混合金属增材制造:最新研究进展(1)
时间:2022-03-17 13:34 来源:混合金属增材制造 作者:admin 阅读:次
特别强调了增材制造与成形工艺的结合,以实现以下两个目标:(i)增加金属增材制造的适用性领域,克服其生产率低、冶金缺陷、表面粗糙质量和尺寸精度不足等方面的局限性;(ii)增加传统成型工艺的灵活性并促进其新应用。
1. 介绍
混合制造(HM)是指将不同的技术结合在一起,以克服各自的局限性并从其内在优势中获益的制造过程(Chu, 2014)。HM起源于减材制造(SM),但随着时间的推移,它的概念和应用逐渐融合了其他传统制造技术,如焊接、组装和成型(Zhu等, 2013; Lauwers等,2014)。
本文关注的是一种新型杂交技术的出现,其根源是金属增材制造(MAM),这是一种通过添加原料金属一层一层地建立具有复杂几何形状的零件的技术。其目标是通过与其他制造技术的结合,克服其生产率低、冶金缺陷、粗糙表面质量和尺寸精度不足等限制,从而增加MAM的适用性领域。相反,基于MAM的杂交也可以被视为增加灵活性和减少传统制造过程中的材料浪费的一种方法(Lorenz, 2015)。
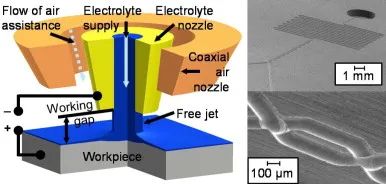
空气辅助射流电解加工原理及其在金属零件柔性高精度表面结构中的应用。
空气辅助射流ecm的原理如上图(左)所示。电解液射流垂直于工件表面喷射。在与周围空气的相互作用下,形成一个封闭的电解自由射流。因此电流被射流限制在一个有限的区域内,电流密度高,局部去除程度高,腐蚀局部化程度高,表面质量好。在空气辅助射流电解加工中,可以使用连续电流,与脉冲电解加工工艺相比,产生更高的去除率。原因是,使用射流可以提供充足的新鲜电解质,并能很好地去除反应产物。通过改变喷嘴位置和设置电流,可以很容易地生成微结构表面和复杂的三维微几何形状。
金属混合增材制造的最初发展是基于利用多种热能资源,并将MAM与金属切削相结合,以提高制造零件的生产率和质量。这些发展导致了第一个混合金属增材制造系统在2010年中期的商业化。
MAM与金属成形的结合是最近才出现的,最初的目的是通过局部塑性变形改善沉积材料层的形状,同时为构件提供更高的刚度和耐磨性。然而,基于MAM与成形相结合的杂化技术近年来得到了迅速发展和扩展,包含了从板料和大块金属成形过程中获得的新概念。
在这种情况下,本文的目的是对这一新出现的与MAM上的根杂交类型的最新进展进行综述。其内容可能被视为一个扩展先前的评论领域的HM如发表的Zhu等(2013)和Lauwers 等(2014),主要是集中在HM的根源主要加工原料,与减去制造业和其他传统的制造技术。
本文除引言外,分为三个主要部分。第一部分概述了不同的增材制造工艺,并讨论了其工作原理和主要特点,重点是那些适用于金属。第二部分回顾了基于金属混合增材制造的新发展的混合制造(HM)的早期分类。第三部分概述了金属混合增材制造领域的主要研究成果,特别关注于MAM与金属成形的结合,据笔者所知,Merklein等人(2016)的一篇论文仅对这一领域进行了部分论述。
2. 金属增材制造
2.1. 发展时间表一览
增材制造的第一次发展是在20世纪80年代早期,由Hideo Kodama完成的,他致力于利用紫外线固化聚合物和创造固体物体(Kodama, 1981)。然而,增材制造被认为是在20世纪80年代末出现的一种技术,由Charles Hull(1990)发展的立体光刻(SLA)和Scott Crump(1991)发展的熔融沉积材料(FDM)。这两种工艺都是在局部热源的帮助下,通过在薄的水平截面上分层聚合物来制造三维零件;在SLA中使用紫外光,在FDM中使用喷嘴热端。
20世纪90年代早期,第一台设备的商业化和使用允许内部制造聚合物原型,大大缩短了交付时间,这也解释了增材制造最初被称为“快速原型制造”的原因。从那时起,设备和材料方面的创新使得增材制造的应用领域得以显著扩展,从原型机扩展到面向客户的机械、电子、航空航天、汽车和医药等领域,使用了包括聚合物、陶瓷、复合材料和金属。
金属增材制造是最常用的工程材料,直到20世纪90年代初Ely Sachs及其同事开发了粘结剂喷射技术,金属增材制造才开始使用(Sachs等人,1993年)。使用喷墨式的打印机头喷射粘合剂,将连续的金属粉末层与粘合剂喷涂在一起,并将它们粘合成三维零件,这解释了术语“三维打印”(或简称为“3D打印”)作为“增材制造”的同义词的起源。
20世纪90年代中期,能够提供加工烧结或熔融状态金属粉末所需的大量能量的激光器的发展,为称为直接金属激光烧结(DMLS)的过程的发展铺平了道路(shellbear和Nyrhilä, 2004年),以及第一个金属增材制造(MAM)设备的商业化。DMLS是选择性激光烧结金属技术(SLS)的延伸,该技术在20世纪80年代末由Carl Deckard(1989)开发,用于聚合物的增材制造(Ning等, 2005)。
20世纪90年代末,瑞典的Arcam公司推出了一种用于金属增材制造的电子束热能源(Larson, 1998)。
与激光的发展同时,Dickens等人(1992)提出了一种名为“3D焊接”的工艺,通过对传统焊接机进行改造并将其与机器人相结合,可以生产出接近成品的金属零件。该工艺为电弧和计算机辅助制造(CAM)软件的结合开辟了道路,以控制刀具路径以及焊机和送丝机的起止点,这些都是将模型转化为三维金属零件所需的。虽然Dickens等(1992)和Prinz &Weiss(1993)被认为是第一个开发电弧丝增材制造(WAAM)的人,但使用电弧作为热能来源和焊丝作为原料制造大型部件的工作原理在以前已经成功应用。
自这些开创性的突破以来,MAM领域有了重大的新发展和应用。在接下来的文章中,作者对不同的增材制造工艺进行了分类,解释了它们的工作原理,并讨论了其主要特点,重点是那些适用于金属的。
Wang等人将磨料电化学多丝切片作为进一步组合应用于太阳能硅锭加工,以提高表面完整性和材料去除率。
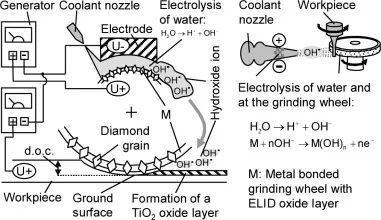
电解过程中修整(ELID)磨削的变种和应用实例。
在ECM和磨削的工艺组合中,Ohmori等人提出的电解过程中修整(ELID)技术也代表了一种主要的混合方法,具有不同的焦点。对于基础技术,如上图所示,砂轮上基于ECM的阳极氧化层生长的自我调节和通过磨削过程(ELID循环)同时机械去除该层结合了两种不同的物理活性原理。此外,冷却液中的氢氧化物离子和ELID氧化物颗粒可对工件侧的材料去除(降低工艺力、提高材料去除率)和表面质量(降低表面粗糙度值——“抛光研磨”具有镜面外观)产生积极影响。
2.2 分类
EN ISO/ASTM 52921(2015)标准将增材制造工艺分为七个不同的类别(图1)。其中四个类别现在被用于制造金属部件;粘结剂喷射(BJ),粉末床融合(PBF),薄板分层(SL)和直接能量沉积(DED)。其他三个类别;还原光聚合法(VP)、材料喷射法(MJ)和材料挤压法(ME)是间接增材制造技术的主要应用领域。
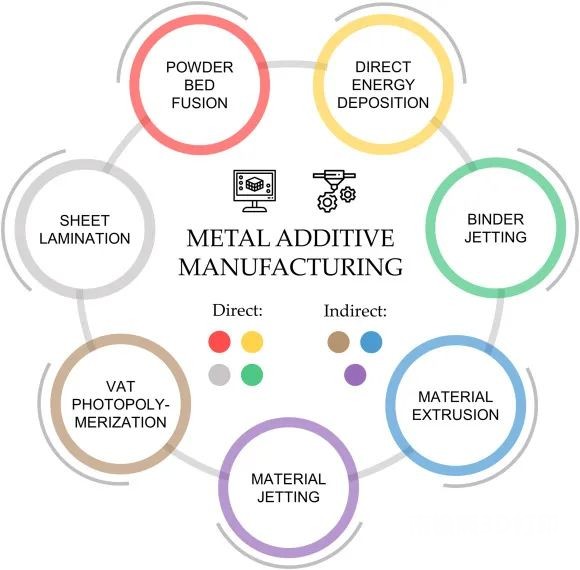
图1 增材制造的分类及其对制造金属部件的直接和间接适用性的识别(根据EN ISO/ASTM 52921(2015)标准修订)。
直接和间接金属增材制造(MAM)工艺之间的区别与对成品零件的使用有关。在直接MAM中,金属构件是最终产品,直接按照设计规范和要求制造。在间接MAM中,构建的部件由主模式或工具组成,随后被传统制造工艺用于获得最终的金属部件(Montero等人,2020年)。
因此,间接MAM无法与传统制造工艺分离,如熔模铸造、砂型铸造(Mitra 等,2019)、压铸和注射成型(León-Cabezas 等,2017),主要集中于非金属材料的3D打印,如聚合物、光聚合物、陶瓷、蜡、树脂和复合材料。
2.2.1 直接MAM
直接MAM包括四类,现在被用来建造金属部件(图1);粘结剂喷射(BJ),粉末床融合(PBF),薄板分层(SL)和直接能量沉积(DED)。
粘结剂喷射包括用液体粘合剂通过喷墨式打印机在搭建平台上喷涂固定的粉末松散床,以便将粉末一层一层地粘在一起形成一个横截面(Sachs等人,1993年)(图2a)。在每一层创建之后,建造的平台被降低,以允许下一层的形成,这个过程继续进行,直到获得一个低强度和大约60%的相对密度的“绿色部分”。然后在受控的气氛中加热绿色部分,去除粘合剂,并将单个粒子烧结(粘结)成一个“完全致密”的金属部分。
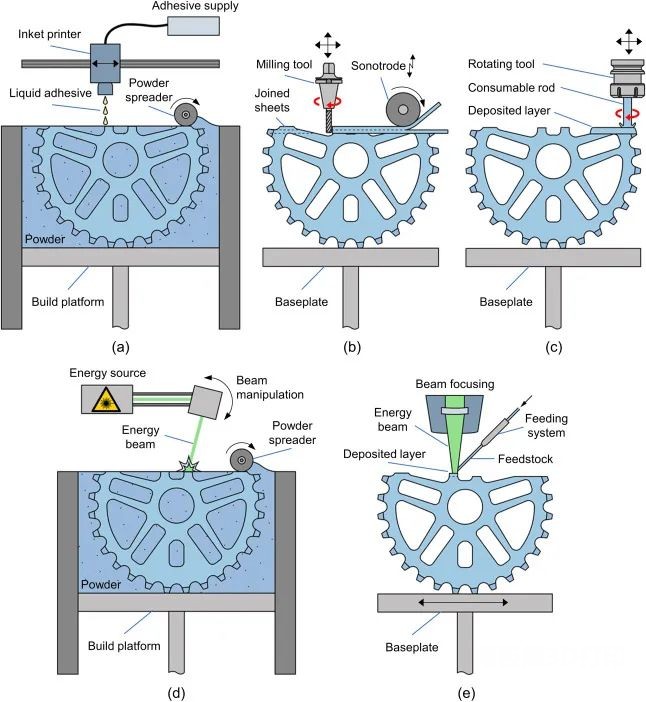
图2 介绍了几种增材制造的工作原理和主要术语。
(a)粘结剂喷射(BJ);
(b)板层(SL);
(c)摩擦堆焊(FS);
(d)粉床融合;
(e)直接能量沉积(DED)。
烧结过程中密度的增加是通过收缩和尺寸精度的损失获得的,这被认为是粘结剂喷射的主要缺点(Ziaee和Crane, 2019)。
(责任编辑:admin)
最新内容
热点内容