最小52μm!μ-LPBF金属3D打印NiTi合金微器件获突破,兼具优异力学与形状记忆性能
时间:2022-06-24 15:22 来源:熊志伟 作者:熊志伟 阅读:次
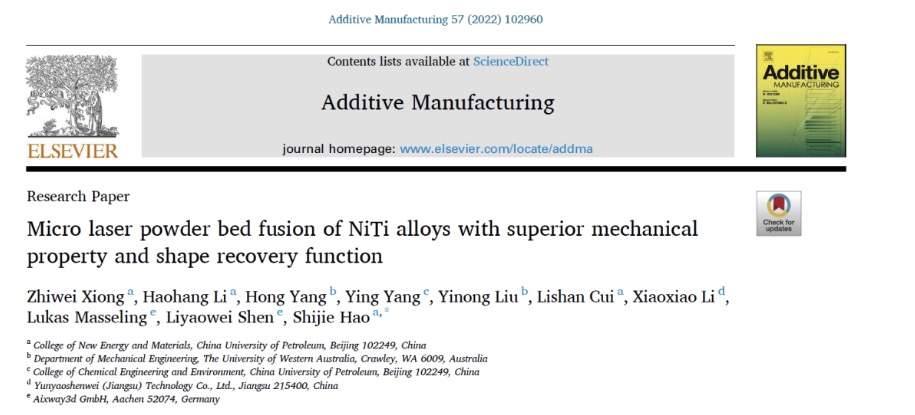
论文链接:https://www.sciencedirect.com/sc ... 22003530?via%3Dihub
研究背景
NiTi形状记忆合金因具有独特的形状记忆效应、超弹性、高阻尼性及生物相容性而在功能微器件(最小特征壁厚/杆径<100 μm)领域展现了极大的应用前景,如微驱动器、微机械传感器、微医疗器件和植入物、微电子系统器件等。然而,制备此类具有复杂结构或三维结构的NiTi功能微器件需要特殊的制造方式,常规的机加工难以适用此类NiTi合金构件。
激光粉床熔覆(Laser powder bed fusion, LPBF)作为一种粉末床增材制造技术,可以通过逐层制造的方式实现复杂结构的三维制造。相比于其他金属增材制造方式比如直接能量沉积、电子束选区熔化等,LPBF拥有更高的表面光洁度和更小的制造尺寸。然而,受限于单道熔池的宽度,常规的LPBF所能制造的最小特征尺寸依然≥300 μm。这一数值远大于微器件所要求的特征尺寸。近年来,μ-LPBF正逐步发展,其是通过缩减一个或多个加工参数比如光斑直径、粉末粒径以及铺粉层厚来实现。尽管有学者以μ-LPBF的名义研究过NiTi合金或者对比过常规LPBF与μ-LPBF在制备316 L不锈钢材料的不同,但是他们的研究对象依然是块体材料,并没有制备出满足要求的微器件。也有学者制备出了特征尺寸在100 μm以下的复杂结构,涉及到钼弹簧、不锈钢螺旋结构等,但这些研究的制造品质不尽如意,表现了较差的表面光洁度和低的致密度。更重要的是,这些微构件并没有展现一定的力学或功能特性,难以满足实际应用需求。
此外,在实际生产中,为了获得更小的制造尺寸,μ-LPBF不仅采用小尺寸加工参数,而且通常采用单轨道激光扫描的方式,这不同于常规LPBF的多轨道重叠扫描,其将会带来显著不同的热历史,无论是在加热熔化或是冷却凝固过程。热历史的不同必然会带来微观组织、成分分布、相变等方面的不同,而目前尚缺乏以此为视角的研究,也缺乏高质量微器件的成功制备。
创新点
本研究从扫描模式和热历史角度,以NiTi微器件为研究对象,综合探究了μ-LPBF制备NiTi合金的热历史特征、制造性能、材料微观组织与相变行为,揭示了采用μ-LPBF制备100 μm以下NiTi合金构件的内部微观特征与宏观力学/记忆性能,并制备了一系列兼具优异力学与形状回复性能的NiTi功能微器件。
图文简述
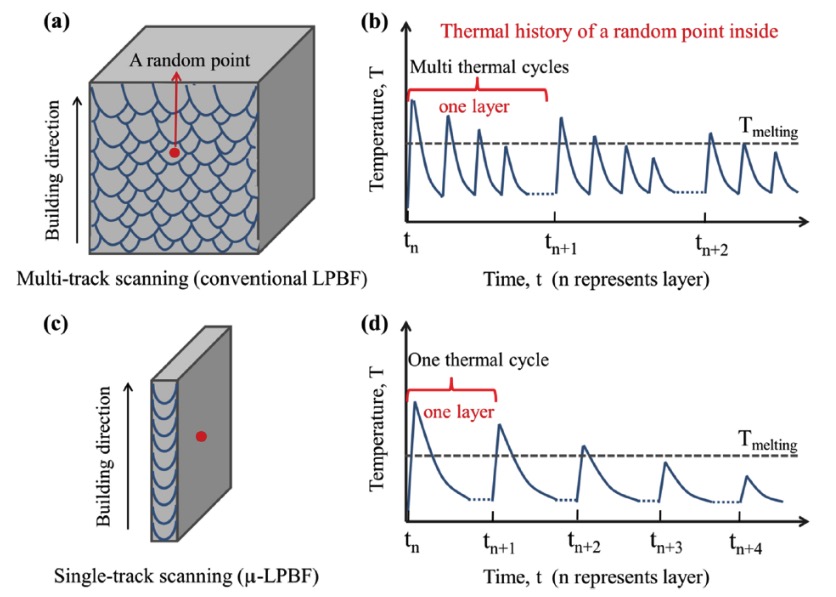
△图1. 常规LPBF与μ-LPBF在扫描模式和内部某点热历史的区别。
常规LPBF制备样品采用多轨道重叠扫描,内部任意一点会经历多次重复加热熔化-冷却凝固,以及复杂的各个方向再加热过程;而μ-LPBF制备过程中因激光单道扫描,重熔仅发生在层间建造方向,层内仅一次熔化凝固过程,其内部任意一点经历的重熔再加热很弱。而且极小的薄壁特征下,周围粉末作为散热介质的影响也被增大。这些热历史的区别对于成分分布、晶粒尺寸、析出情况、组织形貌等均有可能产生影响。
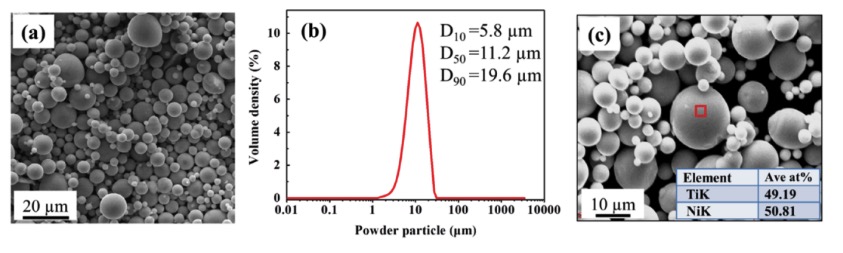
△图2. μ-LPBF采用的小粒径NiTi粉末表征。
本研究采用了粒径为5.8-19.6 μm的NiTi粉末,光斑直径为22 μm,铺粉层厚为10 μm。以功率和速率为变量设计一组正交实验摸索最佳参数窗口,并探究μ-LPBF下工艺参数对薄壁件成形壁厚、粗糙度、致密度、相变、力学等多方面的影响。
△图3. 本文所采用的激光单道扫描方式示意图及制备的多种NiTi合金微器件。
△图5. 不同激光功率和扫描速率组合下的制造性能,包括成形壁厚、相对致密度、表面粗糙度。
(责任编辑:admin)
最新内容
热点内容