英国研究人员使用FFF 3D打印改进头骨碎片的CSI分析
“熔融长丝制造(FFF)3D打印被证明是创建骨骼碎片的物理复制品,执行物理配合分析(PFA)和骨骼碎片重建的准确而有用的方法。因此,我们建议将μCT成像与FFF 3D打印配合使用,这是在处理小碎片和烧伤的骨头时进行无损物理拟合确认的绝佳选择。”研究小组说。
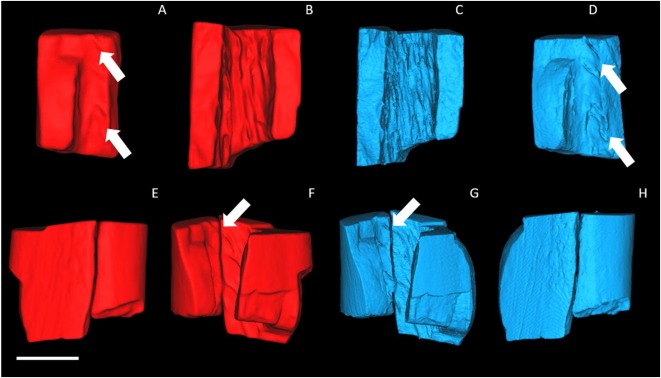
为了评估PFA重建的最佳3D扫描过程,研究人员产生了两组骨碎片(如图)。图片来自Science Direct。
犯罪现场调查中的身体适应分析
CSI通常要求调查人员检查一系列物品作为证据,包括人体遗骸,其中一些遗留物可能因事件期间遭受的创伤而损坏或破碎。这些遗体通常会通过PFA确定它们是否适合。如果此过程导致良好的身体适应,则可能会将犯罪嫌疑人置于犯罪现场,或促进可能解决案件的物体重建。但是,PFA涉及大量匹配和手动处理事项,这可能导致碎片在处理过程中受损。
此外,在某些情况下,PFA可能极富挑战性,例如碎片可能构成生物危害,非常小或骨骼本身太脆弱而无法移动。考虑到重建过程通常涉及将零件粘合在一起,这可能会引起问题,并使研究人员无法充分了解创伤的性质。这使得某些形状的骨头难以记录或呈现,特别是那些具有三维复杂性质的碎片或嵌入外部材料中的碎片。结果,这种情况显然是不足以在法庭上陈述。
尽管3D扫描和建模已在一系列法医人类学应用中使用,但骨骼碎片的处理和重建仍然是一个问题。例如,目前在肢解,武器匹配,颅骨测量和面部重建案例中使用3D建模。扫描允许在某些情况下获得纳米级的高分辨率图像,但是它们往往费时很昂贵,并且需要专业知识和软件来操作。另一方面,表面扫描方法往往更便宜且更易于使用,并且通常用于事后定量损伤分析,标记和软组织损伤分析。
同时,增材制造已被证明足够精确,可以产生用于颌面外科手术的牙科模型。研究还证明了3D打印在法医证据的可视化和分析中的适用性,研究人员着手结合这些技术来创建3D打印的颅骨骨折复制品。这些3D模型提供了PFA发生的可能性,而不必过多地处理原始证据碎片,同时最大程度地减少了损坏或污染的风险。此外,此类模型以引人入胜且易于理解的格式提供360度可视化,同时可用于提高审判期间的陪审团理解力。
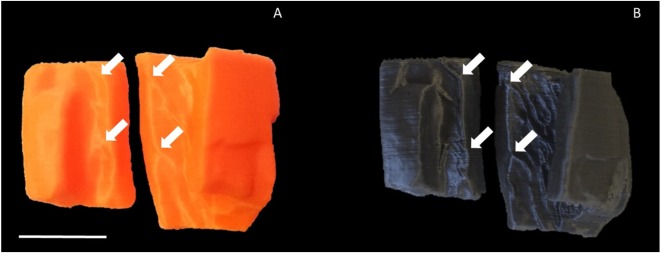
虚拟模型的3D打印副本,与SLS扫描模型(左)相比,μCT扫描模型(右)显示出更强的凸脊细节。图片来自Science Direct。
3D打印头骨碎片副本
研究人员将体积扫描技术微计算机断层扫描(μCT)与表面扫描技术结构光扫描(SLS)进行了比较,以评估两种方法之间的优缺点。为了测试其进行PFA的潜力,团队3D打印了两个烧伤骨碎片模型,以模拟真正调查中可能遇到的损伤。
以朴茨茅斯大学捐赠的考古人类股骨为模型,将复制的骨骼样品切割并在Gallenkamp马弗炉中于600°C燃烧30-60分钟。在燃烧过程中或冷却过程中,骨骼的每个部分自然会自然地纵向分成至少两个单独的碎片。对两个相邻的碎片进行3D成像和打印,以评估它们在可视化和分析烧伤骨碎片的物理适应性方面的技术。
用于测试的SLS扫描仪是Shining 3D EinScan Pro +,而较大的μCT蔡司Xradia 520 Versa扫描仪也因其设置简单和无损过程而被选中。扫描后,使用PLA灯丝通过FFF Prusa i3台式打印机对片段进行3D打印。选择最佳打印质量(0.15毫米),并将填充量设置为0%,以创建完全空心的打印。然后,在成对的3D打印骨骼模型上进行PFA,其准确性取决于两个片段之间的特征匹配和对齐以及配合的触觉“感觉”。
两组烧焦的3D打印的股骨碎片(如图所示)都可以重新拼凑在一起。图片来自Science Direct。
发现3D打印在μCT和SLS模型中都保留了很高的细节水平,总的来说,所产生的打印质量足以执行PFA。根据团队设定的“适合质量”标准,发现与SLS打印相比,使用μCT打印可以更轻松地确认身体是否合适。此外,在创建的所有片段对中,μCT模型都提供了更紧密,更牢固的拟合,从而产生了更详细的表面结构,这在特征匹配中具有重要意义。
中国3D打印网点评: 可以使用FFF 3D打印来生产具有足够细节水平的骨骼碎片副本,从而可以使用任何一种3D扫描技术。此外,该团队建议,通过消除对FFF生产过程中使用的支撑结构的需求,选择性激光烧结(SLS)3D打印可以证明是在将来的研究中生产模型的更有效方法。研究小组说,虽然最终证明实施起来会更昂贵,但SLS印刷也将带来更高的表面光洁度。此外,成功复制的骨骼碎片可以为PFA工艺其他方面的3D打印打开新的应用程序。
与传统方法相比,将3D成像和打印应用于PFA具有许多优势。高度碎片化,脆弱且可能嵌入的遗骸的虚拟重建提供了一个机会,可以在不损害原始骨骼碎片的情况下进行完整重建。此外,可以按比例放大按比例放大来自特别细小的碎片或骨头的3D打印件,生成3D复制品以可视化装配并在以前极具挑战性的项目上执行PFA。
中国3D打印网编译文章!
(责任编辑:admin)