金属粉末床熔合增材制造中的激光熔化模式(4)
时间:2023-02-07 09:38 来源:长三角G60激光联盟 作者:admin 阅读:次
四、知识和机会的差距
A、 新兴知识
这里总结了基于过程的定义的几个关键点。首先,在所有三种模式下都有可能形成蒸汽凹陷,并且在传导模式之外,蒸汽凹陷动力学比熔池动力学更为瞬态。其次,在静止激光熔化下,对应于蒸汽凹陷和熔池转变的两个时间节点严格定义了三种熔化模式。第三,固定激光熔化中的熔化模式可以扩展到扫描情况,根据该情况,商业AM机器通常以过渡或稳定锁孔模式操作。然而,与使用施加的能量密度作为度量的情况一样,由于P-V空间中的蒸汽凹陷形态和激光吸收存在较大变化,因此应谨慎。
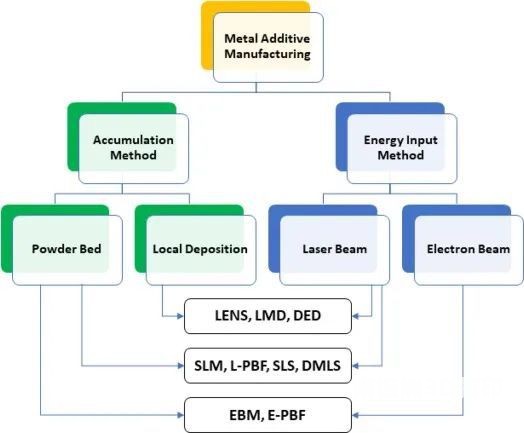
根据积累和能量输入方法对金属增材制造的不同过程进行分类的流程图。
增材制造技术通常根据所用材料的状态、材料层结合的机制以及熔化或软化材料的能量来源进行分类。根据累积方法和能量输入分类的金属增材制造工艺如上图所示。根据此流程图,金属增材制造中使用的两种主要技术类别是功率床融合(PBF)和定向能量沉积(DED)。PBF中使用的主要电源是激光器和电子束,相应的方法通常分别称为选择性激光熔化(SLM)和电子束熔化(EBM)。这两种方法都经常用于金属AM。
B、 超越x射线成像
Operando高速同步加速器x射线成像是探测激光聚变过程的宝贵工具。除了直接测量之外,熔池和蒸汽凹陷形态演变可以通过(如图6所示)高速x射线成像和其他原位和实时监测技术的组合转化为其他信号形式,如动态激光吸收、蒸汽羽流动力学和模式定义的超声信号。例如积分球辐射测量、纹影成像和浸没超声。在过程中x射线成像不可行的情况下,这些可能是过程监控的可行和有效方法。为了便于翻译(也在原位和异地数据之间),基于物理的建模、大数据方法和适当的实验设计是关键。
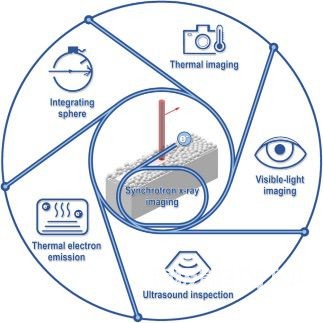
图6 operando同步x射线成像和其他高速现场监测技术的集成。通过多技术融合和多信号转换,同步x射线的新知识可以转化为工业实践。
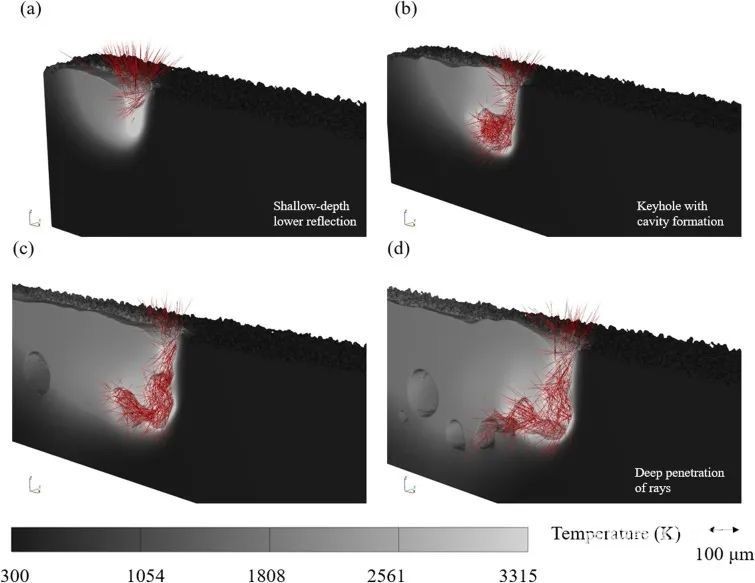
温度等值线以及离开金属相自由表面的反射激光轨迹。
一旦形成匙孔,与激光接触的金属相的暴露表面积将急剧增加。因此,更多的能量将被金属相吸收,从而在很大程度上促进传热。正如Martin等人所报道的那样,凹陷前部的反射将导致其后部的汽化。在稳定条件下,暴露的表面比锁孔条件下的表面小得多。由于光线夹带,具有复杂形状(如形成空腔或钥匙孔向后倾斜)的金属相的较大暴露表面积有可能吸收更多的反射。根据上图,在浅深度条件下,大部分光线会离开金属的自由表面,反射很少,因为凹陷区很浅,反射光线的路上没有障碍物。
C 稳定锁孔AM
这些基于过程的定义为AMcommunity提供了新的指导方针。一个直接的结论是,在金属的激光粉末床熔合AM中,稳定的锁孔区域是实现全密度构建的理想区域。过渡区比稳定锁孔区小得多。它们共同勾勒出金属材料的工艺窗口,如图7(a)所示。在窗口外,P-V空间被几个可能造成微观结构缺陷或尺寸不精确的区域所占据,其中包括小孔孔隙度、球化和未融合孔隙度。为了充分利用这一窗口,我们需要确认并了解其边界。在实践中,当工艺工程师努力提高构建速率或构建条件的局部变化(如激光光斑大小、扫描速度、空气流量和粉末床表面)造成与规定的P-V参数的瞬时偏差时,通常会接近这些边界。换句话说,有必要揭示这些缺陷的根本根源。例如,在图7(b)和图7(c) 中,通过高速同步x射线成像发现锁眼孔隙度边界光滑且清晰。只有当靠近锁孔尖端的气孔从临界锁孔不稳定性释放的声波(高振幅、短持续时间、定向深度)中获得足够的动能时(类似于艺术品中的双掌打击),它们才能迅速从锁孔周围的大热梯度场中逃逸,并被凝固前沿捕获为缺陷。这种声波驱动的机制与粘滞阻力驱动的机制不同,后者需要由缩回锁孔产生足够的等待时间。
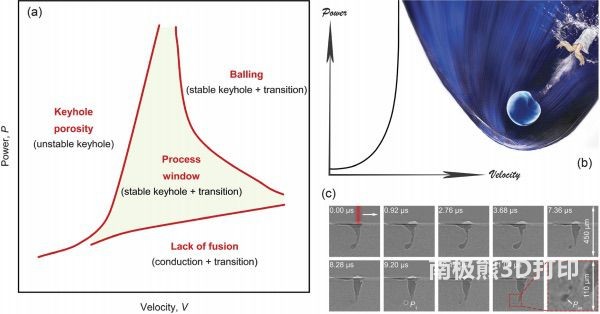
图7金属激光粉末床熔合工艺图示意图。
D、 过程计量学
在金属的激光熔合AM中,迫切需要改进工艺计量。其中与精确确定熔化模式最相关的是激光功率、光束轮廓和扫描速度。它们共同决定了在构建过程中任何位置提供的能量。对于激光功率,通常不确定度在3%-5%范围内的传统热功率计是现成的。然而,这些不确定性在文献中并不经常报道,并且激光功率被假定为用户要求的功率。先前提供的基于物理的定义指出了激光辐照度在确定熔化模式中的重要性。为了准确确定可转移过程窗口,我们建议直接测量激光功率,并对每项将功率视为变量的研究说明不确定性。
如模拟所示,光束轮廓对于确定熔池结果也很重要。在文献中,“斑点大小”这一通用术语通常被简单地表述。只有当光束的几何轮廓已知(具有一定的不确定性)且其定义明确时,才可以使用这样的单个参数。目前有几种商业系统可用于测量光束轮廓,但没有建立绝对可追溯性的方法,如激光功率,这提供了一个计量机会,从而可以量化和解决商业光束轮廓仪之间的差异。
最后,扫描速度在确定激光扫描期间的停留时间以及由此传递的能量方面起着同样重要的作用。尽管如此,人们很少关注其测量或准确性。
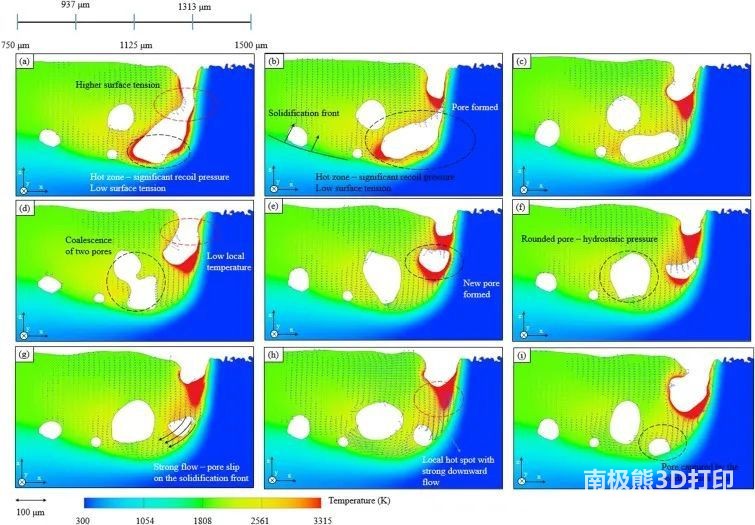
孔隙形成过程中的温度等值线和速度场。
由于逐层制造策略、局部加热和快速冷却以及消耗粉末材料,增材制造金属中经常发现 LOF 区域、气体孔隙率、未熔化颗粒和光滑刻面。这些缺陷通常是在疲劳断裂表面上检测到的疲劳失效的来源。缺陷通常是由于金属增材制造过程中能量不足(LOF缺陷)或能量过多(孔隙率)而产生的。在金属AM中也观察到α相缺陷和显微镜下光滑的刻面,据报道是裂纹萌生的来源。缺陷的类型、位置、形状、尺寸、方向和密度等特征受工艺参数的影响很大。
五、结论
在这篇综述中,我们描述了激光熔化的一般物理过程。正是由极端热条件引起的许多物理机制的复杂相互作用,决定了蒸汽凹陷和熔池形态,并定义了熔化模式。熔化模式随着温度的升高而变化,从传导转变为小孔。
根据形态测量方法,熔化模式的定义可以是死后的或基于过程的。基于尸检的定义在概念上是合理的,但由于省略了蒸汽抑制的细节,它们是主观的、模糊的和令人困惑的。相比之下,基于过程的定义更清晰、更完整,其中熔体池和蒸汽凹陷的形态都是直接从操作高速x射线图像中测量的。它们解决了传统定义的传导模式中产生的锁孔孔的谜团。
熔化模式定义的修订提出了新的指导方针和方向。首先,在金属的激光聚变AM中,激光与物质的相互作用主要是与蒸汽腔。除传导模式外,蒸汽压差比传统预期的更为动态和瞬态。其次,稳定的小孔激光熔化为可持续和稳健的增材制造提供了一种方法。P-V空间中一些常见缺陷产生区的边界和起源仍然缺乏。此外,多物理模拟、从形态数据到其他可行和互补测量信号的信号转换以及改进的过程计量正被用于开发跨平台和规模的可转换过程窗口。
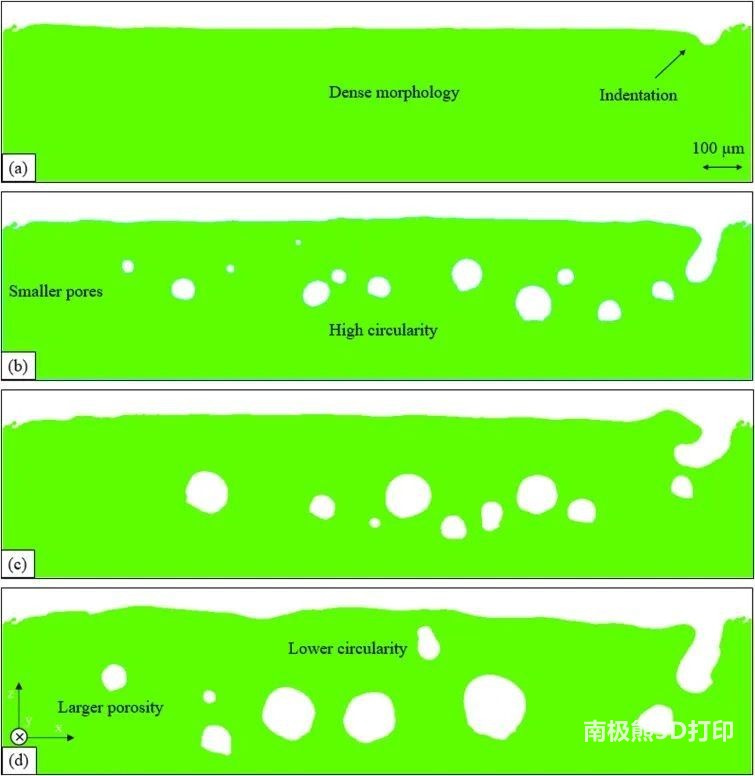
纵向视图显示了自由表面以及以下情况的孔隙率分布。
在匙孔概念首次提出几十年后,正是操作高速x射线成像技术为激光熔化的物理过程打开了大门。随着技术的进步,有可能以更高的空间、时间和能量分辨率重新审视长期存在的问题,并继续更新或修正现有的理论和模型。我们希望这篇综述不仅能加深对激光熔化模式的理解,而且能启发人们对金属激光熔合增材制造的前沿研究和发展的思考。
来源:Laser melting modes in metal powder bed fusion additive manufacturing, Reviews of Modern Physics, 10.1103/RevModPhys.94.045002
参考文献:Aboulkhair, N. T., N. M. Everitt, I. Ashcroft, and C. Tuck, 2014,“Reducing porosity in AlSi10Mg parts processed by selective laser melting,” Addit. Manuf. 1–4, 77–86.;
Aboulkhair,N. T., I. Maskery, C. Tuck, I. Ashcroft, and N. M. Everitt, 2016, “On the formation of AlSi10Mg single tracks and layers in selective laser melting: Microstructure and nano- mechanical properties,” J. Mater. Process. Technol. 230, 88–98.
(责任编辑:admin)
最新内容
热点内容