年产12,000个陶瓷3D打印零件,Steinbach AG为达芬奇手术系统开发的批产案例
时间:2023-07-11 09:29 来源:南极熊 作者:admin 阅读:次
2017年夏天,德国Steinbach AG公司收到一家知名手术产品制造商的请求,希望制造一批陶瓷管,通过这些陶瓷管输送玻璃纤维。这些陶瓷管将用于一款全新开发的达芬奇机器人手术解决方案的导向元件(其中一种常见款式如图1所示)。在测试过使用奥地利Lithoz公司的CeraFab增材制造设备打印的第一批原型组件后,客户最终选择了Steinbach来开发和批量生产这些零件。
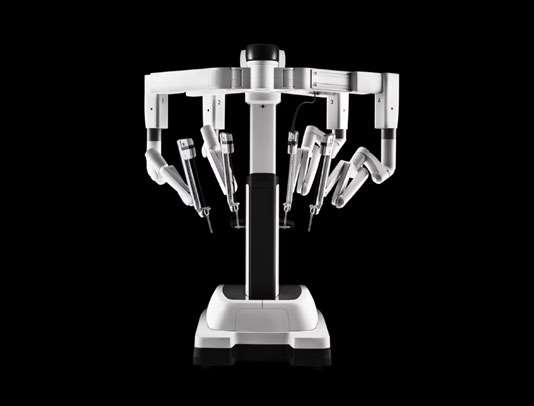
图1 达芬奇机器人辅助手术解决方案的一种常见款式“The Patient Gart”(由Intuitive surgical, inc .提供)
这些复杂的陶瓷管件只能通过增材制造来生产,其他传统制造工艺都不可能实现。由于此前从未有过类似复杂程度的部件,Steinbach使用Lithoz的LCM技术(光固化陶瓷制造)开发一种全新的创新设计,该技术被定义为增值光聚合(VPP)工艺(ISO/ ASTM 52900指南)。
制造成本和开发周期也设定了非常具体的目标——该产品仅在6个月内就投入量产。虽然开发时间紧迫,但值得称道的是Steinbach使用了Lithoz陶瓷增材制造技术,迅速将生产规模扩大到工业化量产的水平。
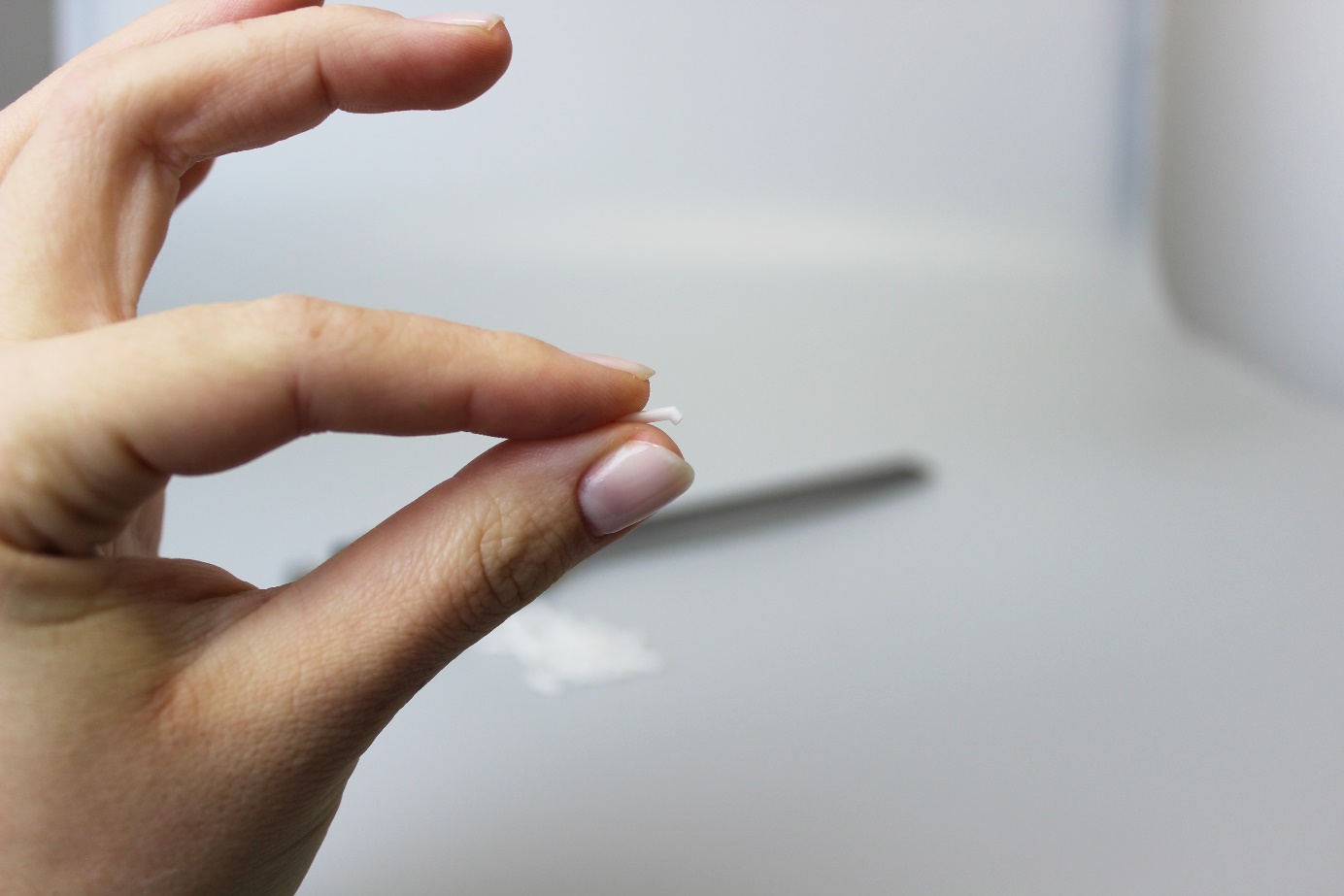
图2 Steinbach AG为达芬奇手术机器人生产的陶瓷打印管件之一(Steinbach AG/Lithoz GmbH提供)
项目和零件的主要特点
Steinbach的具体目标是在保证生产过程可扩展性的前提下,同时始终保持零件的高质量交付,并能够实现既定的成本目标。
为了满足使用要求,该项目的弯管部分必须满足两个给定的参数。首先,管的直径是由机械臂的设计决定的,管子必须插进去而不能折断。其次,玻璃纤维的质量对确保机械臂的功能至关重要,不能低于给定的临界值(该临界值决定了内部横截面)。然而,客户最关键的标准是提供尽可能低的表面粗糙度。这是为了尽量降低玻璃纤维在穿过管路时被撕裂的风险。由于应用的特殊要求,聚合物材料不能用于这些组件。
最初,人们尝试了传统的制造方法,在机械弯曲金属管之前,将玻璃纤维引入金属管内。然而,在这些尝试中,玻璃纤维在弯曲的机械应力和内部通道表面粗糙度的作用下撕裂成碎片。在使用陶瓷增材制造之前,客户也曾认为金属已经是合适的材料,并且尝试制造了金属增材制造原型件,但表面质量无法满足要求。
在客户决定研究并验证陶瓷增材制造后主动联系了Steinbach。在第一次打样后,成型的陶瓷打印零件即证明了能够提供超出客户期望的表面质量。Steinbach生产的陶瓷打印管件如图2所示。
Steinbach在项目开始时,面临的主要挑战是如何满足批量化生产订单中的一些具体尺寸要求。考虑到给定的约束条件(直径和横截面),结合急弯和复杂的内部轮廓,一种全新的管路被设计出来。这同时也导致了所需的最小壁厚仅为200μm(图3)。此外,粗糙度最大为Ra = 0.4的完美光滑表面,外部几何形状±20μm的高精度公差,以及每年生产12,000个零件的需求,这意味着只有发挥Lithoz陶瓷增材制造技术的全部创新潜力才能满足该项目的这些所有要求。
为了满足客户的成本预期,Steinbach将第一批零件所获得的优异材料性能转化为大规模的批量生产能力。具体实施分三个阶段进行,每个阶段都有各自的挑战。本文将关注讨论项目实施过程中的关键标准:生产力、过程稳定性、质量保证和经济效率。
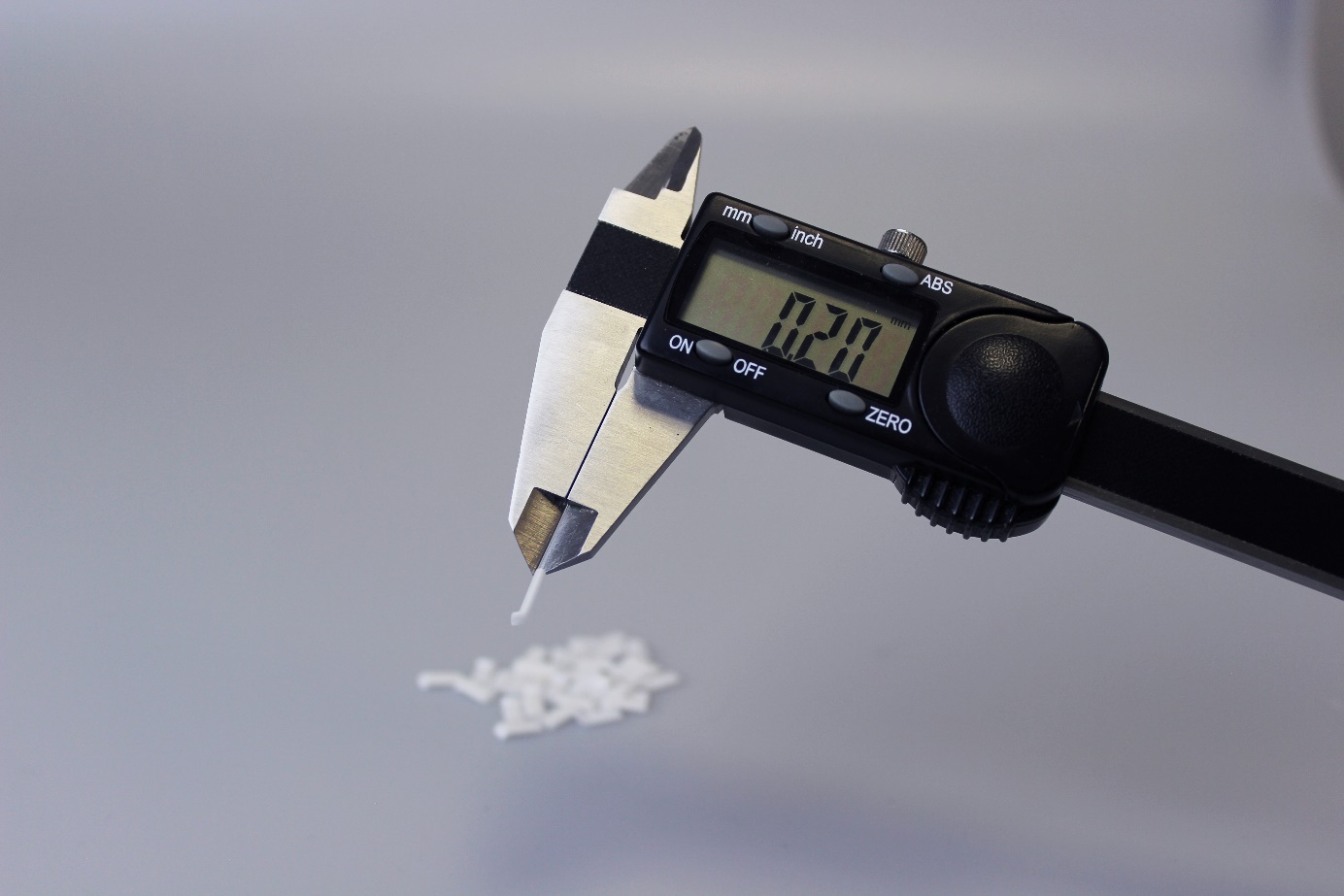
图3 每个陶瓷增材制造管件的最小壁厚必须达到200微米(Steinbach AG/Lithoz GmbH提供)
阶段1:使用LCM技术为组件找到合适的设计
Steinbach使用增材制造设计(DFAM)方法来生产复杂的几何形状,与客户密切合作,以确保在数千个组件的批量生产过程中管件的全部功能得以保障。对于客户来说,零件满足尽可能多的要求以确保完美的功能和精度是至关重要的。
本研究阶段有三个主要特点:
●确保最小壁厚为200μm
●批量生产的排胶和烧结工艺优化
●能够建立并保持100%的质量控制
与客户就流程达成一致之后,项目就进入概念验证阶段。在这一环节,应用验证需要两种不同长度的管件。
LCM的技术特点决定了几乎不需要调整原来的零件设计。因此,Steinbach只需要专注于优化高效批量生产的工作流程,而不是增材制造工艺本身。
原则上,弯曲组件本身的设计在这个阶段对LCM技术来说只是一个小挑战,并且相对容易实现。无论是该设计的弯曲部分、通道以及角度都无需为打印过程进行额外调整。在此类项目中,一个常见的难点是如何非常小心地处理如此精细和超薄的陶瓷部件,但是得益于增材制造的快速定制化生产特性,这一挑战可以通过一些微小的结构设计更改来克服。
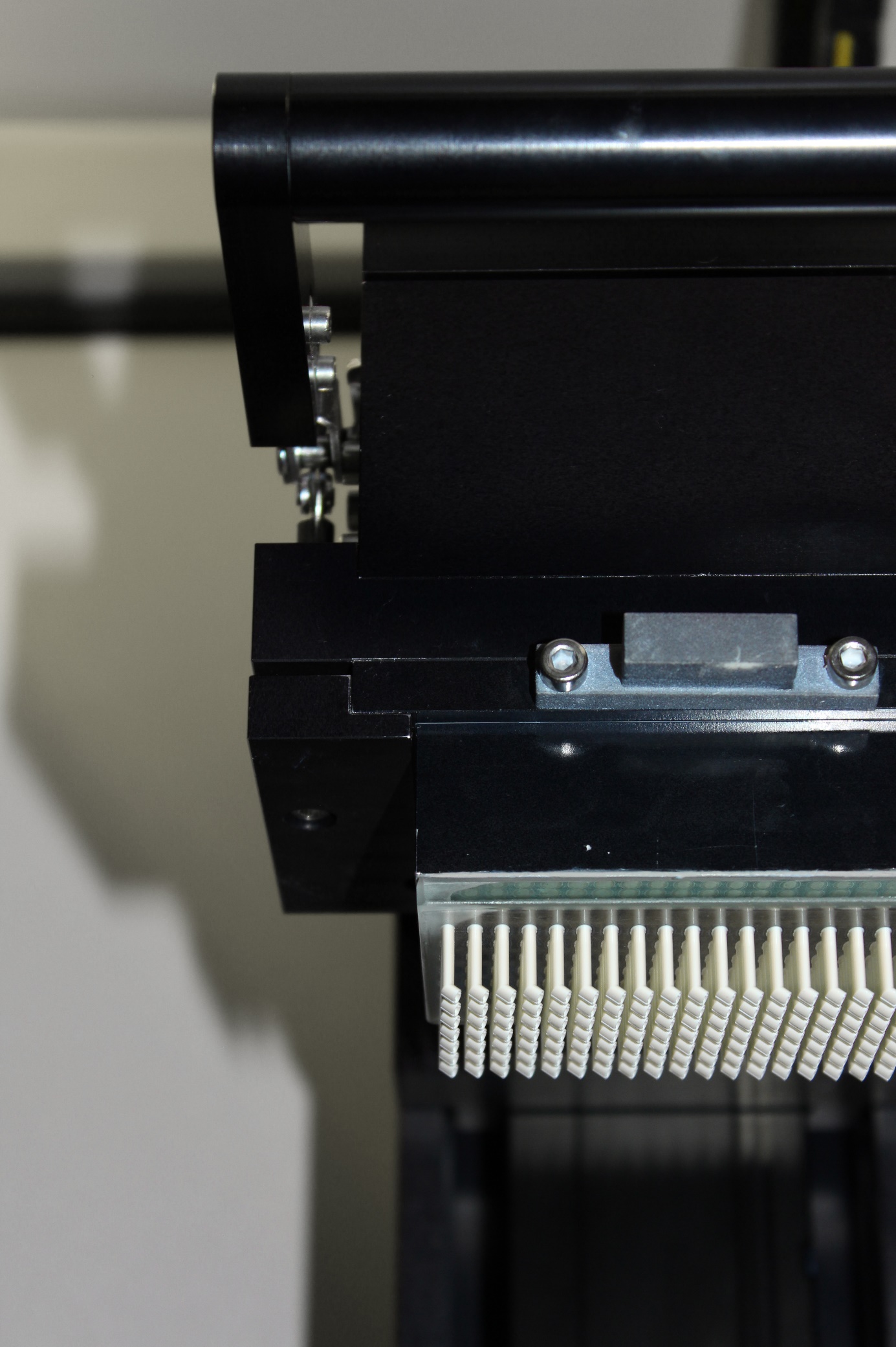
图4 Lithoz陶瓷打印设备的打印平台视图(Steinbach AG/Lithoz GmbH提供)
Steinbach遇到的最大挑战是,必须在弯管内填充精确数量的玻璃纤维,且玻纤材料或陶瓷管本身不能有任何破损——也就是说,客户需要将整个弯管安装到已经定型的手术机器人手臂结构给定的尺寸中,并保证其横截面与玻璃纤维的质量完全匹配。经过大量研究测试,最终确定了最小横截面,从而得出了0.2 mm壁厚的设计要求。这些参数限制将产品设计重点集中在管壁的优化上,即找到一种方法来减少管壁的厚度且不破坏管壁,同时能够实现稳定连续的生产过程。因此,壁厚是该应用最大的设计挑战,也最终成为其概念验证阶段的重点。
尽管Steinbach已经在增材制造陶瓷部件的热处理方面积累了丰富的经验,但在保障经济性的前提下,要扩大产量,就必须对整个加工过程进行大幅度的改良。例如,弯管的精确平衡位置和数量必须得以保证,以确保零件的最低废品率,因为如果它们在形状或长度上出现即使最轻微的偏差,就无法投入使用。图4、图5为打印平台上按照批次生产的陶瓷零件。
Steinbach利用优化的加热工艺和曲线进行了多次测试后,最终找到了最佳的热处理方式。在尝试过将陶瓷弯管进行直立或水平的不同放置方式后,最优的放置方式为:将较短的零件进行“俯卧”放置,而较长的零件进行“仰卧”放置。最优的烧结批次为每8版打印后进行一次烧结。
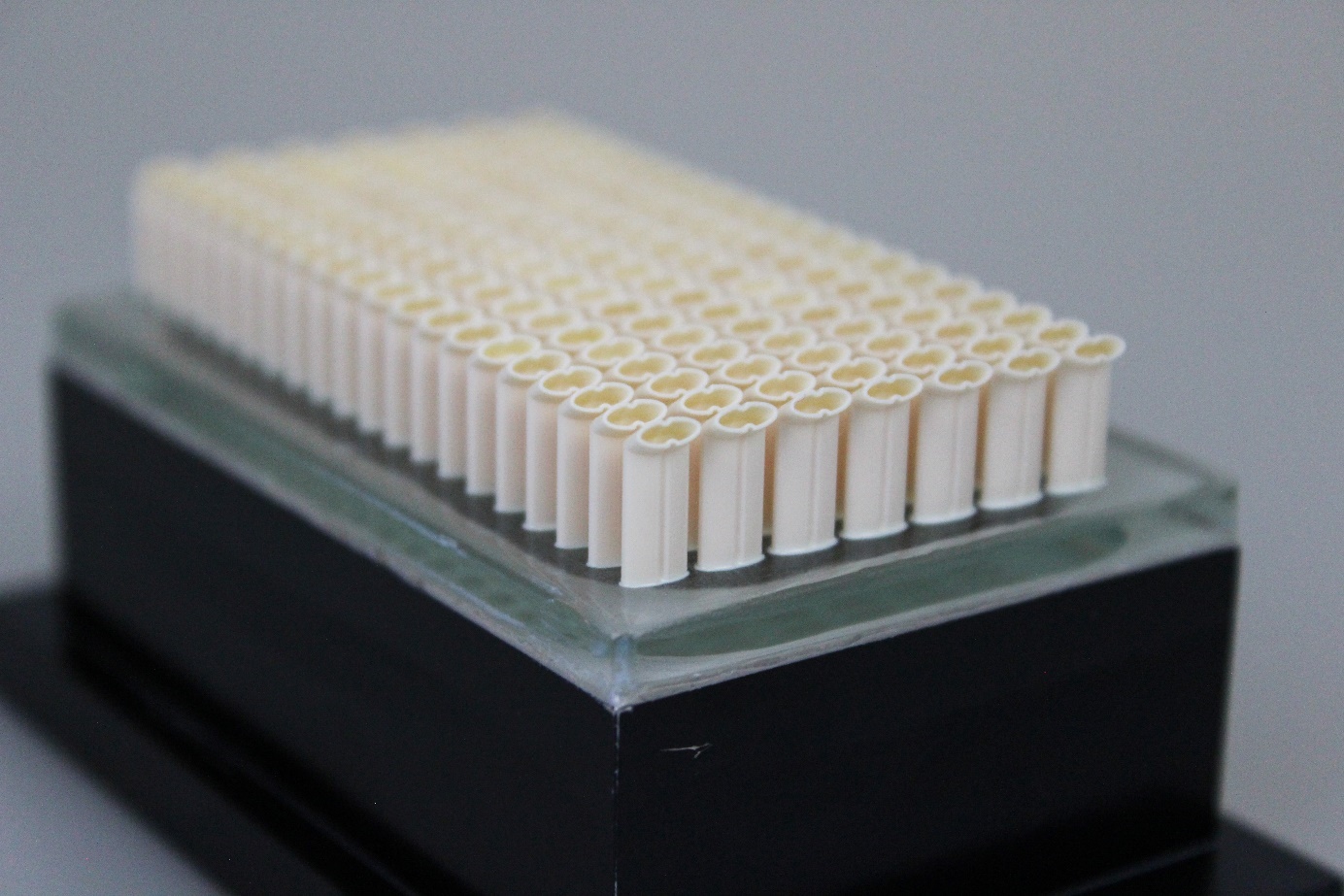
图5整版待处理的打印完成零件(Steinbach AG/Lithoz GmbH提供)
即使是概念验证阶段的原型件,也总是会保证在接近量产条件下对其各项功能进行测试,以确保零件的质量从第一次迭代开始就为后期批量生产模式做好准备。在生产过程中必须保证极小的公差,以保持零件尺寸尽可能完全一致。
Steinbach同样密切关注质量管理并严格遵循相关要求。他们建立了一个三步质量检查流程,应用于每一个生产的陶瓷弯管:
●显微镜检查零件表面缺陷
●游标卡尺测量准确的长度
●由客户提供的定制仪器检查形变
在原型概念验证阶段,Steinbach对产品设计进行了多次更改,得益于增材制造的数字化生产流程,这些设计更改可以轻松快速的实现验证。在每次收到原型产品后,客户也能够给出准确的反馈。每一次验证打印生产的原型件包含6根弯管,所有弯管都必须承受7周的使用周期。因此,整个迭代的测试周期相对较长,完成后才能实现进一步的设计调整,以及制造更新后的新版原型零件。
第一阶段的迭代优化进行了大约一年时间,并最终在客户现场进行了最终原型的验证通过,认可该增材制造零件的几何形状设计方案。
阶段2:工业化批量生产
随后,Steinbach的陶瓷增材制造团队专注于优化工艺细节,以确保批量生产中零件性能的可重复性,并且不会出现任何质量问题。为了实现这一目标,必须充分探索和发挥LCM技术的巨大潜力。这一阶段主要关注两个特点:
●设置适合的打印底板涂料以便于从打印平台上移除零件
●优化后处理清洁过程
软件功能部分的优化是在与Lithoz密切合作下进行的。优化后的软件功能提供的高精度和稳定复现能力也显著减少了次品数量,从而节省了大量材料,时间和成本。
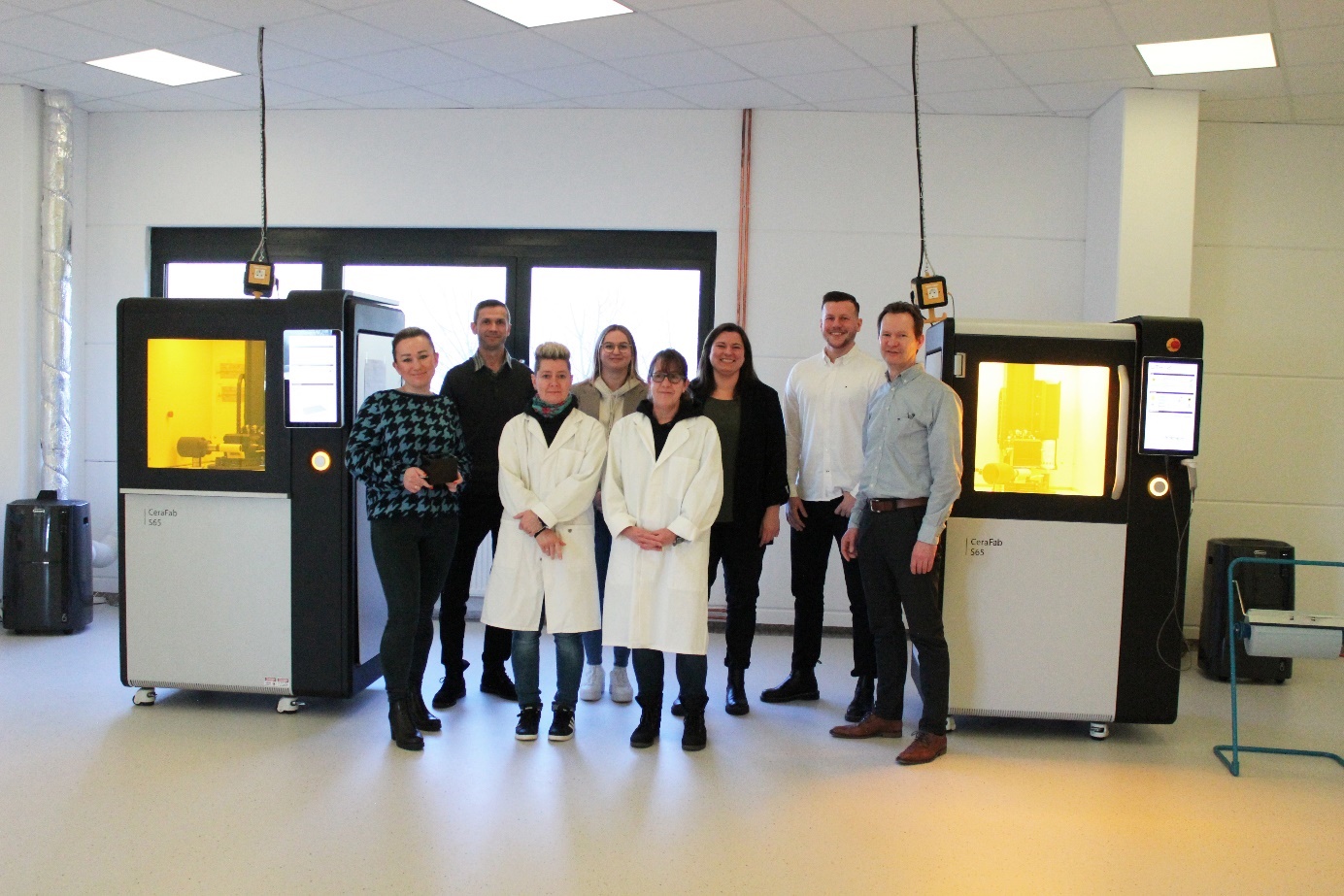
图6 Steinbach陶瓷增材制造团队,公司运营着4台Lithoz 陶瓷打印设备(Steinbach AG/Lithoz GmbH提供)
为了能够实现批量生产,Steinbach需要找到一种更高效、更安全地从打印平台上移除打印零件的方式。在试用了Lithoz提供的两种标准底板涂料后,一种新的特定的两种混合涂料被开发出来,该成分在满足产品生产规格要求的前提下,能够大幅改良零件后处理效率。除此之外,还进行了系统性探索以寻求制造过程中的最优设置条件 (例如,后处理时间被适当延长,以确保最终零件在每次热处理后都不发生任何变形)。
与其他工序一样,陶瓷弯管的清洗也必须满足该项目整体的成本控制水平。从最初只能用镊子纯手工处理清洗过程开始尝试,逐步测试了各种清洗剂。Steinbach很快开始尝试使用超声波清洗零件,并对超声水浴的温度和处理时间进行了调整,以获得最佳的拟合参数,从而实现了更经济有效的清洗工艺。
在第二阶段尾声,整个过程能够得到精确的管理和控制——不论是陶瓷浆料还是料盘批次管理,从增材制造设计,到环境湿度和温度水平,再到后道热处理工艺。基于使用Lithoz CeraFab的软件系统,每个生产步骤的工艺参数都能够被详细记录下来,在整个过程优化中获得的数据也可以作为未来改进和质量保证的分析基础,以及在后续项目中作为合理决策的统计数据基础。整个体系建立起来之后,此类文件会被归档为Steinbach的制造服务内部标准。
最终,第二阶段的工艺优化使制造成本又降低了40%。在这一阶段达到了最高的效率和优化水平后,客户被带到Steinbach工厂体验了为期两天的生产全流程,零件产品在这两天内进行完整流程的打印制造和后道处理。在这次成功通过客户认证的生产流程之后,客户对整个项目的最终产品质量和价格都表示满意,这也标志着第二阶段的圆满完成。
阶段3:连续生产的持续优化
在接到订单六个月后,Steinbach按时交付了第一批批量生产的零件。一旦该工艺被设置为批量生产模式,根据客户对手术机器人的需求,生产批次的数量就会持续增长,而不是分批次增量。到2019年7月,随着销售数字的增长,达到了每年12,000件的产量水平。
从第一次批量生产运行到实现完整产能,通过进一步逐步优化各项参数,进一步减少废品率,Steinbach实现了将单件制造成本再降低40%,在满足技术要求的框架范围内进一步提升了产品的性价比。
在批量生产过程中,Steinbach坚持严格的100%测试政策,从原型到批量生产,对每一根陶瓷弯管都进行了完整的测试,以确保完美的质量交付,包括前文提到的特定长度的各项检测以识别潜在形变。每次新的设计调整都会经过客户对最终样品实物的认可,任何后续的反馈都会由Steinbach陶瓷增材制造团队及时解决。
为了完整交付整个产品流程,Steinbach甚至在内部开发了自己的包装解决方案,以统筹处理这些高度敏感部件的物流问题。专门设计的载具能够确保包装步骤简易快速,并确保运输安全。
项目圆满完成
通过建立以利润为导向的陶瓷增材制造部件生产,Steinbach迈出了从理论到商业实践的决定性一步。由于其对整个制造工艺的持续优化-从概念验证的原型制造到LCM技术对工业化量产的适配调整,再到对批量生产中参数的持续改进——Steinbach不仅开创性地探索了增材制造高性能陶瓷部件的批量生产模式,而且成功地实现了整个价值链的预期投资回报率(ROI)。
由于该项目的成功完成所涉及的密集研究和开发,Steinbach的这个项目可以作为高性能陶瓷增材制造工业应用的绝佳商业化案例之一。在这个项目之后,Steinbach又获得了几个新客户的订单,除了一些小规模的试生产之外,这些订单的零件数量都在每年10,000- 15,000个范围。
在该项目过程中,Steinbach陶瓷增材制造团队在生产过程中也获得了完备的能力——从零件设计到后处理再到成品烧结部件的运输规划。后来的客户同样从Steinbach的丰富项目经验以及质量管理和性能交付水平中获益良多。后续各类批量生产的陶瓷增材制造部件如图7所示。
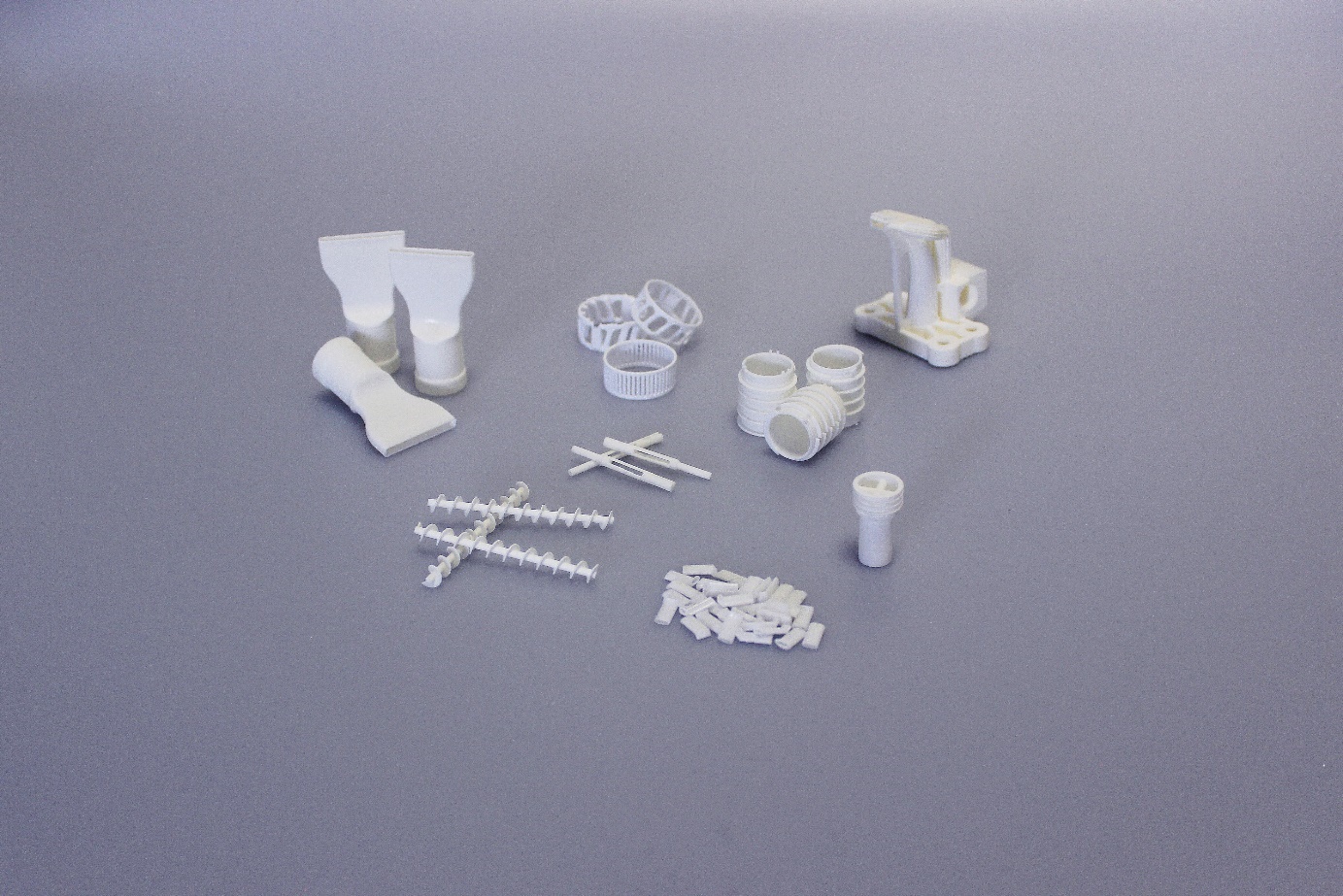
图7本文提到的陶瓷弯管,连同其他陶瓷打印零件,均由Steinbach(由Steinbach AG提供)进行批量化增材制造而成
这项开创性的探索非常成功,它不仅仅帮助实现了外科手术中的一项技术升级,更有助于在整个陶瓷增材制造工艺链上建立一个重要的陶瓷增材制造知识库。Steinbach每年生产12,000个零件的成就同时也证明了Lithoz CeraFab陶瓷打印设备的优异性能,目前同类设备也被全球众多客户用于批量生产不同应用产品。
(责任编辑:admin)
最新内容
热点内容