螺杆挤出熔融沉积建模增材制造致密氧化锆陶瓷
时间:2021-10-09 14:31 来源:未知 作者:admin 阅读:次
在这项工作中,作者提出一种基于螺杆挤出的适用于高固体负荷原料的FDM方法。确定了氧化锆陶瓷增材制造螺杆的优化结构参数和加工窗口。并对烧结陶瓷的层间结合和机械强度进行了评价。研究结果表明,基于螺杆挤压的FDM方法用于制备复杂形状陶瓷零件是可行的。
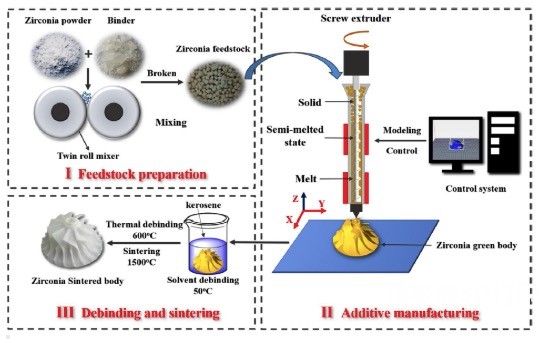
图1 螺杆挤出熔融沉积致密氧化锆陶瓷流程
该研究制备氧化锆陶瓷部件的加工流程如图1所示。首先,将氧化锆陶瓷粉与有机粘结剂混合得到原料。然后,将原料板通过螺杆送入料管,再加热,从喷嘴挤出。陶瓷坯体逐层制造,然后在有机溶剂中进行脱脂。最后,通过热脱脂和烧结得到致密的陶瓷零件。
挤出流量主要受螺杆转速和机筒温度的影响,是评价螺杆挤出装置性能的重要指标。当螺杆转速为5 r/min、10 r/min、15 r时,在130 ~
190 C范围内均可获得连续稳定的挤出效果。在较高的螺杆转速(20r /min和25r /min)下,原料不能在130℃和25r
/min下连续挤出。
当筒体温度超过150℃时,挤出膨胀效果不明显,当筒体温度达到160℃后时,挤出的线材直径几乎与喷嘴尺寸相等,有利于较高的印刷精度。这可能是由于温度较高后材料粘度变低,流动性变好导致的。因此,筒体温度是决定挤出线直径稳定性的关键因素,对打印精确性非常重要。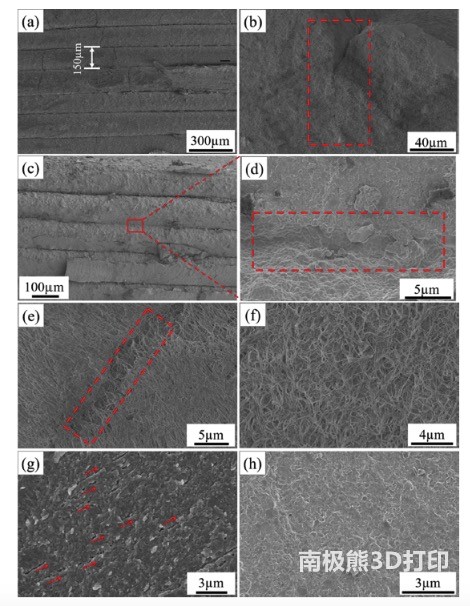
图2 打印件SEM图像
本研究主要关注的两个方面是表面质量和层间结合。表面质量直接关系到烧结材料的精度和后续的加工成本,而层间结合则影响烧结材料的可靠性。在层厚为0.15
mm的表面拍摄的SEM图像如图2(a)所示。表面各层之间的间隙是可见的,FDM技术很难避免。然而,从截面图像估计,这种层间缝隙的深度仅为0.1
mm左右(图2(b))。在收缩率为20%左右的烧结后,层厚度变为0.1
mm(图2(c)),在图2(d)放大图像中可以清楚地看到,层间区域的显微组织与内层一样致密均匀。图2(b)和图2(d)中的红线标记了印刷和烧结部分的层间区域。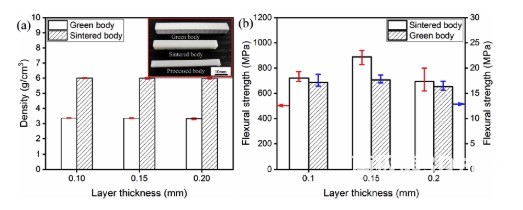
图3氧化锆陶瓷打印密度及强度
图3为测试不同层厚时坯体和烧结体的密度和弯曲强度。层厚度对印刷体和烧结体的密度没有显著影响(见图3(a))。坯的密度为0.35 g/cm3,达到3Y-TZP理论密度的58%,烧结坯的密度约为6.0 g/cm3,达到TD的99%。如图3(b)所示,不同层厚制备的坯体抗弯强度达到注塑坯体30mpa抗弯强度的一半以上,证明坯体内部的层间粘结足够。厚度为0.15 mm的烧结体强度超过厚度为0.1 mm和0.2 mm的烧结体强度,达到890MPa,接近干压或注塑所能达到的水平。进一步优化印刷参数,以最大限度地减少加工缺陷,并提高制备材料的可靠性将在后续研究中进行。
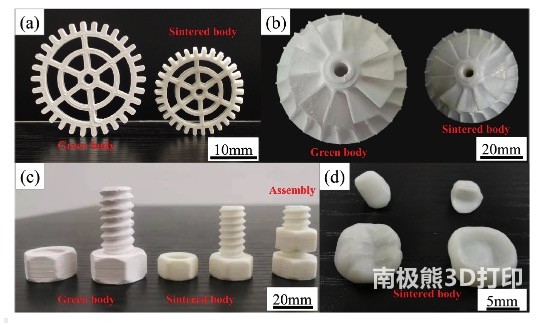
图4 螺杆挤出熔融沉积致密氧化锆陶瓷零件
图4为本研究开发的FDM法制备的一些氧化锆陶瓷零件。矩形棒料从印坯到烧结件的纵向线形收缩率为20.5%。通过对比坯体的几何形状,证实了该方法具有可靠的保形能力(见图b))。基于螺杆挤出的FDM系统适用于打印高固相含量的ZrO2颗粒料,对其他工程陶瓷如Si3N4和Al2O3的增材制造也具有广阔的应用前景。设计螺杆直径为12mm,长宽比为17:1,紧凑比为2.34。其强度足以承受挤压过程中产生的剪切应力。通过对打印温度、螺杆速度和喷嘴尺寸的监测,优化了获得稳定、精确可控的挤出流量和充分的层间结合的均匀组织的加工窗口。氧化锆坯体和烧结氧化锆坯体的密度分别达到理论密度的58%和99%,接近干压或注射成型所能达到的水平。验证了基于螺杆挤出的FDM系统适用于复杂几何形状陶瓷零件的打印,尺寸精度可控。
(责任编辑:admin)
最新内容
热点内容