面前建立足够大的组成过冷区,当溶质铜围绕第一β相钛树枝状晶粒偏析时形成过冷区(图1c);Ti–8.5Cu合金的Q值为62 K。
这意味着,在相同的激光加工条件下,与Ti–6Al–4V相比,Ti–8.5Cu的增材制造过程中,构成的过冷区的大小要大八倍。充分的结构过冷可以有效地抵消高热梯度的负面影响,并确保可以在结构过冷区中触发非均匀成核事件的波,并且可以实现完全的柱状到等轴转变。根据相互依赖理论,晶粒尺寸也取决于Q。更多的铜溶质更快地提供更高的组分过冷,因此等轴在先β晶粒的尺寸随着铜含量的增加而减小(参见扩展数据图4)。
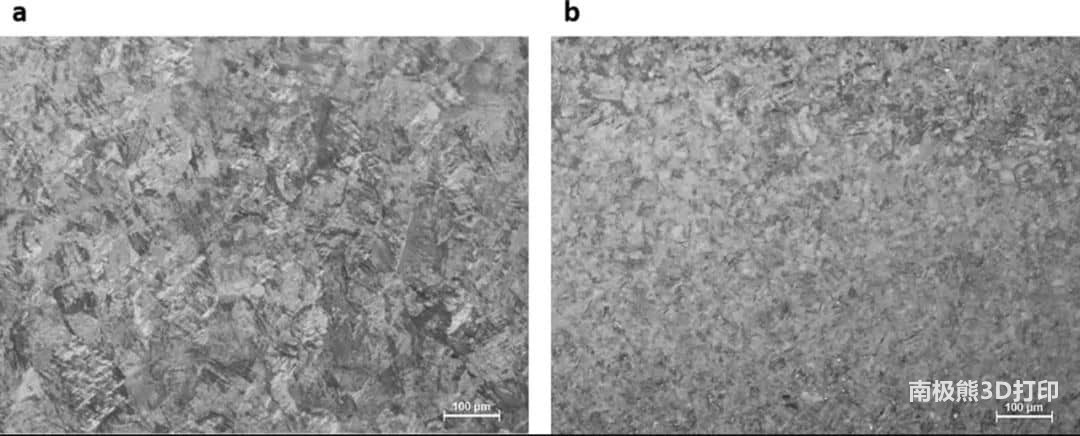
扩展数据图4偏振光学微结构。
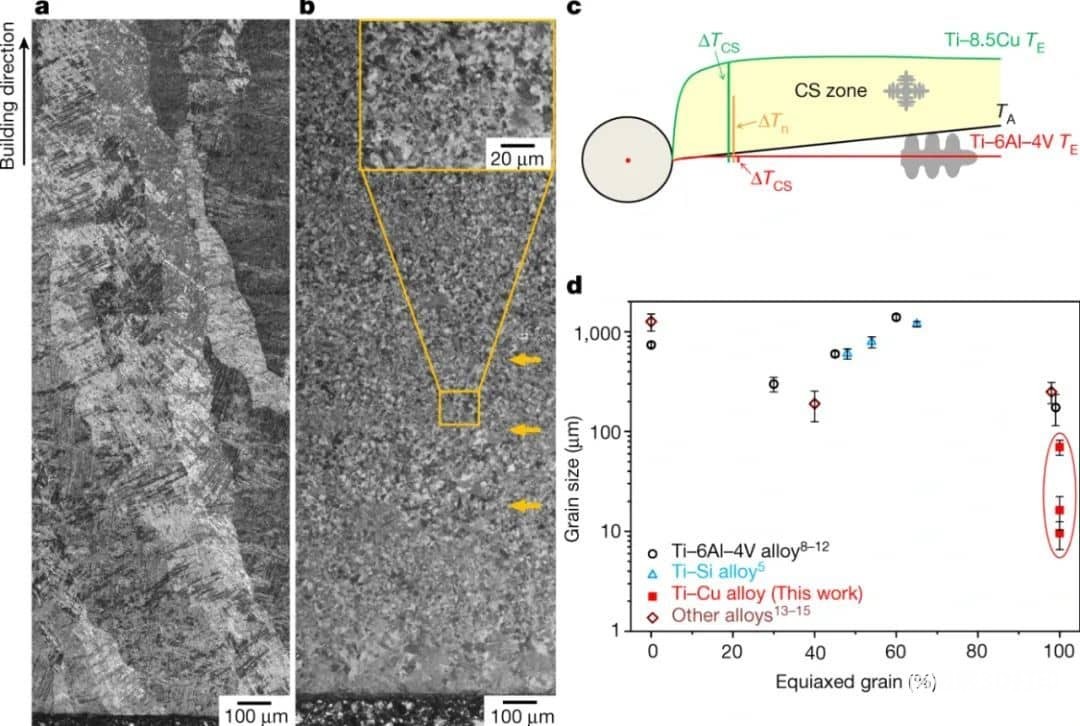
图1 Ti–6Al–4V和Ti–8.5Cu合金的增材制造。
值得一提的是,Scheil–Gulliver凝固路径和凝固范围通常用于预测凝固过程中开裂的可能性。较大的凝固范围通常导致在凝固的最后阶段可用于枝晶间进料的液体较少。在本研究中,基于钛-铜平衡相图,Scheil曲线显示了大于500 K的大冻结范围(扩展数据图5,虚线)。细等轴枝晶的形成可以有效降低热撕裂敏感性,这在铸造合金的先前研究中得到了验证。
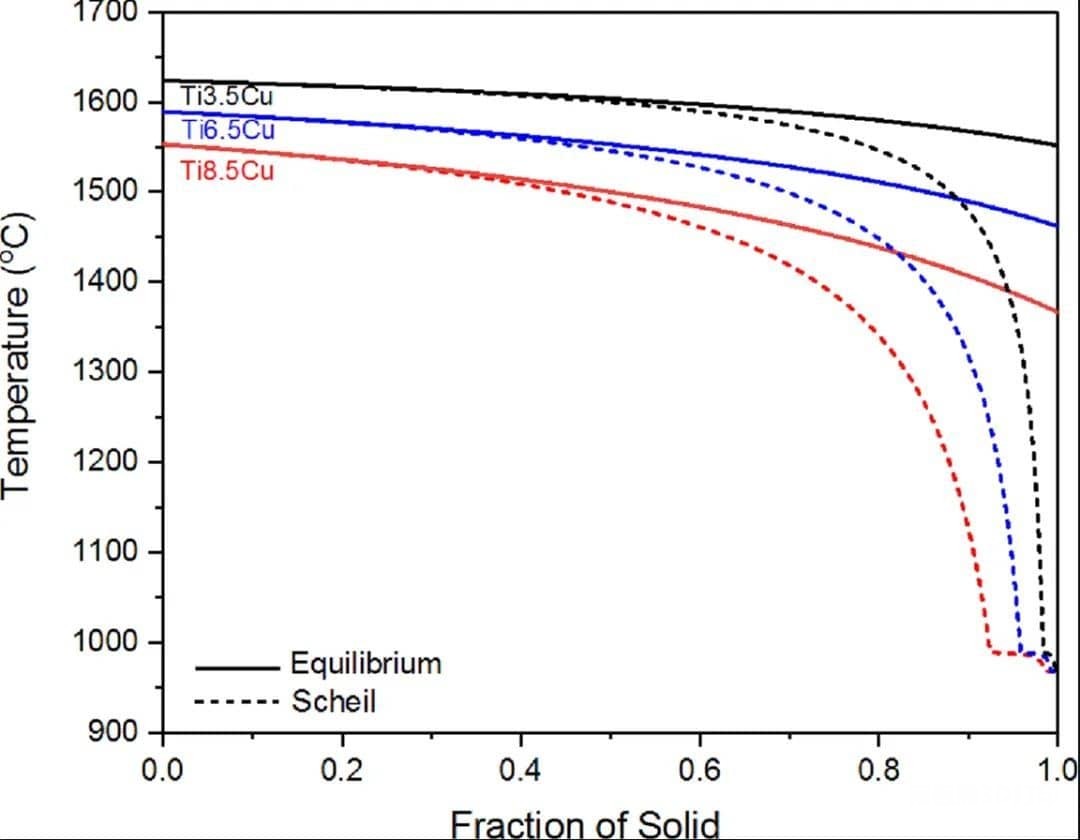
扩展数据图5凝固曲线。
完成液相-β相凝固后,钛的β相(体心立方结构)可在随后的固-固相转变中分解为不同的产物相,这取决于冷却速率。高冷却速率可限制原子的扩散,从而抑制共析耦合生长,导致形成马氏体(α′相钛,六方紧密堆积结构)。钛合金中的马氏体可导致更高的强度但更低的延展性。正如预期的那样,由于增材制造的Ti–8.5Cu合金的单轨中的高冷却速率,观察到马氏体针状板(图2a);然而,连续的逐层制造导致在共析反应温度(792 °C),因此由于散热不足,β相分解的冷却速率随着层数的增加而降低(见图2c)。这种特征热历史可以有效逆转马氏体转变,并产生超细共析薄片(图2b和扩展数据图6)。在其他成分中也观察到类似的现象(参见扩展数据图7)。此外,打印态Ti–8.5Cu合金的平均层间间距为46 nm±7 nm(图2b),比传统制造的水冷(约150 nm)和炉冷(约1μm)样品精细得多。这是因为层间间距受铜原子的扩散长度控制;扩散长度受到快速冷却的显著限制。
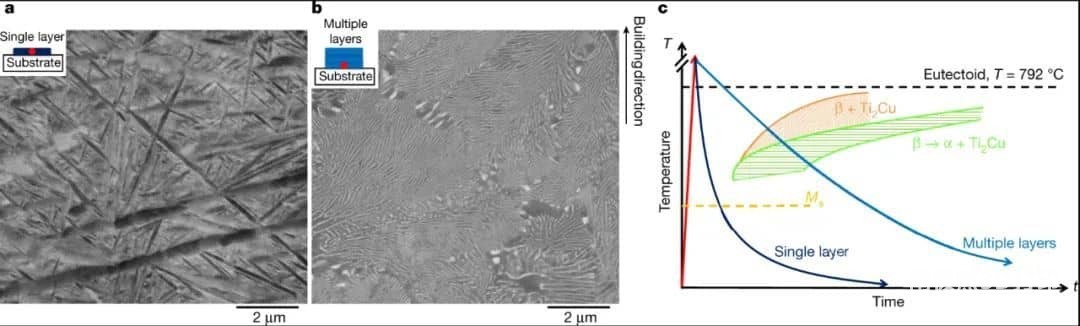
图2 Ti–8.5Cu合金的扫描电子显微镜(SEM)表征。
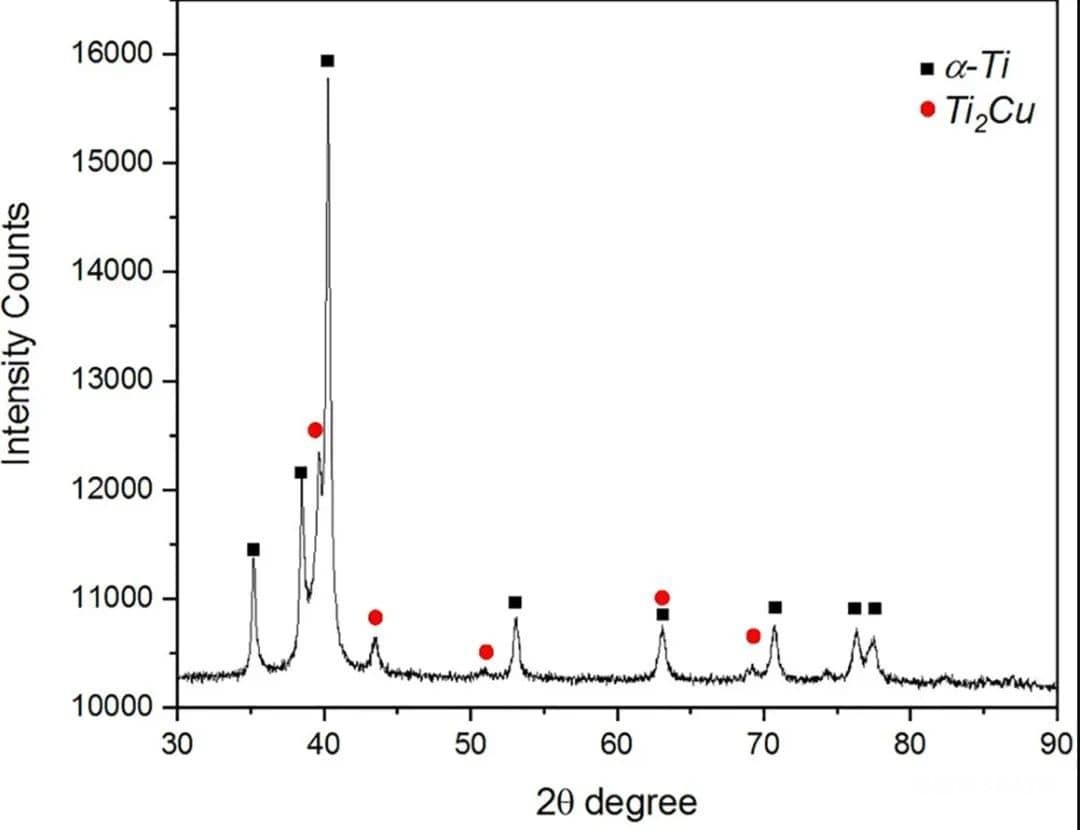
扩展数据图6 XRD光谱。
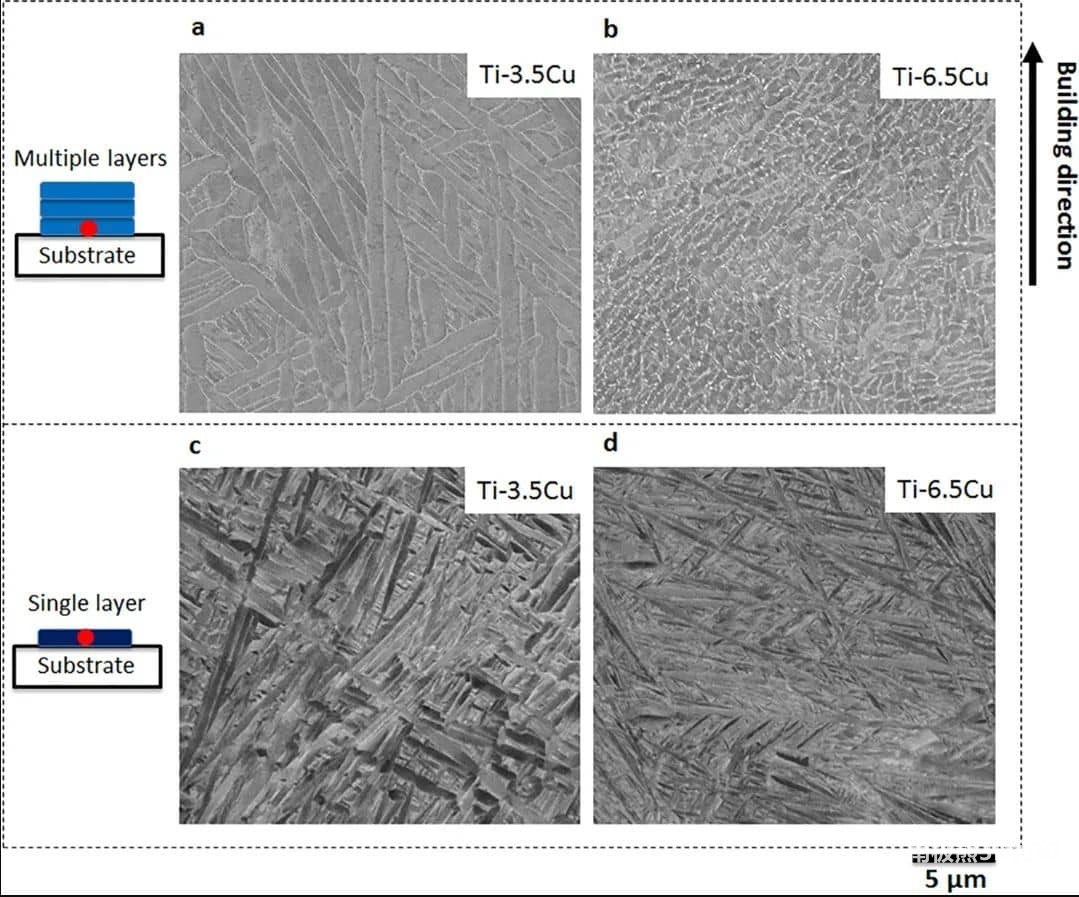
扩展数据图7 BSE图像。
钛合金通常具有非常低的导热率,这可能导致从表面到芯部的层间间距变粗,这是由于在大型、笨重的钛-铜部件的常规正火热处理过程中冷却速率的变化。相比之下,激光金属沉积工艺能够在整个合金中实现相对恒定的冷却速率,从而获得更均匀的微观结构,而不管试样的尺寸如何。还值得一提的是,共析薄片中的铜浓度(图3b–d)偏离了平衡成分。α相钛含有2.8 wt%的铜,并且是过饱和的,因为平衡时铜在α相钛中的最大固溶度为2.0 wt%。这表明,通过优化后热处理,可以实现更实质的沉淀硬化效果,以进一步提高拉伸强度。
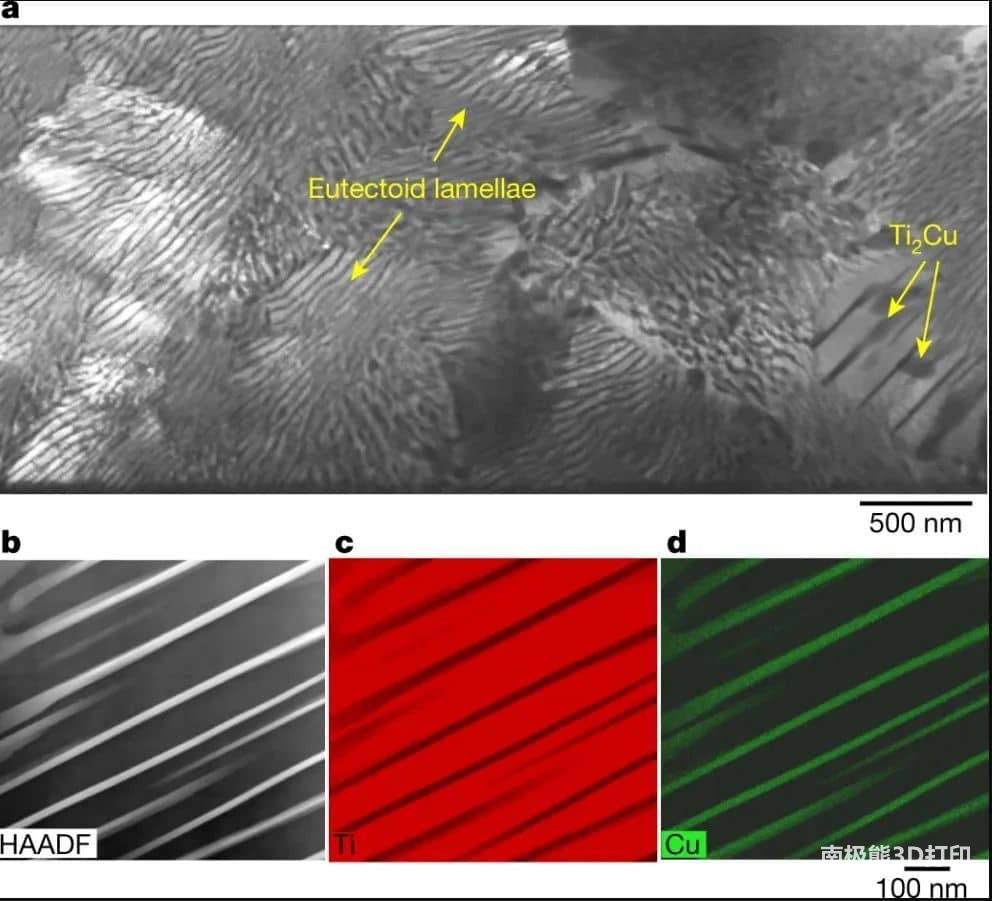
图3 打印态Ti–8.5Cu合金的透射电子显微镜表征。
比较Ti–6.5Cu和Ti–3.5Cu合金,Ti–6.5 Cu中的共析薄片显著提高了强度,但降低了延展性(见图4a)。与Ti–8.5Cu和Ti–6.5Cu合金相比,Ti–8.6Cu具有更高的强度,因为共析薄片的体积分数更高,但由于超共析Ti2Cu颗粒,延展性更低。等轴在先β晶粒的尺寸(图1b和扩展数据图4)和微观结构长度尺度(图2b和扩展资料图7a,b)也可能对机械性能产生影响。断裂表面(图4c–e)显示出从凹坑到典型的晶内断裂形态的变化,这与合金的延展性变化一致。与常规铸造和后热处理方法相比(图4b),具有超细等轴先β晶粒和共析层状结构的打印态钛-铜合金的机械性能显示出优异的偏移屈服强度和延展性组合。其性能也与铸造和锻造的Ti–6Al–4V合金以及激光金属沉积的Ti-6Al-4V合金相当。此外,铜是一种相对低成本的合金元素,钛-铜合金可以用混合元素粉末而不是预合金粉末进行增材制造。
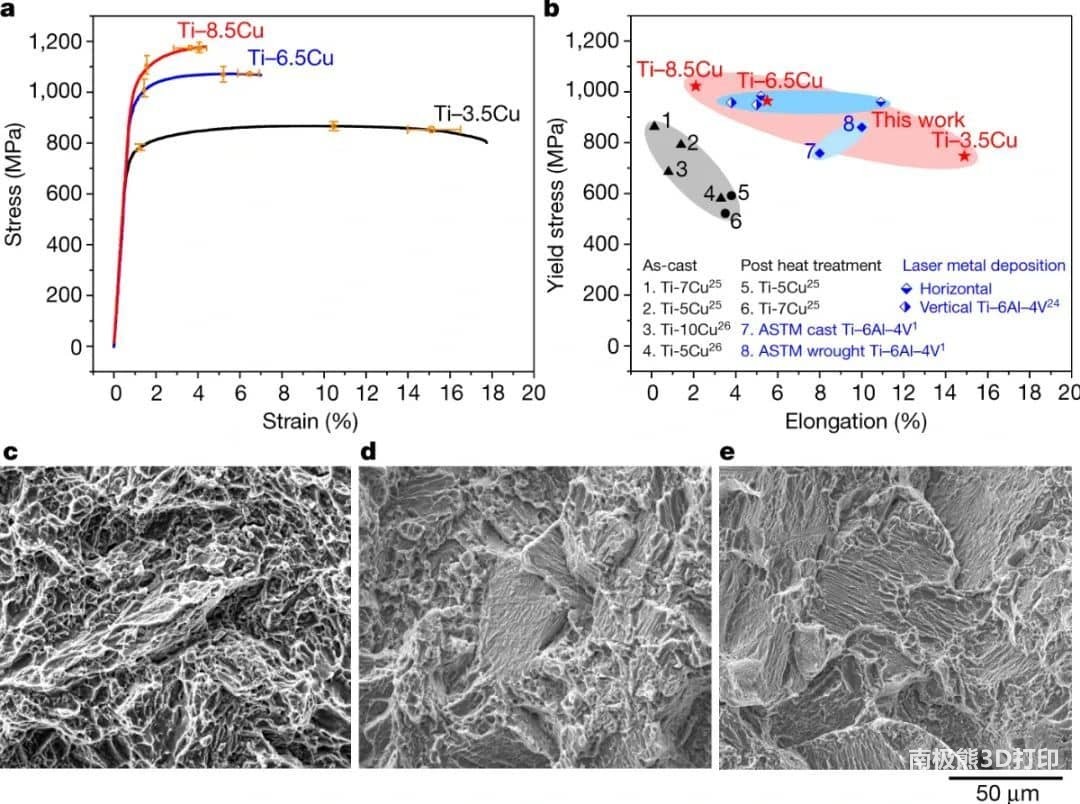
图4 打印态Ti–Cu合金的机械性能。
我们已经证明了一种增材制造钛-铜合金的途径,该合金具有细等轴先β晶粒和超细共析层状结构。我们的实验结果表明,凝固和随后的共析分解可以协同设计,以调整机械性能以适应特定应用。这种使用高Q值合金的晶粒细化方法已在许多合金和凝固过程中得到证明,并在这里被证明是增材制造钛合金的设计方法。该方法也可能适用于其他共析系统,如珠光体钢,其中这些常规合金的机械性能可以通过高性能工程应用的增材制造来提高。
激光金属沉积
将直径在50μm至100μm之间的纯(99.9%)钛和(99.5%)铜球形粉末(分别为TLS Technik和Thermo Fisher)(见扩展数据图8)在Turbula振动台混合器中混合一小时,以达到设计的组合物。激光金属沉积是在通快 TruLaser 单元 7020 上进行的。
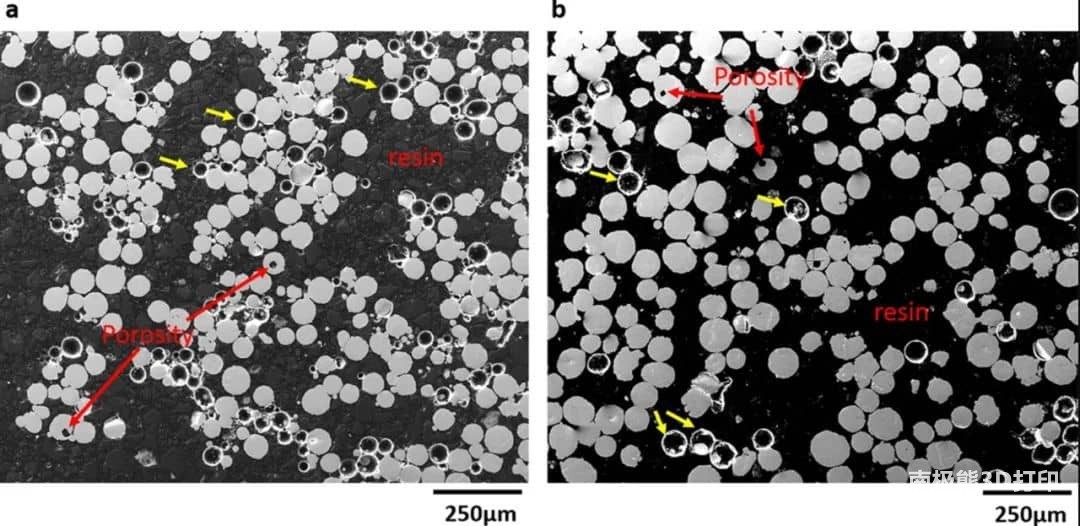
扩展数据图8原料粉末横截面的SEM图像。
拉伸试验
将打印样品加工成规格长度为25 mm,厚度为4 mm的矩形拉伸试样(ASTM标准E8 / E8 M-08的超大尺寸试样)。拉伸测试加载方向垂直于激光金属沉积建筑方向。在室温下进行准静态单轴试验,初始应变率为1.0×10−3 s−1在配备非接触式激光引伸计的通用测试设施(MTS810,100 kN)上。对每种组合物测试了五个拉伸试样(见扩展数据图9)。然后将结果与标准尺寸试样的ASTM标准进行比较。
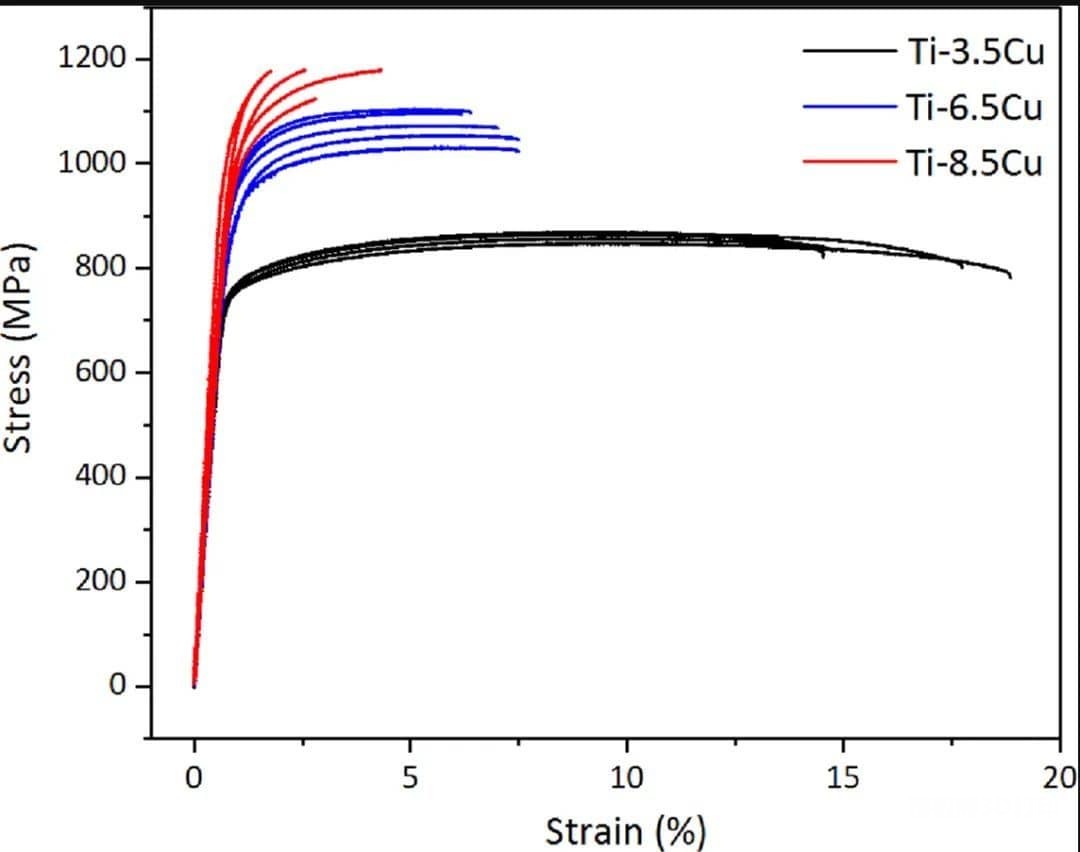
扩展图9扩展数据图9工程应力-应变曲线。
碳对拉伸性能的影响
下图显示了碳对合金拉伸性能的影响。所有三种碳合金的平均屈服和抗拉强度均有所提高,但与Ti-6Al-4V相比,碳添加量为0.1 wt.%时,最大提高了9%。在此碳水平以上,强度降低并发生严重的拉伸脆化。
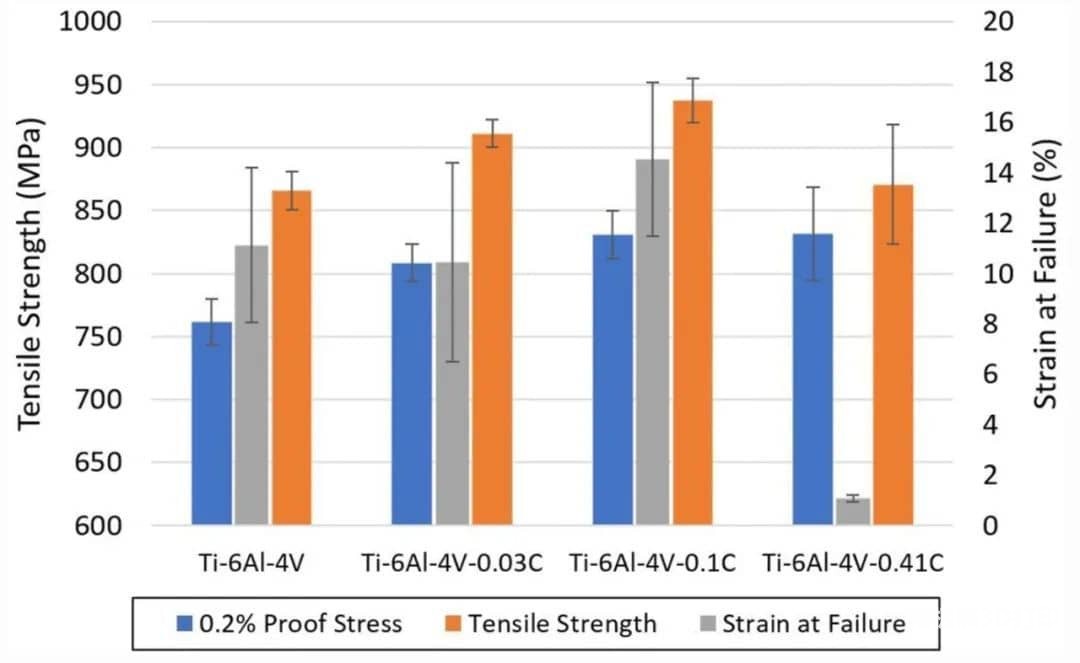
微量碳对Ti-6Al-4V拉伸性能的影响。
这种低延展性与TiC增强钛金属基复合材料相似,并且与这些研究一致,Ti-6Al-4V-0.41C的微观结构揭示了丰富的TiC。Da Silva等研究了TiC对Ti-6Al-V-TiC复合材料拉伸性能的影响,发现延展性受TiC断裂速率和随后的空隙增长和聚结的控制。TiC的弹性非常有限,因此在拉伸载荷下不可避免地会开裂和空隙的产生。最近,这种失效模式在用硼化物增强的Ti-6Al-4V中得到了证明。众所周知,碳在固溶体中会显着增加强度,而碳化物的存在提供的贡献有限。这与目前的发现一致,即即使在最小的痕量水平上故意添加碳,也能将Ti-6Al-4V的强度提高到与Ti-6Al-4V-0.41C相似的水平,而不会降低延展性。很明显,Ti-6Al-4V-C合金的强度和延展性的令人满意的组合可以在低于该水平的水平上实现,该水平容易形成大型碳化物。
来源:Additive manufacturing of ultrafine-grained high-strength titanium alloys, Nature, doi.org/10.1038/s41586-019-1783-1
参考文献:Trace carbon addition to refine microstructure and enhance properties of additive-manufactured Ti–6Al–4V. JOM 70, 1670–1676 (2018).
(责任编辑:admin)
最新内容
热点内容