航天科工3D打印技术助力未来新一代飞行器发展
时间:2021-12-02 08:12 来源:中国日报网 作者:admin 阅读:次
走进7103厂的厂房,和传统制造厂机器轰鸣的生产景象不同,这里噪音很小、地板格外洁净,一台台设备整齐列装,设备内激光飞舞扫描,一层一层铺叠出产品的真容,一件3D打印的宇航级产品随即诞生。目前,在7103厂增材制造创新中心,利用3D打印技术生产一件整流栅,生产流程从原先的19个缩短至3个,生产周期从20天缩短为2天,产品合格率显著提升。
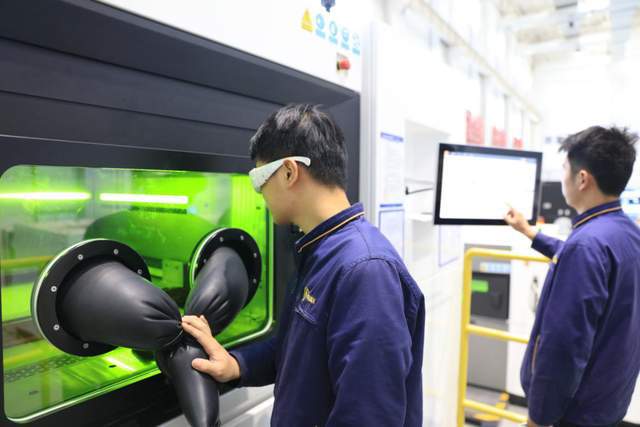
为了满足航天液体动力领域的生产需求,7103厂以3D打印领域发展较为成熟的激光选区熔化成形技术和激光熔覆沉积成形技术为主导,创新优化设计,后处理工艺及质量检测评价展开系统研究,掌握了20余项关键技术,初步构成增材制造应用研究全流程技术体系。
目前,7103厂主要将3D打印技术应用于液体火箭发动机新研型号研制,重点解决“急、难、险、重、新”的零部组件研制问题,同时承担成熟发动机型号复杂异形构件研制及批产。截至目前,3D打印技术已经在40多个型号240余种典型产品中得到使用,产品先后成功参与50余次发射和飞行试验,增材制造创新中心取得了多项技术成果,获得国家科技进步二等奖等8项省部级以上奖励。
“我国开展的新一代航天装备研制难度大、性能要求高、研制周期紧。”杨欢庆认为,随着航天发动机设计性能的提升,宇航产品越发复杂精细,3D打印技术可以从根本层面突破传统制造的技术局限,把图纸设想变为现实。
面向未来发展,7103厂与高校合作,计划培养一批智能制造领域专业人才,增材制造创新中心先后与西北工业大学、华中科技大学组建联合实验室,与西安交通大学成立培养育人基地,形成良好的产学研合作机制。该厂预计在未来2年内建成100台金属增材设备规模的“云端制造”智慧工厂,承担起更重大的研发生产任务。
(责任编辑:admin)
最新内容
热点内容