军用飞机金属零件激光增材修复技术的研究进展
时间:2023-03-01 14:07 来源:航空材料学报 作者:admin 阅读:次
传统的飞机金属零件修复主要集中在表面处理工程和焊接修复技术,如增材制造、激光熔覆、激光熔凝、冷喷涂、电弧堆焊以及搅拌摩擦焊等[3]。上述技术具有修复成本低、灵活性强、技术应用成熟以及使用范围广等优势,但也存在易污染环境、易损伤基体材料、修复区结合力不强、修复精度以及自动化程度较低等缺点[4]。
激光增材修复(laser additive repair,LAR)技术是激光增材制造技术在金属零件修复领域的具体运用。通过对零件中损伤部位进行准确建模后开展定制化修复,具有修复速度快、效率高以及修复后零件性能优良等优势[5]。LAR技术已在飞机机翼前缘、发动机叶片、垂尾梁、摇臂、支架以及起落架活塞杆等损伤金属零件的修复中获得成功运用,部分零件已通过了多次装机应用和验证考核,应用范围不断扩大,必将在航空维修领域受到更多关注[6]。本文介绍激光增材修复技术特点,阐述激光增材修复过程中常见的缺陷类型,总结激光增材修复技术工艺优化特点以及在维修中的应用,并对激光增材修复技术未来的研究重点和趋势进行探讨。
1. LAR技术特点
激光增材制造技术是激光熔覆和激光快速成型技术的有机结合,主要以金属粉末或者丝材为原材料,将CAD目标成形模型进行分层处理,再利用高能激光束熔化原材料实现堆积生长成形,是一种能够快速将复杂结构的三维数据模型直接转化为实体零件的数字化制造技术[2,5]。在具体运用过程中,采用预置金属粉末方式的称为选区激光熔化成形技术,采用同步输送金属粉末或者丝材的称为激光直接沉积成形技术。国内外众多学者,又将激光直接沉积成形技术称为定向能量沉积、激光金属直接成形、激光近净成形、直接激光制造、形状沉积制造以及激光立体成形等技术[3-6]。
选区激光熔化成形技术是控制高能量的激光束按照预定的扫描路径,熔化预先铺覆好的金属粉末后逐层熔覆堆积,冷却凝固后成形的一种技术[7-8]。激光选区熔化技术原理图如图1(a)所示。由于铺粉类固有的工艺特征,决定了选区激光熔化成形技术对于大型复杂构件的修复存在局限性[2,4-6]。
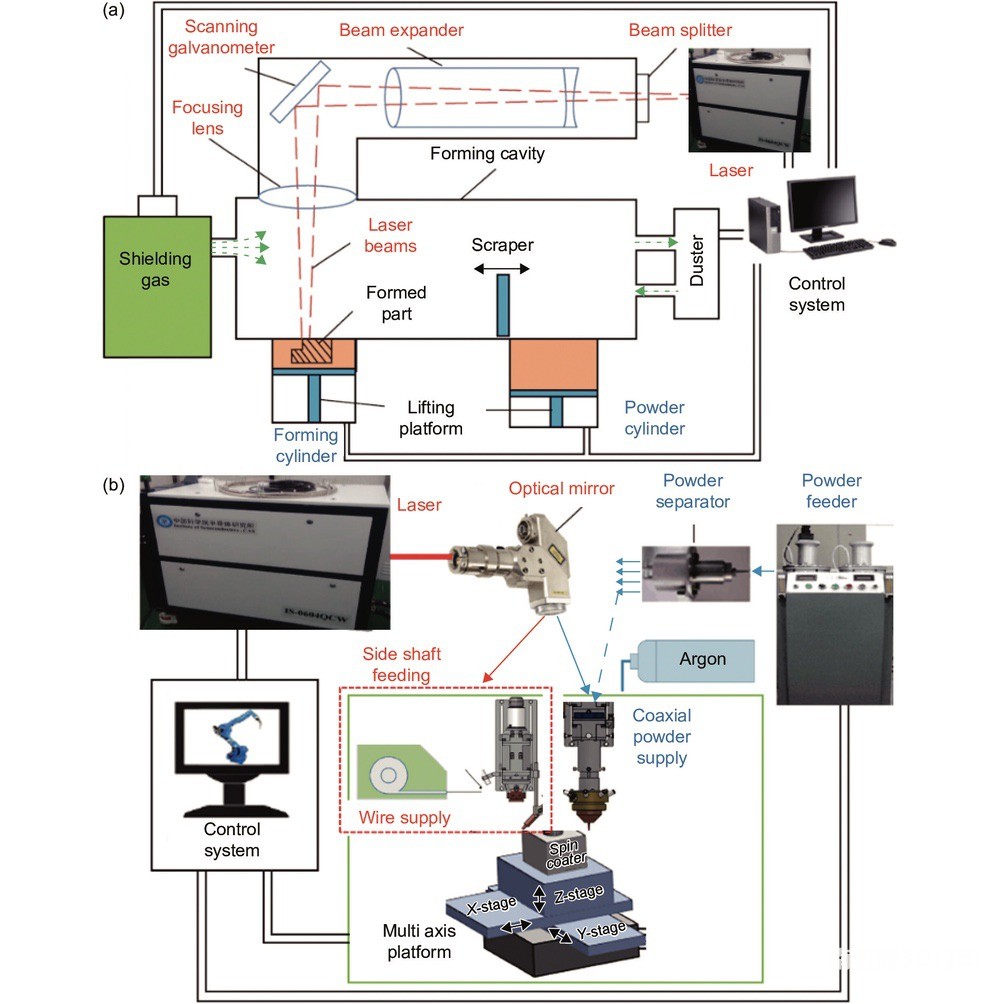
图 1 激光增材制造技术原理图 (a)激光选区熔化技术[7-8];(b)激光直接沉积成形技术[9-10]
激光直接沉积成形技术是以金属粉末/丝材为填充原料,采用高能激光束将填充材料逐层熔覆堆积,从而形成金属零件的制造技术[9-10],其原理如图1(b)所示。
旁轴送材方式加工平台易搭建,但送材方向性较强,输送材料容易受热不均匀;当激光扫描路径较为复杂时,旁轴送材方式的成形控制难度增加。激光束同轴送材方式则无方向性问题,能保证任意路径下熔覆层的一致性,从而获得更为广泛的应用[5-6]。按照激光束和金属粉末的相对位置,同轴送粉方式又可分为光外同轴送粉和光内同轴送粉[6],如图2所示。同轴送粉方式的金属粉末与激光束同步输出并汇聚于激光焦点处,能提升粉末利用率,设备简单且更适合精密成形。与金属粉末相比,制备丝材所需成本更低,所以光丝同轴激光增材制造技术近年来也受到极大关注[11]。
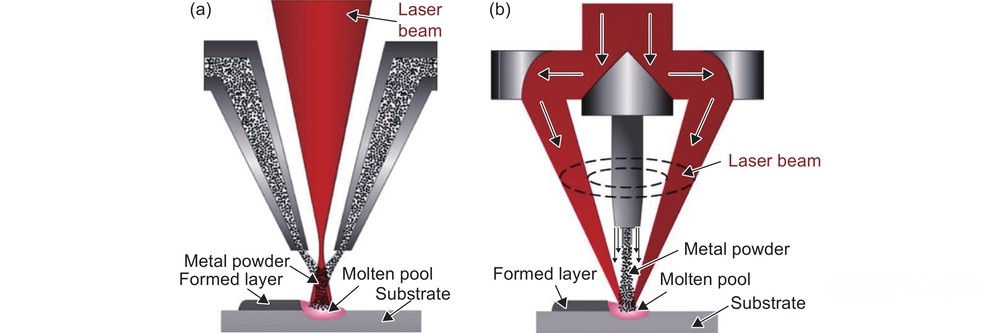
图 2 同轴送粉原理示意图[6] (a)光外同轴送粉;(b)光内同轴送粉
与常规激光熔覆技术相比,超高速激光熔覆使粉束汇聚点位于熔池上方,同时提高光束和粉束的汇聚性,大部分激光能量(约80%)作用于合金粉末,使粉末在落入熔池前处于熔化或者半熔化的状态,进而减小了粉末在熔池内的熔化时间,减少激光对基体材料的热输入量,成形质量优良[12-13]。超高速激光熔覆的沉积速率由常规激光熔覆的0.5~2 m/min提升至20~500 m/min,单次熔覆厚度能够控制在0.02~1.0 mm,可直接用于修复较薄零件[14]。该技术具有更高的工作效率,如果能代替常规激光熔覆技术与快速成型技术相结合,将有助于推进LAR技术的进一步发展。
激光-电弧复合增材制造技术是将激光和电弧两者的热源进行复合,共同作用于材料待熔化区域,其交互作用能够产生优势互补效果[14]。在成形过程中,先启动电弧能量使材料发生熔化,激光能稳定电弧且能对熔池产生搅拌作用,可促进气孔的快速逸出,并使形核生长的晶粒破碎从而细化晶粒。气孔数量的减少以及晶粒的细化,能使修复零部件具有更好的力学性能。
与激光增材制造技术相比,LAR技术有其自身的特殊性,需要根据修复对象的损伤类型和结构特点进行工艺规划,并且要考虑与零件基体的结合效果。
飞机零部件LAR工艺流程主要包括:
(1)借助清洗设备对缺陷零件进行清洗处理,并对零件进行无损检测判定损伤类型以及安全评估,结合相应的修理手册标准评估其可修复性。
(2)受损区域形式多样,为方便激光扫描路径的形貌特征需求、增强修复效果,对受损部位按修理标准进行V型或U型等规则化处理。对缺乏原始三维设计数据的零件,利用工业CT、三维激光扫描仪等对待修复区域进行精确测量。
(3)采用逆向建模技术进行数据处理,获得光顺的曲面、平面、实体等特征,再构建较为完整的修复目标模型。将连续的三维CAD模型离散成具有一定层厚及顺序的分层切片,根据切片轮廓设计合理的LAR工艺参数并转换成相应的数字控制程序[15]。
(4)依据修复目标模型,以损伤零件为基体,对修复区域进行激光增材制造,得到修复后的零件。
(5)与维修手册标准进行比对,进行性能测试以及装机检验等方式确定修复效果,检验修复后零件的“修形修性”情况。
综上所述,LAR技术可总结为以高能量密度的激光束作为热源,以金属粉末或丝材等为填充材料,借助CAD等软件对目标模型进行预分层处理,通过控制系统使激光光源、保护气体、填充材料输送装置和载物工作平台按指定空间轨迹运动,以修复零件为基体对待修复部位进行逐层成形,最后生成与待修复部位形性接近的三维实体,完成对损伤零件的几何形状和使用性能的恢复,延长其服役寿命。
2. LAR中缺陷类型和调控方法
在立体型飞机零件LAR过程中,激光循环往复进行逐点扫描熔化→逐线扫描搭接→逐层凝固堆积,材料先后经历快热、熔化和快冷等过程,导致修复区易出现如塌边、表面球化、气孔以及裂纹等不同尺度缺陷。
2.1 塌边
在LAR过程中,高能激光束、填充材料与基材相互作用,形成的熔池主要受到重力(G)、保护气体气-固两相流影响力(M)、熔液表面张力(N)和基体支撑力(Z)的混合作用,熔池在这四个力相互作用下与水平面形成一定的倾斜角θ,如图3(a)所示。当激光束完成第H层的最后一道扫描时,第H+1层第一道如果也在该侧进行扫描,将导致每一层第一道处(即扫描经过进出端和边角处)的热量累积比其他区域温度要高,使熔池的表面张力减小,熔体的流动性增加,凝固层变薄,导致成形件边缘出现塌陷现象[16]。当底层修复区域发生塌陷时,该区域较实际沉积高度更低,如图3(b)所示。在纵向分层厚度不变的情况下,激光束扫描至该区域时,离焦使激光光斑直径变大造成能量密度降低,熔化粉末的能力下降;随着修复层数的增加,出现塌边变形现象,如图3(c)所示。
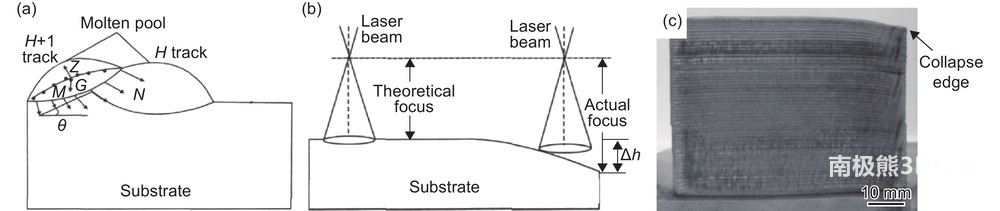
图 3 LAR成形件塌边现象[16] (a)熔池受力作用示意图;(b)塌陷时光束作用示意图;(b)塌边实物图
在修复薄壁零件或者零件边缘区域时,采用短边往复并逐层更换激光起光点位置,以及针对熔池高温区吹冷却气体、延长停留时间等方式来降低材料热量累积效应,可减小几何缺陷现象的发生[17-18]。
2.2 球化缺陷
在LAR过程中,填充材料熔化液在表面张力的作用下进行收缩,球形表面积和表面能较低且最为稳定,如果熔液与固体基体表面润湿性较差时,熔液难于均匀铺展,易发生球化反应形成球化缺陷[19],如图4(a)所示。激光扫描速度较快时,激光束冲击熔池易引起熔液飞溅。飞溅出熔池外的熔液只受重力作用且接收激光能量较低,易形成小尺寸球型金属颗粒。此外,由于激光能量呈高斯分布,熔覆道两侧以及相邻道间搭接区域的能量密度较低,如果送粉量较大而激光能量不足,使粉末不能完全融化,会加剧表面球化现象[15]。故表面球化缺陷常分布在熔覆道两侧或相邻道间的搭接区域,多层FeCr合金球化缺陷实测图,如图4(b)所示。
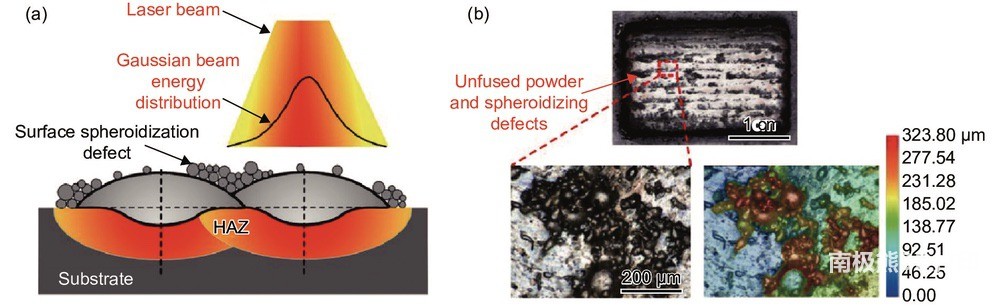
图 4 LAR中球化缺陷 (a)球化缺陷示意图[19];(b)多层FeCr合金球化缺陷实测图[15]
在LAR过程中,采用预热基体和多层成形时进行气氛保护能提升填充材料熔液与凝固层的润湿性[15];适当增加激光能量密度、降低送粉量和延长层间间隔时间(待凝固层稳定后),都有助于改善球化缺陷现象[19]。2.3 气孔
在LAR过程中,以下几种情况都会产生气孔缺陷:一是在高能激光辐照的过程中,熔池温度高,基体材料或者多层多道间搭接处的原有熔覆层发生冶金反应,产生如CO、CO2以及SO2等气体[20-21];二是保护气体或者输送粉末气体(如N2、He以及Ar气等)中混入空气;在快速熔化和凝固过程中,气体如果来不及排出就会在成形件中形成气孔[22-24]。气孔缺陷的形成与气-液-固三相之间的接触角(θ)和熔池凝固时间息息相关[25]。当气体介质与固相界面的接触角小于90°且熔池凝固时间足够长时,气体介质可完全摆脱界面的约束上浮逸出,可避免气孔缺陷的产生,如图5(a)所示;当接触角大于90°且凝固时间较短时,部分残余气体介质仍然附着在固相界面来不及逸出,待熔池凝固后留在成形件中从而形成气孔缺陷,如图5(b)所示。
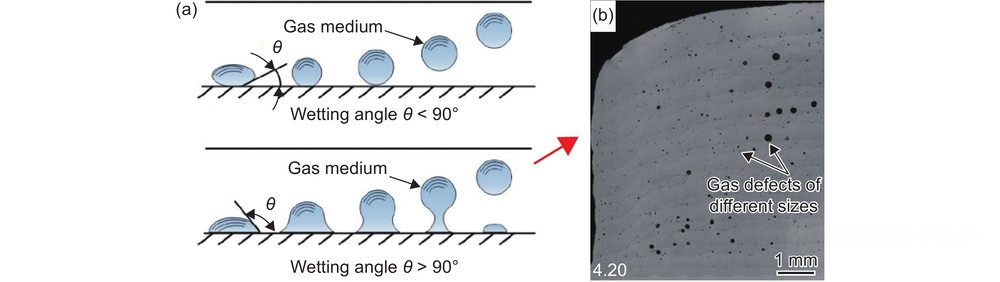
图 5 LAR中气孔缺陷[24-25] (a)气泡上浮过程;(b)成形件中典型气孔缺陷
选取具有良好润湿性的填充材料,成形前充分烘干减少水汽,提高激光输入能量能使熔液液态时间增长以及适当降低扫描速度,使气孔有足够的时间上浮和逸出,都有益于降低材料中的气孔率[20-23]。此外,在LAR过程中对熔池施加超声振动或者磁场等,也能促进气体更好地逸出,降低孔隙率[25]。
2.4 裂纹
应力集中是LAR成形件中产生裂纹的主要原因[23]。LAR过程中产生的应力主要包括热应力、约束应力以及组织应力[26-28],如图6(a)所示。温度梯度的不同会使材料在冷却过程当中基材与修复层或者多修复层内部之间的热膨胀速率不一致,从而产生热应力[28]。熔池中材料受热膨胀,受到周围较冷基体约束而产生的压应力及凝固收缩受到较冷基体的拉应力,称为约束应力。在成形件中,由于金属元素的组织偏聚而引起的应力,称为组织应力。组织不均匀导致该区域应力高于其他位置。在多种应力的共同作用下,应力不会随着冷却而终止,反而会在其内部传播,当应力超过材料极限断裂强度时,萌生出裂纹。随着扫描层数的增加,横向拉应力逐渐积累增大,促使裂纹进一步扩展,从而在成形件中形成跨越多层的长裂纹[27],如图6(b)和(c)所示。
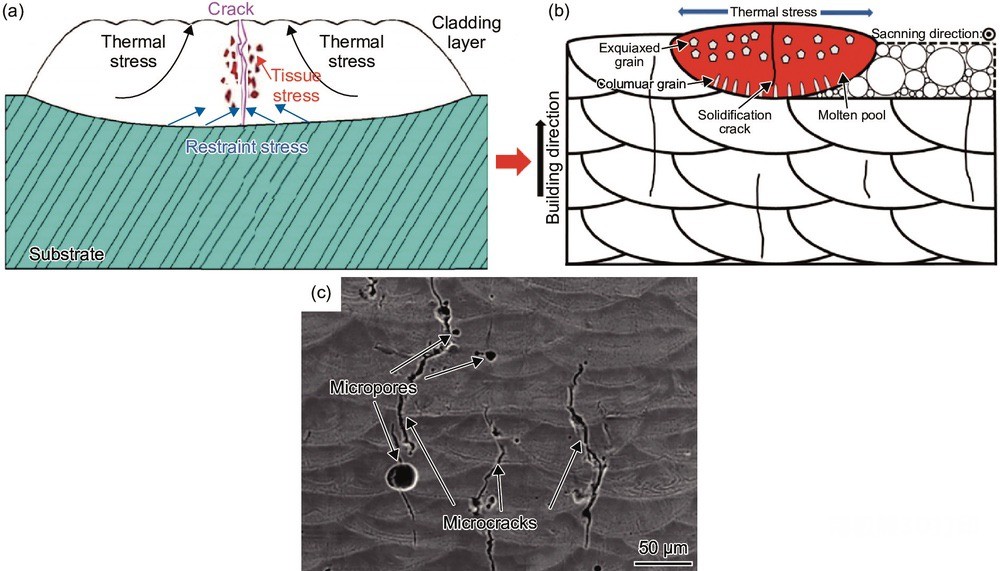
图 6 LAR中裂纹缺陷[27] (a)应力作用示意图;(b)裂纹形成示意图;(c)裂纹形貌
选用与基体材料热膨胀系数接近、材质均匀的填充材料,并在修复前进行预热处理减小温度梯度、适当降低扫描速度减小熔液冷却速率等有助于减小材料内应力作用,降低裂纹率[26-28]。
(责任编辑:admin)
最新内容
热点内容