高强度铝合金增材制造面临的挑战和混合增材制造的发展现状(1)
时间:2022-01-25 20:11 来源:江苏激光联盟 作者:admin 阅读:次
增材制造(AM)工艺,也被称为3D打印,使几何复杂的零件可以在扫描物体或使用设计软件生成的三维(3D)数据的基础上,一层一层地生产出来。与传统的制造工艺相比,AM省去了生产步骤,允许从3D模型设计中快速且相对容易地建立物理对象的原型,并复制现有的对象。在过去的二十年里,AM工艺已经广泛应用于许多工业部门的复杂形状部件的制造,其主要应用领域之一是在航空航天工业。该部门广泛使用高强度铝合金,因为其高强度重量比和刚度重量比以及优良的可加工性。
然而,AM工艺对高强度铝合金的适用性仍然受到增材制造(AMed)铝部件中存在的几种不可忽视的问题和缺陷的限制。多年来,大量的研究致力于最小化或消除这些缺陷,从而扩大AM在高强度铝合金中的应用范围。本文综述了航空航天用高强度铝合金的AM研究现状。重点是AMed 2xxx和7xxx系列合金的缺陷和问题,以及新型混合AM工艺的最新发展,以最小化或消除缺陷。
1. 介绍
高强度铝合金因其优异的强度重量比和刚度重量比以及良好的可加工性而被广泛应用于航空航天行业的结构件制造中。由于航空航天零件的几何复杂性,传统的减法制造方法在制造过程中面临着巨大的挑战。然而,由于要制造的组件体积小、价值高和几何复杂性高,AM过程适合于这一领域的应用。此外,AM流程可以实现部件整合,即通过设计和制造具有更复杂拓扑结构的部件,减少飞机部件的总数。零部件整合的好处包括降低生产成本和零部件失效风险,更好的产品性能,包括高强度重量比和轻量化,以及随着零部件复杂性的增加而降低材料使用量。由于这些原因,航空航天工业已经在上大规模采用了AMed组件。
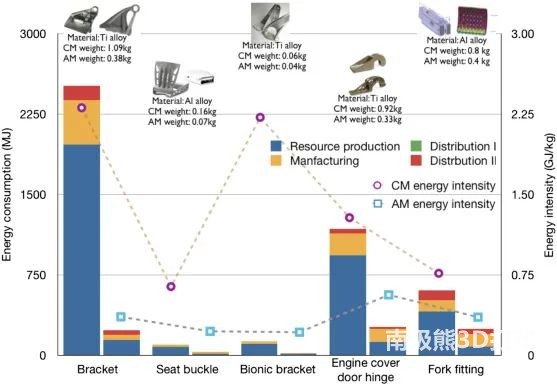
从支架到闸门的一次能源结果的案例研究组件。
使用LCI模型,对每个案例研究中被替换的AM组件和现有CM组件进行了从支架到闸门的一次能源和排放分析。该分析的结果在上图中进行了部分总结,显示了每个案例研究组件的CM和AM路径之间的平均支架到闸门一次能源利用的差异(左轴),以及CM和AM过程能量强度的差异(右轴)。
航空航天部件数量和飞机总重量的减少带来了两大环境效益。这些措施包括:(i)减少了制造过程中的材料浪费和能源消耗(从支架到闸门),(ii)提高了成品飞机的燃料效率,从而在运行中降低了环境足迹。使用AM工艺在装配过程中减少零件数量,也减少了库存中的工具数量和整体生产成本。举个例子,空客公司从126个液压外壳油箱部件,用传统工艺生产,变成了一个单一的AMed部件。通用航空公司报告称,一个由20个部件组成的喷嘴被整合到一个AM装置中,重量减少了25%。该公司还实现了从使用传统制造工艺生产的855个部件减少到12个合并AMed部件,从而减轻了飞机的重量,燃油效率提高了20%。
买飞比,即原材料重量与最终部件重量之比,是控制航空航天部件生产成本的主要参数之一。涡轮叶片和薄壁结构的这一比率可以在20:1和40:1之间,相当于相当大的原材料损耗。然而,由于设计中的几何自由度,使用AM工艺可以实现接近理想的买飞比(1:1),从而大大减少加工过程中的材料损耗。维护,包括定期更换机械部件,是所有飞机的一项要求。AM流程提供按需更换部件的快速生产,用于安装和装运,以满足短交货期限的要求。这种能力减少了一系列航空航天部件的维修提前期和相关成本。出于上述原因,AM工艺是航空航天工业中使用的一些最合适的制造方法。然而,AM在该领域的使用仍然受到某些类型缺陷的限制,这些缺陷影响高强度铝合金制成的AMed部件的质量。另一个关键问题是AMed组件缺乏全面建立的、全球公认的质量标准,这限制了AM工艺在航空航天行业的使用。
在过去的二十年里,我们进行了大量的研究,以(i)开发更有效的AM工艺,以降低成本和提高质量,以及(ii)减少AMed铝合金部件的缺陷,以提高结构完整性。这项研究的一个主要成果是新技术的发展,如混合增材制造(混合AM)工艺,以扩大AM工艺对高强度铝合金的适用性。混合制造过程,包括多种操作,例如连接和减法过程,已经发展为特定的应用和要求。Hybrid-AM是一种混合制造类型,其中AM过程与一个或多个其他过程(通常为其他AM操作和/或传统减法制造)相结合,以在AM单独或传统制造所能实现的基础上改进最终产品。
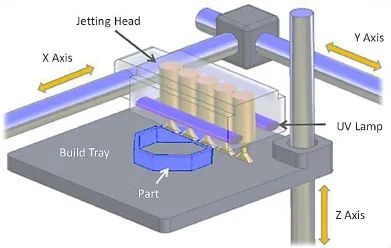
PolyJet的原理图(Gay 等2015)。
在材料喷射中,光固化树脂滴被选择性地沉积在构建平台上,并使用光源固化(ASTM, 2012)。树脂一滴一滴地沉积,形成最终模型的每个水平横截面层。在一层完成后,构建平台被降低,下一层将被放置在上一层。在材料喷射成形原型时,通常至少使用两种类型的树脂。一种或多种模型材料用于制作原型,而另一种支撑材料在打印过程中为结构提供必要的支撑。在后处理过程中,通过使用水射流或溶解在适当的溶剂中,可以很容易地去除这些支撑结构。聚喷墨打印技术是材料喷墨打印技术的一个例子。在上图中,多个喷射头允许同时打印一种以上类型的模型材料,并使用紫外线灯立即固化树脂。
在过去的十年里,工艺、机器和多种材料(同时使用两种或两种以上的材料)在混合调幅工艺中相互结合和融合,以提高零件质量、机械性能和性能以及主要调幅工艺的功能。然而,只有少数研究研究了混合调幅工艺的能力,并没有综述目前在高强度铝合金混合调幅技术的发展,这是本文的主要动机。因此,本文的主要重点是批判性地回顾了高强度铝合金调幅中出现的缺陷的研究,以及减少或消除这些缺陷的方法,特别是新的混合调幅工艺,然后通过解决混合调幅解决方案来提供消除这些缺陷的建议。
本文共分为六个部分。在第二节中,对铝合金的调幅工艺进行了回顾,并介绍了航空航天市场各子课题的相关研究和对铝合金调幅工艺的适用性研究。第3节涵盖了在高强度铝合金AM过程中遇到的主要限制和缺陷,重点介绍了2xxx和7xxx铝合金系列以及将缺陷最小化或消除的方法。第4节介绍了混合调幅工艺和铝合金混合调幅的最新发展,特别关注高强度合金。讨论对调幅和混合调幅过程进行了展望。最后,总结了本研究的主要结论和作者提出的建议。
2. 铝合金的增材制造工艺
根据国际标准化组织/美国测试和材料标准协会(ISO/ASTM 52900:2015),商业上可用的AM工艺可分为七种主要类型:材料挤压(ME)、粉末床融合(PBF)、定向能沉积(DED)、薄板分层(SL)、还原光聚合(VP)、材料喷射(MJ)和粘结剂喷射(BJ)。表1中总结了七种主要的AM过程类型的显著特征,其中考虑了材料、优点和缺点、建筑体积的典型范围(决定了AMed对象的最大尺寸)和近似分辨率(可以打印的最小尺寸)。
表1 主要AM进程的比较。

广泛应用于铝合金的AM工艺包括粉末床熔合、定向能沉积和薄板层合。在PBF工艺中,零件是在真空气氛中用滚轮将薄层粉末铝合金铺撒,然后用氩气(Ar)或氮气(N)等惰性保护气体回填。粉末熔化后形成固体层。在连续生产每一层后,计算机控制的制造平台沿着z轴逐渐降低,使后续的Al粉层(平台和滚轮示意图见图1(a))。PBF工艺可细分为PBF-激光(PBF- l),其中粉末层是使用应用激光烧结,和PBF-电子束(PBF- eb)工艺,其中粉末是由电磁线圈光栅化的电子束熔化。前一过程如图1(a)所示。常用的PBF工艺包括直接金属激光烧结(DMLS)、选择性激光熔化(SLM)、选择性激光烧结(SLS)和电子束熔化(EBM)。
在这些工艺中,SLM被认为是最有前途的工程部件,尽管它的主要限制是粉体床的尺寸。为了提高这些合金的加工性能,SLM工艺已在文献中应用于高强度铝合金AA2022、AA2024、AA2219、AA7050和AA7075。然而,人们发现,特别是AA7xxx系列合金,由于其高反射率、低激光吸收率和加工过程中的高开裂敏感性,使用SLM很难生产。因此,仍有必要在高强度铝合金中进一步开发这些工艺,以实现具有高结构完整性的无缺陷部件。
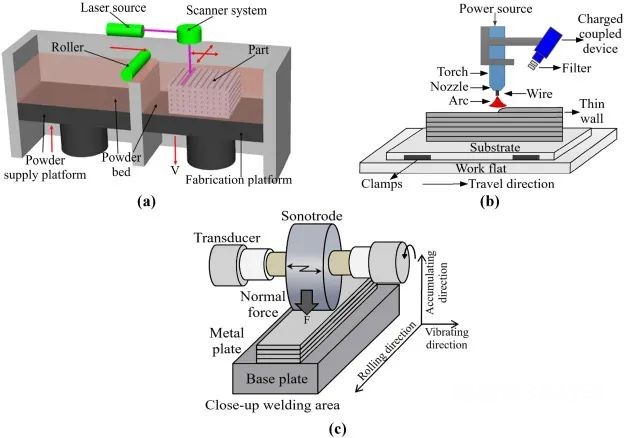
图1 铝合金AM工艺的主要类型:(a)粉床熔合,(b)定向能沉积,(c)片层压。
定向能沉积(DED)(图1(b))是一种AM工艺,在该工艺中,在沉积过程中,使用热能源(聚焦激光、等离子体或电子束)熔化铝合金中呈金属丝或粉末形式的原料。熔化沿着热能源定义的路径进行。在铝合金中,保护气体(如Ar或N)用于防止铝氧化物氧化皮的形成。DED工艺能够将所需特征添加到现有组件中,并在平坦基板上生产近净形状的组件。应用最广泛的DED工艺是线+弧AM(WAAM)和透镜工程净成形(透镜)工艺。在这些工艺中,移动式氩保护(也称为氩屏蔽)线焊机被自动引导,以生产所需零件,而不受大多数其他AM工艺中因建筑体积有限而产生的生产尺寸限制。在Cranfield大学进行的一项研究中,由AA2024、AA4043和AA5087制成的铝丝合金能够生产出高达10米长的优质部件。
在薄板层压(SL)工艺(图1(c))中,通过粘合剂(层压对象制造,LOM)或通过使用超声波(超声波AM,UAM)焊接的方式将薄金属板结合起来。该工艺还涉及使用应用激光进行切割,使用SL工艺生产的部件的尺寸精度通常低于使用上述其他AM工艺生产的部件。然而,SL工艺允许制造商在印刷时交换建筑材料,从而能够生产复合材料。在LOM机制中,使用激光源或机械切割机精确切割连续层。然后,各层通过超声波电极施加的法向力在基板顶部相互粘合,超声波电极是一种产生超声波振动的工具,通过将各层压在一起以促进粘合来实现粘合(基板和超声波电极的图示见图1(c))。该工艺可在粘接前去除和回收多余材料,不仅适用于金属材料的热粘接,也适用于陶瓷材料的热粘接。
然而,LOM可实现的尺寸精度低于PBF,因此不建议将LOM用于复杂形状零件的生产。UAM工艺用于粘合之前作为单独层打印的铝箔。在UAM的机制中,减法计算机数控(CNC)铣削(用于尺寸精度)和超声波缝焊工艺相结合,以层压铝箔以获得所需的形状。UAM是唯一一种能够在较低工艺温度下生产金属部件的AM工艺。然而,累积方向上的强度和几何精度远低于滚动和振动方向上的强度和几何精度,且更难控制(见图1(c))。
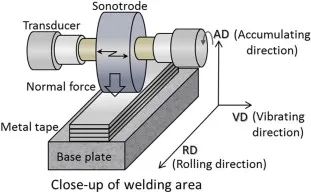
UAM流程示意图和各自方向的定义。
另一项实验中,以6061-H18铝合金为原料制备了VHP-UAM组件。将150 μm厚的胶带逐层堆叠31层,粘贴在6061铝合金底板上。元件的近似尺寸为24.5 mm(宽)× 170 mm(长)× 4.65 mm(高)。根据累积方向(AD)、振动方向(VD)和滚动方向(RD)定义试样的坐标系,如上图所示。VHP-UAM工艺无需外部加热,工艺参数为:20 kHz频率、31 μm振幅、5.6 kN法向力、35.6 mm s-1声纳极行走速度。每一个循环都将声纳极冷却到室温。从组件中切割标本,并安装在导电树脂中。用碳化硅砂纸在水中研磨,再用金刚石膏抛光。最后,在Buehler VibroMet振动抛光机上,在硅胶溶液中制备了适合于微观结构观察的表面。
(责任编辑:admin)
最新内容
热点内容