你觉得电弧增材不就是焊接吗?
时间:2022-06-23 13:55 来源:格智学院 作者:admin 阅读:次
电弧增材是焊接吗?
要回答这个问题,我们就要先了解焊接的定义,然后再依据定义来判断电弧增材是否符合。
-
焊接的定义:通过加热或加压,或两者并用,并且用或不用填充材料,使同种或异种工件达到原子间结合的一种加工方法。
根据焊接的定义,电弧增材完全可以理解为采用电弧作为热源,对材料进行加热,用金属丝材作为填充材料,使同种或异种材料达到原子间结合从而形成工件的一种加工方法。
显而易见,电弧增材无疑就是一种焊接技术。然而,我们不妨顺着这个思路再进一步。从定义的角度来说,金属增材制造的各种技术路线,无论是成熟度更高的激光粉末床熔融增材技术,还是后起之秀的激光能量沉积,电弧增材,等离子熔丝增材,电子束熔丝增材等,似乎也都符合焊接的定义。而事实上,如果我们将常见的焊接方法和增材工艺技术路线进行对比,我们就不难发现,二者之间惊人的相似。
焊接方法总体上可以分为三大类:熔焊、钎焊、压力焊。其中熔焊包括:电弧焊、激光焊、电子束焊、等离子弧焊等,压力焊包括:电阻焊、搅拌摩擦焊、冷喷焊接、超声波焊接等。
而我们常见的金属增材技术则包括:电弧增材、激光粉末床熔融,激光定向能量沉积,电子束熔丝增材,等离子增材,也包括近来逐渐受到关注的搅拌摩擦增材、冷喷增材等等。
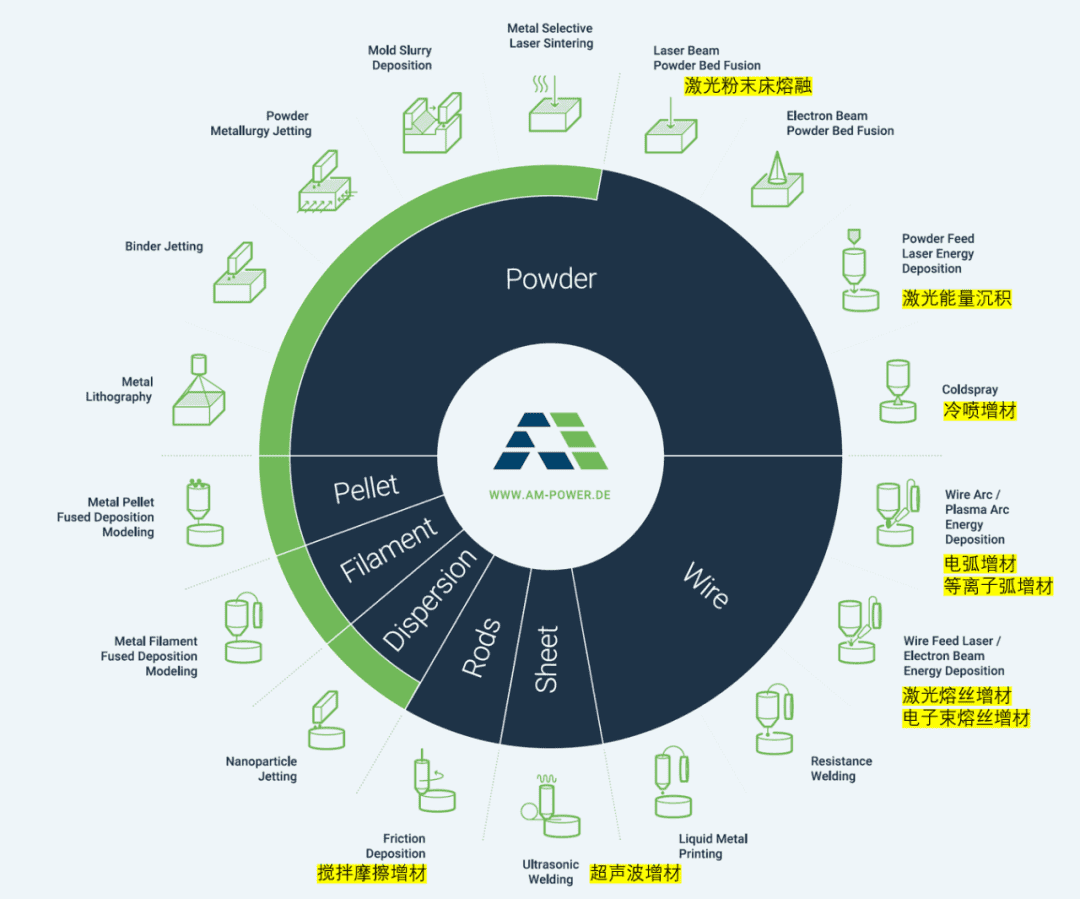
图片来源:AMPower
到这里,结论已经呼之欲出。不仅仅电弧增材是焊接技术,绝大多数金属增材技术都与焊接技术同根同源。
这个结论让人觉得意料之外却又在情理之中,因为焊接技术与增材技术从来都不是两个互相排斥或是互相包含的概念,它们是从两个完全不同的角度对技术进行定义和分类的。因此,一项技术方法既是焊接又是增材也是完全可能的。然而这个结论似乎并不能解答大家真正的疑问,因为比起电弧增材是不是焊接,其实大家更想问的是:作为一种焊接技术,我们为什么要把电弧增材定义为一种增材技术,而不是就叫它电弧焊呢?
这个问题背后,可能反映的是大家的一个认知误区。因为往往我们提到金属增材制造或者金属3D打印,大家首先会想到的是激光粉末床熔融(SLM)技术,甚至有人会觉得SLM是增材制造,而电弧增材不是。当然这也情有可原,因为SLM技术确实是目前被认为技术成熟度和工业化程度最高的金属增材技术。然而受限于效率、成本和质量,SLM技术更适用于小型精细的金属零件增材,而电弧增材自由的成型环境对零件尺寸几乎无限制,成型效率可达每小时几公斤,更适合中大型到超大型复杂金属构件的制造,随着近年来技术成熟度和工业化程度逐步达到了工业化应用的水平,逐渐被越来越多的人关注。
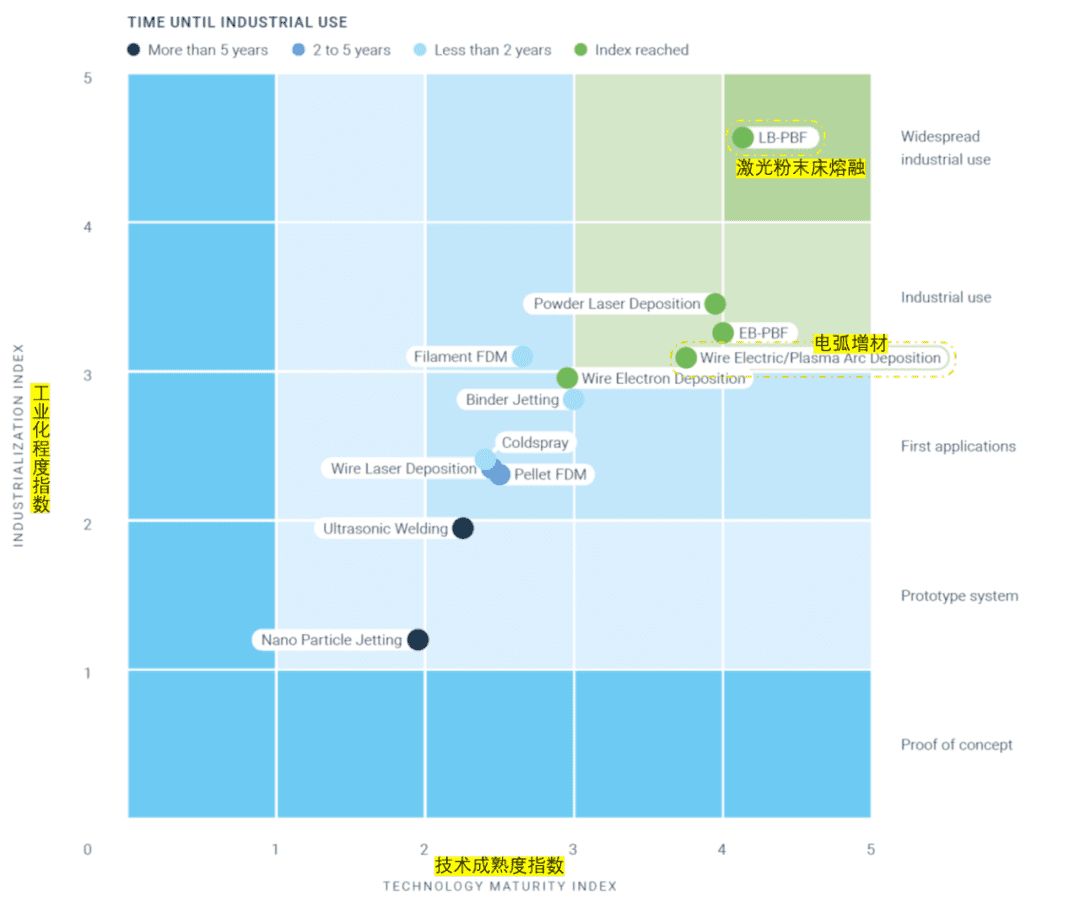
图片来源:AMPower
增材制造定义:以三维模型数据为基础,通过材料堆积的方式制造零件或实物的工艺。
从增材制造的定义,我们可以看到三个关键的要素:
第一,是原型制造,描述了增材制造的用途,是用于零件或实物的原型制造、快速成型;
第二,是模型驱动,定义了增材制造一定是一种数字化技术;
第三,是逐层堆积,说明了增材制造自下而上、从无到有的过程。
这三个要素,恰恰体现了电弧增材与焊接之间的不同。
电弧增材制造技术(Wire Arc Additive Manufacture,WAAM)是一种采用电弧或等离子弧作为热源将金属丝材熔化,在程序或软件控制下采用逐层熔覆原理,根据三维数字模型由线-面-体制造出接近产品形状和尺寸要求的三维金属坯件的先进数字化制造技术。
差异一:原型制造
电弧增材是从无到有直接进行原型制造、快速成型的过程。而一般来讲,焊接的应用场景包括工件的连接和表面改性,都是在已有的零件上进行加工的手段。因此从应用场景上来说,电弧增材与焊接就是不同的。而不同的应用场景,就意味着不同的目标和要求。我们以和增材更为接近的堆焊为例。
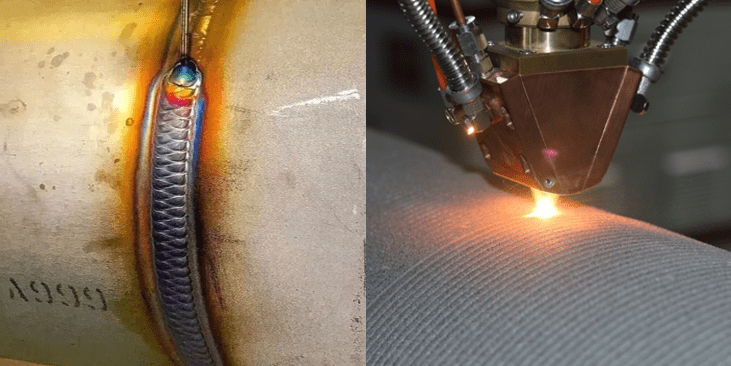
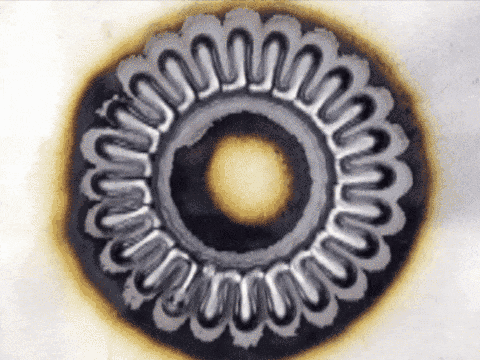
电弧增材制造技术成型的零件由全焊缝金属构成,化学成分均匀、致密度高,在逐层堆积过程中,零件会经过多次加热,经历多次淬火和正火,可以消除大型铸件中存在的不易淬透、宏观偏析、强度和韧性的各向异性等问题。另一方面,电弧增材制造无需模具,工序少工艺链短,整体制造周期短,自由的成型环境对零件尺寸几乎无限制,成型效率可达每小时几公斤,适合中大型到超大型复杂金属构件的制造。
差异二:模型驱动
由于电弧增材是用于零件的快速成型的,因此不管是通过CAD软件自主设计亦或是通过视觉逆向重构生成,电弧增材制造的工作流程起点都一定是零件的三维数模。而对于焊接来说,则并没有这一项要求。具体来说,焊接过程要完成的是“点”或“线”的连接或是“面”的覆盖,而电弧增材要完成的是“体”的堆积,而这个“体”就是零件的三维数模。
模型驱动的差异,衍生出的是工艺编程方式的截然不同。即便是机器人焊接或堆焊,由于路径复杂程度低,大多数时候编程都可以通过手工示教或配合简单的轨迹偏移即可完成。然而电弧增材,需要首先将目标工件的三维模型通过软件在垂直于水平方向上或者是在曲面上进行2D分解,每个分解层对应着实际的沉积层,由执行机构带动金属熔池沿着通过软件规划好的由数万个甚至更多“空间点”组成的复杂空间轨迹,逐层沉积最终形成实体零件。如此复杂的空间轨迹,自然无法通过传统焊接的编程方式实现,而必须依靠专业的CAM软件。这也是为什么,软件是电弧增材一项至关重要的技术分支。更多关于软件的重要性,大家可以查阅上一篇文章,里面有更详细的讲解,这里就不再展开。
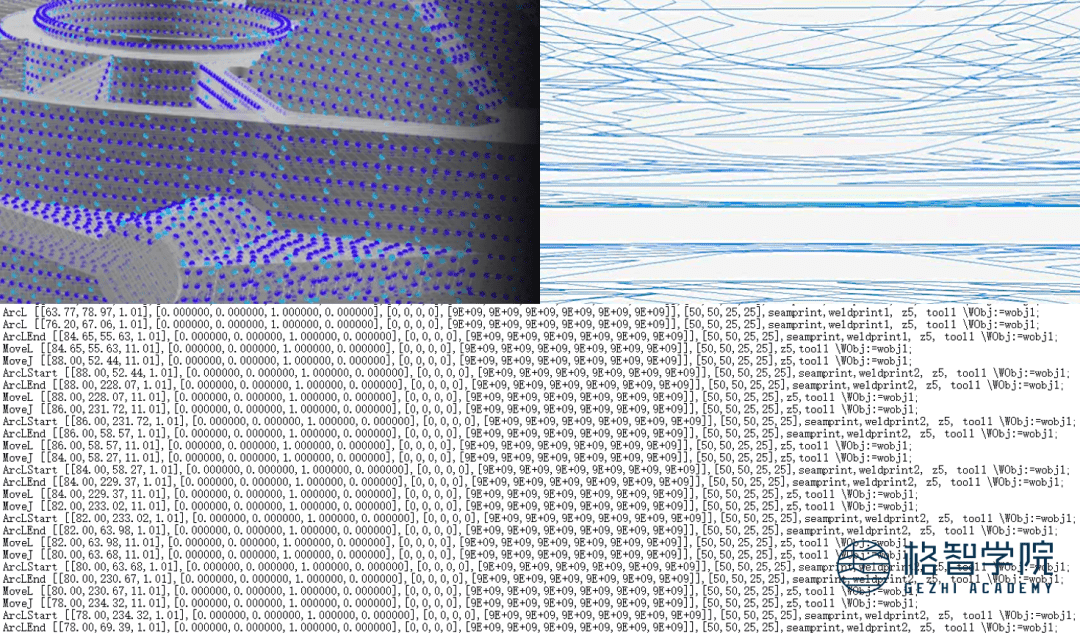
差异三:逐层堆积
上面我们说到了,电弧增材是要完成零件三维“体”的堆积,就需要沿着复杂的空间轨迹将材料逐层堆积。而逐层堆积的过程,带来的绝不仅仅是轨迹编程上的差异。
电弧增材完成零件通常需要增材数百甚至数千层,这就对工艺质量的稳定性,过程缺陷的即时识别与修复的要求都提升了数个量级,因为一旦增材过程中出现缺陷,又未能及时识别和修复,就会导致整个产品的报废,造成无法估量的损失。因此为保障增材质量,除了对装备的稳定性要求更高之外,增材过程中通常需要采用各种过程监控手段,如工艺参数监控、形貌监控、熔池监控等等,再通过智能化软件辅助对过程缺陷进行识别和修复。
与此同时,不同的质量要求,意味着焊接领域相对成熟的各项标准、规范、体系,仅供参考,不能拿来主义的应用于电弧增材。事实上电弧增材制造目前可供参考的质量标准寥寥,比如《GB/T 39253-2020增材制造 金属材料定向能量沉积工艺规范》以及《GB/T 39254-2020增材制造 金属制件机械性能评价通则》,然而落到各行各业的生产实践中,适合于电弧增材的工艺规范或是检测标准几乎空白,从而使得工艺认证变得困难重重。因此标准体系的建立和完善可以说是整个电弧增材行业目前最关注的,甚至可以说是影响着电弧增材技术得到更广泛应用的核心痛点。然而标准化之路漫漫,仍然需要更大的投入和更广泛的参与,更需要经过实践漫长的检验,只能说,吾将上下而求索吧。
传统的新生
相信到这里,电弧增材与焊接之间的关系大家应该已经了然。它绝不是简单的新瓶装旧酒,而是一项传承了三千年的传统技术,复合了更多学科和技术领域,蜕变后的新生。但如果我们的眼光再长远些,焊接技术也在不断向着智能化、数字化的方向发展,而电弧增材技术也会不断成熟和完善,在不远的将来,彼此之间的界限会不会越来越模糊,融合甚至孵化出新的可能呢?
让我们拭目以待。
推动行业发展需要低使用门槛的软件和专业技术人才
任何新兴制造技术的发展,都需要装备、软件、材料、工艺、人才五大核心要素协同发展,缺一不可。
对电弧增材技术来说,其工艺本身与有着悠久历史的焊接工艺同根同源,因此巨大的机器人焊接应用市场存量对应的装备、工艺、材料经验储备都应该可以成为电弧增材技术发展的土壤。然而现实情况是,时至今日,电弧增材技术的应用依然局限在少数场景,归其原因木桶的短板在于早期软件和人才两个要素的缺失,制约了行业的发展。
相信随着专用CAM软件的出现和发展,对专业技术人才的要求门槛也随之不断被降低,用户可以越来越专注于工艺和产品的开发,从而不断将电弧增材技术的潜力充分发掘出来。
(责任编辑:admin)
最新内容
热点内容