综述:SLM制造铝合金的显微组织和性能(一)(2)
时间:2021-09-02 08:35 来源:江苏激光联盟 作者:admin 阅读:次
2.1. Al合金的AM制造
AM制造过程显著的不同于传统的铸造工艺,其显著的优点在于减少了制造步骤和浪费的大大减少。金属的AM制造会导致形成独特的显微组织和机械性能,这是传统的机械制造所不能实现的。然而,传统的铸造在整个铸造过程中是不能实现快速冷却的,快速凝固主要限制在小或薄的部件的制造上。相反,SLM AM制造则呈现出优异的特点,其快速加热仅仅限于一次时只针对一个小范围的材料。同激光辐照的时间非常短耦合在一起,就可以实现快速加热和快速冷却(可以达到10exp(3)–10exp(8) K/s)。这就导致了加工状态的不同,以及随后的冶金反应也不同,同传统的铸造工艺相比较的话。
SLM AM制造的一个最为重要的特征就是快速加热和快速冷却。铝合金的快速凝固组织可以沿着三条线进行详细的描述。首先,成分的变化时快速凝固的时候的过冷程度所造成的。在更加极端的情况下会造成无分区凝固(即无偏析)。其次,单独的相细化会发生,此处显微组织的细化非常接近凝固界面的速度。第三,形成非稳态相,如Al6Fe在Al-Fe 中和 Al6Mn 在Al-Mn合金中形成,包括在一些快速凝固合金中的非晶结构的形成以及准晶相的形成,取决于合金元素的添加,甚至是在中等冷却速率的条件下形成。独特的显微组织结构的特征在铝合金中会发现,主要是快速凝固后发生,包括细小的显微组织,如枝晶间距的减少,偏析模式的减少、在初生Al中合金元素固溶度的扩大、非稳态晶的相变、非晶结构和准晶等。
晶粒的结构对材料的性能的影响是深远的。晶粒尺寸极大的影响到机械性能,这一点通过Hall–Petch关系式来说明(σy=σ0+k/d ), 这一关系式表明多晶的屈服强度(σy ) 同晶粒尺寸 (d )的平方根成反比,此处的σ0 为摩擦应力(同晶粒尺寸无关),K是材料常数。在SLM制造的过程中高的冷却速率是产生细小晶粒的便利条件,从而可以同传统铸造相比具有有益的机械性能。铝合金进行SLM制造时的晶粒尺寸一般为~≥50 μm,比较典型的属于Hall–Petch 关系式的应用范畴,从而导致强度的增加。然而,许多晶粒具有生成柱状晶而不是等轴晶的倾向(在制造方向)。因此,机械性能就有可能是各向异性的,这一点对研究人员来说对于晶粒尺寸的特定分析也是非常重要的。合金强化也可以通过控制共晶、析出相、弥散强化、金属间化合物和非稳态相的形成来实现。
采用铝粉末进行SLM制造也是非常特别的,这是因为铝合金的热导率高和低的比重,使得适合制造轻质和热控制的部件(如吸热和热交换器件)。然而,大多数可打印的铝合金仍然是强度比较低的近共晶AlSiMg为基础的合金,而不是高强度的变形合金。另外一类可打印的铝合金为含有高Ti含量的2xxx (Al-Cu)合金系,如 Aeromet所发展的A20X™ (Al-4.5Cu-0.3Mg-0.7Ag-3.5Ti) 含Sc和Zr的5xxx (Al-Mg)系合金,如 空客公司所发展的Scalmalloy® (Al-4.5Mg-0.6Sc-0.5Mn-0.3 Zr),HRL实验室所发展的含高Zr的7xxx (Al-Zn) 合金,如 Al-7A77 alloy (Al-5.5Zn-1.5Cu-2.5Mg-1.5Zr)。
直到今天,AM制造的Al合金的研究活动同其他合金相比,还是受到限制的。这里有大量的因数限制着铝合金的打印,如粉末中容易形成氧化物、粉末的流动性差、对常见的激光器的波长铝合金吸收率低、材料的导热率高等。尤其是,铝合金的高热导率和低的激光能量吸收使得需要较高的能量才能实现粉末的熔化。然而,这样做的话也导致合金的不均匀的汽化,如Zn、Mg等元素具有较高的蒸汽压,会优先汽化。这就导致了最终打印部件的不均匀性。
大多数含Sr的合金目前还不属于商业化的合金,它们的合金粉末目前只有少数的供应商能够提供。进一步的,典型的高强度变形铝合金(拉伸强度达到500MPa以上且延伸率在热处理后可以超过10%)在打印的时候加工性能很差,这是因为热裂纹的存在。结果,采用新的办法来提高铝合金的可打印性能就非常重要。下图3总结了传统铝合金和当前采用SLM进行打印的铝合金的拉伸强度的对比图。该图非常清晰的显示了通过SLM制造的铝合金可以获得几乎同传统制造工艺相似的拉伸强度,但延伸率却下降,这一点随后再详细讨论。
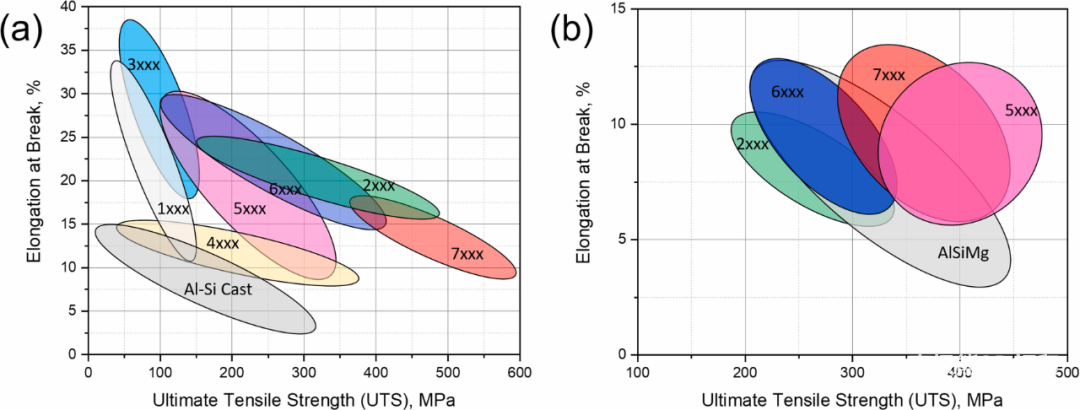
▲图3 (a)传统制造的铝合金和(b)SLM制造的铝合金的拉伸强度图
3. Al-Si合金的AM制造
近共晶 Al-Si 合金具有杰出的流动性、高的热导率、低的热膨胀系数和优异的铸造性,因此大多数的铝合金在采用SLM制造的时候基本都是亚共晶Al-Si (7–12 wt%)-Mg (>1 wt%)合金。少量的公开文献会使用具有较高Si含量的过共晶,基本上是将Si和Al粉末混合进行。
3.1. 制造的Al-Si合金的显微组织
3.1.1. 亚共晶Al-Si合金
在凝固过程中显微组织的演变是决定SLM制造的部件的机械性能的一个关键因数。在SLM制造的亚共晶Al-Si合金中主要的显微组织为初生Al晶粒和共晶Si相。一个通常的SLM制造的铝合金的初生Al晶粒的形貌为外延生长的柱状晶(见图4a)。这一柱状晶,平行于制造方向,是AM制造的金属部件产生各向异性的主要原因。外延生长的柱状晶的生长原因是在材料沉积的过程中早先凝固的层部分熔化熔化的结果,然后在随后的制造层中连续生长的结果。这就造成了熔池中足够的热梯度,沿着释放的潜热来阻止在凝固前沿的新相的孕育。EBSD研究显示这些柱状晶呈<001>显微结构生长,由于在陡峭的温度梯度(快速加热和快速冷却形成的)条件下的定向传热导致长的柱状晶的形成,在凝固过程中的共晶周围的边界形成。Wu等人注意到这些长的胞的形成实在柱状晶之内形成的,并不会改变生长方向,当在共晶沉积和在现存的Al胞中形成的条件下,见图4e和f所示。在他们的工作中,报道的柱状晶的尺寸达到了几百个μm,其胞的尺寸为几个μm。他们的研究表明外延生长存在于共晶的Si和Al之间(描述为(111)Si||(200)Al))。在传统铸造的时候,当冷却速率小于10 K/s的时候,Si颗粒生长成针状或板条状的结构且存在于Al晶粒的枝晶结构中(见图2)。相反,在SLM制造的高的冷却速率的条件下(10exp(3)–10exp(8) K/s) ,这些合金形成超细的共晶Si结构,见图4c和d,在胞周围和晶粒边界(图4g和h)的尺寸大约为10–100 nm 。这一极端细小的胞纤维组织,以及超细的共晶组织,导致了SLM制造的铝合金样品的机械性能的显著提高。

▲图4 亚共晶AlSiMg合金的显微组织特征,EBSD结果显示了(a)出生的Al柱状晶的晶粒
<001> 显微织构在制造方向(ZY)的结果,(b) 在XY方向上的出生Al晶粒的结构; (c) ZY 和(d)
XY方向上的SEM照片, 表明细小的共晶结构。噶被放大的照片,显示了 (e) 带对比度图像和 (f) 一个方位图 ,
显示了在出生Al晶粒中的胞结构的相似的方位;TEM image in (g) 和 (h) 的TEM照片显示的细小的共晶Si在胞内的情形。
优化工艺参数在SLM制造过程中的应用来构建具有细小显微组织和理想机械性能的部件。在SLM制造过程中共晶Si的显微组织的控制受到许多因数的影响,包括热动力学(即润湿性)和局部的Al和Si的原子浓度。在SLM的制造过程中,由于热源是移动的,热温度梯度和生长速率的变化是随着熔池而变化的,导致了构建的显微组织和织构的不同。许多研究人员探索了这一点,尝试通过控制工艺参数来改变熔池而实现合金显微组织的改变。例如,Thijs等人则提出了熔合的在溶质的再分配效应同传统制造工艺显著不同。他们观察到Si的固溶度在固溶的Al中由于快速冷却而显著的增加。因此,超固溶的Al固溶体,得到细小的胞-枝晶结构,沿着位于胞边界的纤维状的共晶Si而形成。Si在液相Al中的固溶浓度受到冷却速率和扩散的影响,这可以通过几个主要的工艺参数来进行控制,包括激光功率和扫描速度等。进一步的,由于激光同材料的相互作用时间比较短,液相的波动或毛细波的形成,将会在熔池中产生不均匀的显微组织。相应地,不同的研究人员研究了通过不同扫描策略来改变显微组织和提高SLM制造制品的质量。
3.1.2. 过共晶Al-Si合金
过共晶Al-Si合金的显微组织主要包括初生的Si颗粒和共晶的针状Si嵌入在初生的Al基材中,初生的Si颗粒可以产生高的强度和耐磨性能。在传统铸造的时候,会形成多面和块状的初生Si,见图2c所示。,从而导致韧性低、耐磨性差和机加工性能差,这极大的限制了该合金的应用。这些限制可以通过细化初生Si颗粒和在Al基材中的分布来实现。在AM制造中,初生Si颗粒的尺寸通常<1 μm,同传统铸造的合金相比,他们通常为 25–50 μm,此时的合金含Si量为20wt%。Kang等人的研究表明在高Si合金Al-50Si 合金中,熔池内部(接近激光热源的地方)会随着Si的浓度的降低而逐渐凝固,此时外部的熔池由于较高的冷却速度而产生具有更小尺寸的出生Si相,见图5所示。这是因为被流动的液体(Marangoni 对流)所控制的液相金属孕育的初生Si相在熔池外部凝固,这是在SLM的过程中的温度较低的时候形成的。这一构建过程中的微观分离会对熔池的温度和尺寸造成显著的影响。这一数值是输入能量的函数。进一步的,扫描速度和其他加工参数也会显著的影响过共晶的显微组织,在SLM过程中的较高的冷却速率会造成相的位移,并且过共晶会形成同亚共晶或共晶相似的显微组织。

▲图5 SLM制造过共晶 Al-50Si铝合金时的显微组织和示意图,熔池、初生的Si和共晶的Si均分布在其内
SLM制造的时候,在亚共晶和过共晶-共晶之间的Al-Si合金的显微组织是不同的。这主要是因为在初生相的凝固过程中相的比例不同造成的。初生的Al主要在亚共晶中占据主导,由于在强烈的热温度梯度和快速传热的条件下及其少量的共晶弥散在晶粒间以细小的形式的定向生长而形成外延和柱状晶结构。在另外一方面,相当数量的共晶存在于过共晶合金中,此时的Si形核作为初生相以分散的颗粒存在于共晶液相中。而这可以避免柱状晶在过共晶中的形成,强烈的热温度梯度和相应的流体流动将会导致Si颗粒的不均匀的分布和漂浮的分离。由于热温度梯度和冷却速率均会影响凝固状况和液体的流动,激光加工参数将会同时影响过共晶和亚共晶的显微组织,尽管他们在显微组织和形成上存在差别。
3.2. 缺陷
研究也表明加工参数对AM制造Al-Si合金部件的密度产生至关重要的影响,这是因为会形成气孔。气孔的形成会严重的影响到部件最终的机械性能和断裂强度。众所周知,加工参数可以优化来增加SLM制造的部件的密度。例如,应用高的功率和扫描速度的组合,并且扫描间距缩小,可以通过优化后来提高SLM制造部件的密度。然而,很少有研究研究揭示出其对熔池的材料化学的影响造成的对最终部件中缺陷的形成的影响的相关研究。
图6显示的为在AM制造AlSiMg合金的时候所得到的不同的缺陷。球化现象(图6a)是在SLM制造金属的时候经常观察到的一种现象,它会造成不规则的扫描道和弱的道道之间的结合。进一步的,这一球化现象在沉积新鲜的粉末到前一已经熔化的道次上的时候会造成阻碍,由此造成不均匀、气孔和甚至是分层。因此,球化会严重的恶化材料的性能和部件的几何形状。不规则的气孔缺陷是一系列不完全熔化和捕获的气体所形成的。不规则的气孔缺陷是不充分的能量密度和层层之间的弱的结合所造成的,此时排列的缺陷经常伴随着相邻的熔化道之间的距离过大所导致的扫描道之间搭接不充分造成的。

▲图6 在SLM制造Al-Si的时候形成的典型的缺陷的不同类型:(a) , (b) 气体造成的气孔 , (c) 由于未熔化完全造成的空穴或气孔;(d) 热裂纹
粉末原材料中的湿气会造成比较小的气体所形成的气孔,一般直径小于5 μm,见图6b。这在高能量的激光进行作用的时候是一个非常严重的问题。进一步的,如果湿气同Al反应,生成Al2O3的话,释放出来的氢气就会被溶体所吸收。这样反过来就会造成富集氢的气孔,使得气孔的尺寸在制造过程中由于温度升高而变大。例如,Weingarten 等人报道了在SLM制造A1Si10Mg 合金的时候,其形成的气孔96%的为氢气孔,见图7。然而,将粉末进行预热会抑制气孔的扩大。例如,Yang等人的研究显示,在气氛室内200 °C的条件下保温16小时会显著的提高制造产品的质量。
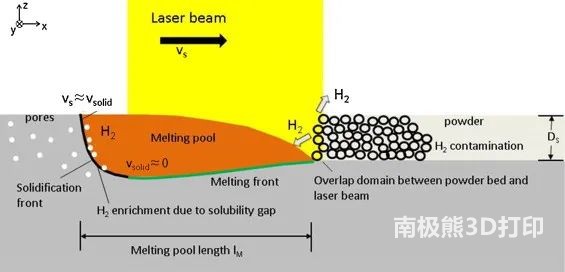
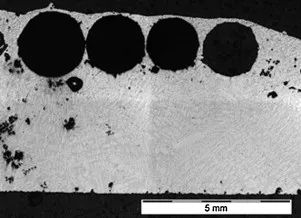
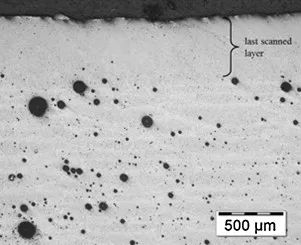
▲图7 Weingarten等人的研究结果:(a) 铝合金粉末和激光相互作用的示意图;(b)SLM制造的AlSi10Mg合金样品的横截面图;(c)SLM制造的AlSi10Mg合金在经过550 °C@1h热处理之后得到的横截面结果
大尺寸的气孔(直径为>30 μm)同熔化时的匙孔效应相关,造成的原因是极端高的体积能量密度以及在采用相似的能量进行轮廓扫描和中心扫描的时候。第一个位置位于轮廓扫描的区域,此处的熔池的一边的热扩散比较困难,造成大量的热积累。第二个位置位于圆周的中心,此处的加速和减速存在改变激光方向,造成局部的能量增加。在这两个位置形成的气孔会导致疲劳性能下降,但可通过调节能量输入来改变。第三种典型的位置为岛状扫描的边界时存在,此处存在额外多的边界搭接。优化SLM制造的Al-Si合金的参数会显著的控制这些未熔合气孔的存在,见图6c。实现了制造致密的部件,即使是在没有预热粉末原材料的前提下也能实现。通常来说,近共晶Al-SI合金对凝固裂纹或热裂纹不敏感,除了Si的含量为1 wt%的时候,见图6d。这些SLM样品中的裂纹的萌生是通过气孔的收缩和由于在制造的过程中应力的释放造成的扩展而形成。
未完待续,欢迎您持续关注
(责任编辑:admin)
最新内容
热点内容