3D打印高新技术——航空航天器零部件
时间:2021-09-07 08:35 来源:中国有色金属报 作者:admin 阅读:次
导读:航空航天器设备是3D打印最具前景的应用领域之一。第一,航空航天设备具有多品种、小批量的特点,尤其在试制阶段许多零部件都需要单件定制,若采取传统工艺则周期长、成本高,3D打印可以实现低成本快速成型;第二,出于减重与强度要求,航空航天设备复杂结构件或大型异构件的比例越来越高,若采用传统的“锻造+机加工”方式,则所需工序繁多、工艺复杂,甚至根本无法直接加工,而3D打印在复杂部件加工方面具有明显优势;第三,采用传统工艺加工飞机零部件的原材料利用率仅约10%,其它部分都在铸模、锻造、切割和打磨过程中浪费了,而3D打印的增量制造原材料利用率可达到90%以上。
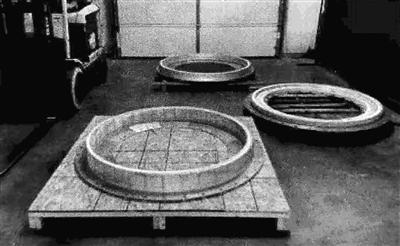
△梅尔德公司打印的3D铝合金环件
钛合金在国外3D打印航空航天器产品中应用
航空航天器设备是3D打印最具前景的应用领域之一。第一,航空航天设备具有多品种、小批量的特点,尤其在试制阶段许多零部件都需要单件定制,若采取传统工艺则周期长、成本高,3D打印可以实现低成本快速成型;第二,出于减重与强度要求,航空航天设备复杂结构件或大型异构件的比例越来越高,若采用传统的“锻造+机加工”方式,则所需工序繁多、工艺复杂,甚至根本无法直接加工,而3D打印在复杂部件加工方面具有明显优势;第三,采用传统工艺加工飞机零部件的原材料利用率仅约10%,其它部分都在铸模、锻造、切割和打磨过程中浪费了,而3D打印的增量制造原材料利用率可达到90%以上。
波音公司是率先将3D打印技术用于飞机设计和制造的国际航空航天器制造企业,已累计利用3D打印技术生产了300多个不同的小型零部件。
2012年,通用电气公司收购了专门开发激光烧结金属粉技术的莫里斯技术公司,用来为其Leap系列发动机制造零部件。普惠公司也投入数百万美元联合康涅狄格大学成立了增量制造中心。美国国家航天航空局正在使用3D打印机生产航天器的引擎部件,并计划将打印设备发射到国际空间站,以期宇航员能够自给自足,利用空间站上的原料直接生产所需品,改变完全依赖地面供给的补给模式。
2014年8月31日,美国宇航局的工程师们完成了3D打印火箭喷射器的测试,本项研究在于提高火箭发动机组件的性能,由于喷射器内液氧和气态氢一起混合反应,燃烧温度可达约3315℃,可产生约9吨推力,验证了3D打印技术在火箭发动机制造上的可行性。
制造火箭发动机喷射器需要精度高的加工技术,如果使用3D打印技术,就可以降低制造上的复杂程度,在计算机中建立喷射器的三维图像,打印的材料为金属粉和激光,在较高温度下,金属粉可被重新塑造成我们需要的样子。火箭发动机中的喷射器内有数十个喷射元件,要建造大小相似的元件需要高的加工精度,该技术测试成功后将用于制造RS-25发动机,作为美国宇航局太空发射系统的主要动力,该火箭可运载宇航员超越近地轨道,进入更遥远的深空。马歇尔中心工程部主任克里斯认为,3D打印技术在火箭发动机喷油器上应用只是第一步,我们的目的在于测试3D打印部件如何能彻底改变火箭的设计与制造,并提高系统的性能,更重要的是可以节省时间和成本,不太容易出故障。
2014年9月,美国国家航空航天局(NASA)预计完成首台成像望远镜,所有元件几乎全部通过3D打印技术制造。NASA也因此成为首家尝试使用3D打印技术制造整台仪器的单位。这款太空望远镜功能齐全,其50.8mm的摄像头使其能够放进立方体卫星(一款微型卫星)当中。据了解,这款太空望远镜的外管、外挡板及光学镜架全部作为单独的结构直接打印而成。
这款长50.8mm的望远镜将全部由铝和钛制成,而且只需通过3D打印技术制造4个零件即可,相比而言,传统工艺所需的零件数是3D打印的5-10倍。此外,在3D打印的望远镜中,可将用来减少望远镜中杂散光的仪器挡板做成带有角度的样式,这是传统制作工艺在一个零件中所无法实现的。
2018年12月3日,一台名为奥根纳特的突破性3D打印装置,被执行“58号远征”任务的“联盟MS-11”飞船送往国际空间站。打印机由英维特罗的子公司“3D生物打印解决方案”公司建造。英维特罗随后收到了从国际空间站传回的一组照片,通过这些照片可以看到老鼠甲状腺是如何被打印出来的。
2021年3月,法国赛峰集团旗下赛峰起落架系统公司使用SLM解决方案公司的选区激光熔化(SLM)技术制造了公务机前起落架的组件,为公务机打造首个3D打印的大型钛合金前起落架壳体。
具体来说,他们使用金属增材制造来制作将载荷从机轮传递到飞机结构的组件之一,该组件在起飞后将收回机身内,尺寸为455mm×295mm×805mm,对于金属增材来说是相当大的体积。采用该生产方法后,赛峰集团将组件的总重量降低了15%,同时又保持了力学性能。该组件是由钛材料3D打印的,并承受高应力。
飞机的起落架显然具有一些关键功能,即用于起飞、着陆和制动。赛峰集团着陆系统公司特别感兴趣的是制造一种必须能够承受机轮传递应力的组件,是一个承受很大压力的结构元件:它必须能够在枢轴上旋转,以使起落架在飞机下方收回,并且它必须吸收来自飞机机轮的机械应力。在这种性质和尺寸下的一个零件上使用增材制造是世界首次。
该3D打印组件是钛合金起落架壳体,并在SLM解决方案公司金属机床SLM 800上打印,该机床以其四激光技术和可靠性而闻名。团队使用增材制造,不但总质量降低了15%,还缩短了生产时间。
在材料方面,选择钛是因为其坚固性和耐腐蚀性。传统上,零件是用铝材设计、通过锻造工艺制造的,但是考虑到选择面向3D打印的设计,这种金属是不合适的。零件的70%的表面没有经过机械加工,仅加工了功能性表面,增加了箱体的寿命。目前,赛峰集团起落架系统公司计划在2022年测试3D打印组件,这是认证过程中的关键一步。
中国3D打印的钛合金航空航天器产品
中国的大型钛合金结构件激光成形技术具有国际领先水平,是目前世界上唯一掌握了飞机钛合金大型主承力结构件激光快速成型技术并实现装机应用的国家。另据媒体报道,在舰载机、四代机等新型军用飞机的研制过程中,3D打印技术已经发挥了重要作用,承担了包括起落架在内的钛合金主承力构件的试制任务。
2020年5月5日,中国首飞成功的长征五号B运载火箭上,搭载着新一代载人飞船试验船,船上还搭载了一台“3D打印机”。这是中国首次太空3D打印实验,也是国际上第一次在太空中开展连续纤维增强复合材料的3D打印实验。
3D打印的铝合金航空航天器产品很多,有铝合金的,也有铝基复合材料的,简述几则产品如下:
1. 美国梅尔德公司的大型部件。该公司于2019年采用其独创的3D打印技术以6061铝合金粉打出直径超过1400mm的大型环件(如图),在3D打印零件领域具有里程碑意义。所采用的技术为一种固态工艺,在加工过程中材料不会达到熔化温度,产品中的残余应力很低,具有精准的尺寸与外形。
2. 2015年6月俄罗斯技术集团公司以3D打印技术打造出一架铝材无人机样机,打印时间31小时,质量3.8kg,翼展2400mm,飞行速度90km/h-100km/h,续航能力1-1.5小时。
3. 10m级高强铝合金重型运载火箭连接环样件,2021年1月,国家增材制造创新中心、西安交通大学卢秉恒院士团队利用3D打印技术制成了世界上首件10m级高强铝合金重型运载火箭连接环样件。该样件利用电弧熔丝增减材一体化制造技术,在整体制造的工艺稳定性、精度控制及变形与应力调控等方面均实现了重大技术突破。
10米级超大型铝合金环件是连接重型运载火箭贮箱的简段、前后底与火箭的箱间段之间的关键结构件。该样件重约1吨,创新采用多丝协同工艺装备,制造工艺大为简化、成本大幅降低,制造周期缩短至1个月。
目前,采用增减材一体化制造技术成功完成超大型环件属国际首例,该成果将会助力增材制造为中国航天事业发光发热,同时,为中国航天事业中重大零件的快速制造提供了技术支撑。
(责任编辑:admin)
最新内容
热点内容