颜永年:熔覆-挤压工艺在高端装备制造的应用前景
时间:2016-01-09 19:51 来源:未知 作者:中国3D打印网 阅读:次
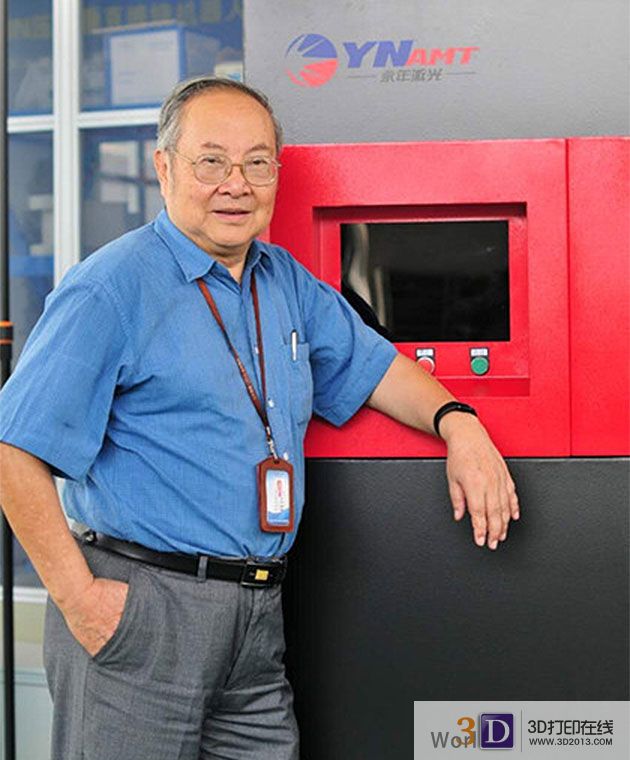
江苏永年激光成型技术有限公司董事长颜永年
当前,国内、外重型装备的重型和大型高端结构件,无一例外地采用重型精炼和重型真空铸锭获得的重型或超重型钢锭,通过“开坯”、“预锻”和“终锻”完成,这就是近两个世纪以来的重型自由锻工艺。而采用与重型自由锻工艺完全不同的成形技术——3D打印金属激光熔覆(LC——Laser Cladding/电子束熔覆(EC——Electron beam Cladding) 技术,完成无偏析的高端优质坯件,再与现代热挤压工艺相结合,通过高温高压闭式挤压,获得高端重型和大型结构件。这种金属激光熔覆制坯-热挤压最终成形的创新工艺称为熔覆-挤压(C-E ——Cladding-Extrusion)工艺。C-E先进成形工艺是用于高端装备制造的工艺,在航空、电力、高铁、海洋、核电和军工领域具有广阔的应用前景。
一、背景简介
进入21世纪,高端装备制造对重型、大型和具有壳台、管台的复杂腔体等核电、海工和军工高端结构件的质量要求越来越高,数量要求越来越多。一般锻件卖不动,高端锻件供不应求,核电锻件尤为严重。现在是“谁有核锻件,谁就有核电站”的年代。传统的重型自由锻设备在我国十分过剩,但又不能很好解决高端锻件的问题。重型自由锻采用重型钢锭为原材料,为提高材料内部质量通过“开坯”来消除偏析,材料和能源浪费很大,锻造精度很差,制造周期很长。在高端、重型成形制造领域,平均1.5~2吨锻件才能加工出1吨零件,而1吨零锻件需要4吨钢锭,故平均6~8吨钢锭才能加工出1吨零件。美国西屋公司AP1000标准的核反应器过渡段,17吨,需钢锭96吨,材料利用率仅17%。核锅炉锻件(508-Ⅲ钢)之钢锭平均利用率仅为20%-25%。钛合金空-空导弹弹头和弹体的材料利用率仅15%。表1和表2说明了核电高端锻件材料利用率是十分低的。重型高端锻件的成形制造周期太长是另一个问题,一根重量8-10吨的核电一回路主管道,需一年的制造周期。AP1000 100万kw,建设时间长达4年,200万kw建设周期需6年。重型高端装备的制造周期长、材料利用率低等因素的综合影响,导致投资巨大AP1000 100万kw 核电站需100~120亿人民币的建设投资。
表1 核电高端锻件材料利用率表
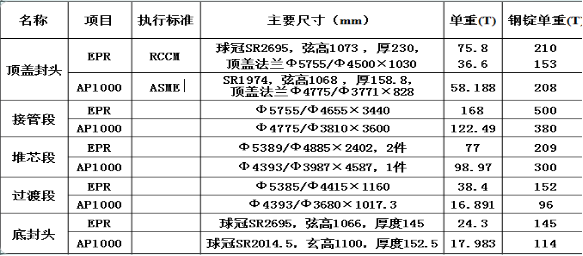
表2 核电高端锻件材料和钢锭利用率表
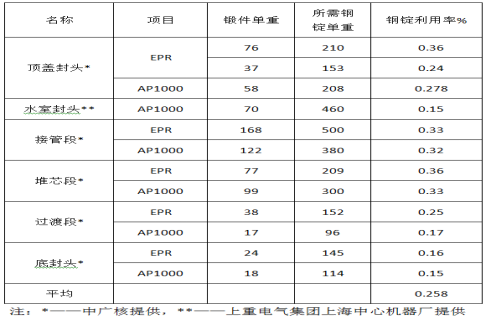
我国的高端重型装备制造的传统技术路线。这是基于重型自由锻技术的《7654》路线,即倾国之力建设具有700吨钢水-600吨铸锭-500吨铸件-400吨锻件能力的技术路线。不可否认,长期以来,《7654》路线为我国的重型装备和国防建设做出了巨大的贡献,大大推动了我国重型装备制造的发展。但进入21世纪以来,其弱点,随着核电、航空、海工向高参数、大容量、高效率、节材、节能、低排放方向发展,逐渐暴露出来,并为工程界所重视。大量的事实证明,《7654》技术路线是高能耗、高材耗、高排放,低效率的技术路线。
《7654》路线流程示意见图1,其核心问题在于钢锭达到600吨重,由于600吨重,才需要700吨钢水和巨大的真空铸锭能力;由于600吨重,导致严重偏析,这才需要1~2万吨自由锻液压机进行开坯。事实上,600吨钢锭一般仅能完成100~200的锻件。钢锭之600吨,并不是零件的需求,而是技术路线和工艺的需求,是该技术路线本身的问题所致:自由锻在开式环境中,需要大体积的塑性变形(大钢锭的高温塑变),才能获的动态再结晶所需要的高强度应力场。上述需求,导致了7654路线的现状。
7654路线的本质是《以大制大》——零件越大,钢锭更大,钢锭重与零件重(如100万kw核电核反应器)之比约在6~8之间。《以大制大》造成巨大体量之液态金属的凝固,引起严重偏析 ;引起巨大钢锭之开坯,需要大功率的设备,造成能源、材料和工时的巨大浪费,见图2。
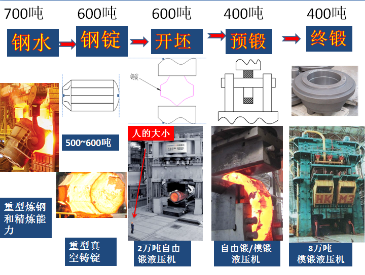
图1 《7654》技术路线示意图
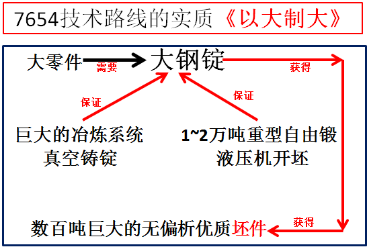
图2 《以大制大》示意图
事实上,传统的重型模锻最适用于航空壁钣和杆件成形;多向模锻最适于小型腔体件,均无法解决上述核电、海工和军工领域中,长期困扰工程界的重型、大型壳体的成形制造问题,这些轴对称和准轴对称、大型、超大型的高端壳体的成形制造任务只能有自由锻来完成了。
3D打印重型熔覆工艺,为解决上述问题开启了一扇大门。本团队在多年金属激光3D打印产业化,特别是重型熔覆工艺的产业化的成果基础上,提出3D打印重型熔覆技术与重型热挤压技术相结合的创新技术路线。这是一种高效、节材、节能、减排的,高端重型金属成形工艺和设备系统,它开辟了一个重型装备制造的新时代。
二、金属激光熔覆工艺
(1)熔覆工艺LCD和EBAM 简介
熔覆(Cladding)是指,在高能量密度的束流(激光束和电子束)作用下,在材料表面产生的冶金过程,其与3D打印的原理相结合,一层又一层地熔覆(增材成形),即形成LCD——Laser Cladding Deposition(激光熔覆沉积)工艺和 EBAM——Electron Beam Additive Manufacturing(电子束增材制造)工艺,分别见图1和图2。在LCD喷头中,激光束经透镜被聚焦到熔覆件的表面,形成微熔池,同时金属粉末也同步送到微熔池中,迅速熔化,并随熔池离去而迅速冷却,完成熔覆,连续进行此过程即LCD过程。EBAM过程与此类似,将激光束流换成电子束流、金属粉换成金属丝即可。
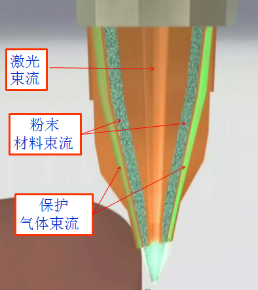
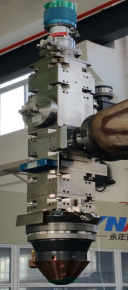
图1 LCD原理图及4000W LCD喷头的外形图
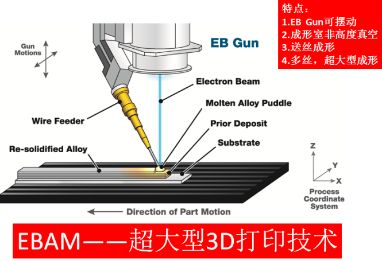
图2 EBAM原理图
采用LCD和EBAM工艺成形金属构件,特别是重型构件,优点明显:熔覆成形过程自动保证了结果的无偏析,熔覆所得坯件结构形状合理,可最好地满足后续热挤压之需,而不是粗造的自由锻件。详细分析如下:
A. 熔覆工艺以小型冶炼系统生产的金属粉末或丝材为原材料,而不是以数十吨或数百吨真空冶炼和真空铸锭系统而得的重型钢锭为原材料,这就节省了巨额投资和建设周期,大大降低成本,
B. 熔覆工艺成形制造的无论是坯件还是最终结构件,其材料利用率可从传统自由锻工艺的20~30%(核电结构件)提高到50~60%,节省大量的宝贵材料,节省材料就是节省能源;
C. 无偏析(Segregation-free),这是以金属粉末和丝材为原材料的3D打印熔覆工艺的共同特点。无数金属粉末在微熔池中迅速熔化并凝固“组装”而成形,就从根本上消除了巨大体量金属熔体,凝固形成之严重偏析,它为获得成分均匀和性能优良的成形件的奠定了基础。既然无偏析,也就无需开坯锻造工艺,节省大量的设备、能源和材料。
D. LCD和EBAM可完复杂的结构的成形,这是增材成形最重要的优点——“柔性”,可成形形状合理,符合挤压工艺需要的坯件,保证挤压工艺的顺利进行。图3为美Sciaky公司采用EBAM工艺完成的6米×1.2米×1.2米大型构件照片,图4为美Lasertec公司采用LCD技术完成整体叶轮。
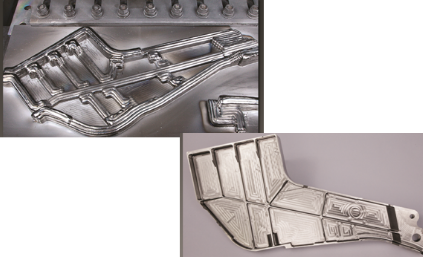
图3 美Sciaky公司完成的6×1.2×1.2米构件,(下图为加工后)
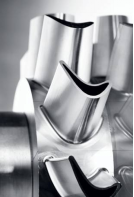
图4 美Lasertec公司采用LCD技术完成整体叶轮-叶片(加工后)
(2)熔覆工艺LCD和EBAM 的“先天不足”
激光熔覆和激光熔化技术完成的成形件,并不能全部达到高端结构件对机械性能严格的要求。熔覆工艺虽然因快速非平衡冷却,较容易成细小、均勻、等轴的晶粒,因而均可保证σb(断裂极限),σs (流动极限)超过各种铸造工艺的强度,接近或达到锻造的强度。然而激光熔覆成形毕竟仍是一种液态凝固的成形过程,这是一种“先天不足”,主要表现在成形件的塑性不够。主要原因在于缺少在热-力耦合作用下,迫使金属产生塑性流动,而发生的动态再结晶过程。只有动态再结晶,才能不但彻底破碎枝晶、非金属氧化物、闭合裂纹和空洞,而且还修复晶界,这就为获得优良的组织及性能奠定了金属学和热力学基础。大量的实验证明:LCD成形工艺而δ(流动极限)ψ(断面收缩率)往往达不到锻件的水平,最终冲击韧性ak必受很大的影响,达不到要求。发明LENS技术的美Sandia国家实验室,将各种材料的激光熔覆成形样品与锻造退火样品比较,就能说明问题。他们公布4组实验结果,就有一组718镍合金的LENS工艺之δ值仅16%,比锻造退火值的20%,差得较多,见表3 。我国华南理工大学杨永强教授对镍铬合金的工艺实验证明,激光熔化样品的延伸率仅为4%,远达不到锻造8%的水平。本团队的高温合金的激光熔化(SLM工艺)实验结果也证明,SLM的延伸率δ和断面收缩率ψ达不到先进热挤压的水平。
表3 美Sandia国家实验室LENS实验结果表
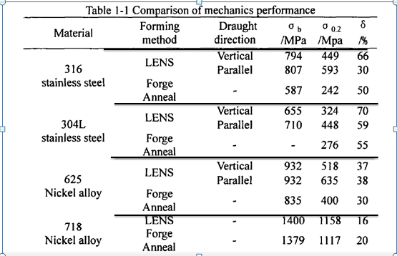
三、熔覆-挤压工艺
上述分析说明,基于自由锻的《7654》技术路线已难以满足21世纪对重型装备制造的要求,而3D打印激光熔覆工艺的成形件之δ和ψ以及冲击韧性ak 均难以稳定地达到重型高端装备制造的要求,但如果将激光熔覆工艺与现代重型热挤压工艺结合起来,以后者来大大提高前者的δ、ψ和ak 则就有另外一番新天地。
事实上,与《7654》技术路线的《以大制大》不同,3D打印增材成形的制造机制是《以小制大》: 采用高能束(激光束或电子束),聚焦于金属表面(含先凝固的质点表面),产生1400度高温,连续熔覆(熔化)并凝固,形成无数微小(数十微米~数毫米)的,无偏析均质的质点,将这些微小的质点实时组装,就形成无偏析、均质的坯件。多个熔覆喷头同时熔覆,即可获的重型坯件,即无需600吨重型钢锭、无需600吨钢锭的开坯、无需预锻,采用微滴凝固-组装,完成优质金属坯件成形制造。
正如前述,工程上的最佳消除铸造缺陷的方法,就是采用动态再结晶,即在应力场下,随着金属的变形进行重新结晶,而完成晶界的修复、晶粒的细化和缺陷的消除。本文建议采用挤压轴,以数千吨~数万吨的挤压力,直接作用在高温熔覆坯件,产生400~600Mpa的球应力,迫使金属产生动态再结晶,大大提高δ、ψ值,最终和获得理想的ak值。本文作者和团队,拥有先进的重型热挤压工艺和设备技术,完成了全国第一套1.5万吨/3.6万吨,垂直钢管制坯/挤压系统,并获得国家科技进步奖。
C-E工艺是崭新的重型金属成形创新工艺,它拥有熔覆和挤压两方面的优点,是先进的重型金属激光3D打印与传统挤压工艺结合的典范,它保证最终制件在强度和塑性两方面,均获的极高的,稳定的机械性能,保证 σb、 σs、 δ、 ψ 、ak 全面达标。图5为C-E工艺技术路线图。
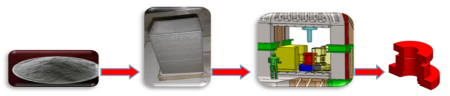
图5为C-E工艺技术路线示意图
C-E技术将3D打印与热挤压进行了巧妙结合:利用熔覆工艺的无偏析(Segregation-free)优点——无需开坯
利用3D打印熔覆工艺的柔性成形的优点 ——无需预锻(预成形)
利用热挤压提高成形件的塑性,保证成形件全面的机械性能 。
麦肯锡全球研究所的一项新研究—— “驱动经济未来的12种技术”强调指出:《在任何一个领域,各家企业都在做同一件事情:将所有这些技术以利润最大化的方式结合起来。技术创新所带来的实际经济收益不会源自那些炫目的想法,至少在近期内如此,而是源自正在趋于成熟的新兴技术与存在了数十年的传统技术的巧妙结合》*。 C-E工艺就是这样一种新兴技术与存在了数十年的传统技术的巧妙结合的典型。
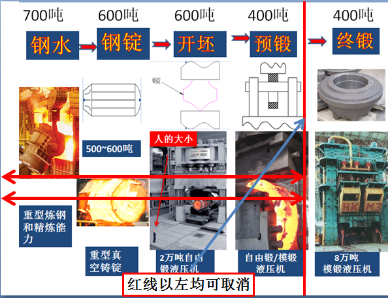
图6 修正的7654技术路线流程示意图
四、核电主管道的熔覆-挤压工艺分析
下面以核电主管道锻件成形制造为例,分析C-E工艺。核电主管道是核电一回路上关键结构件,一个100万kw的反应堆,需8~12根主管道。主管道为AlSI-316L不锈钢,主管道零件重8~10吨,市价1500万/根。一根主管道上有两个非对称的管台,图7为AP1000 主管道锻造毛坯的设计图(主管道零件为弯曲结构,管道弯曲工艺成熟,本项目未加分析)。管台之一体化成形是对重型锻压成形工艺的重大挑战。
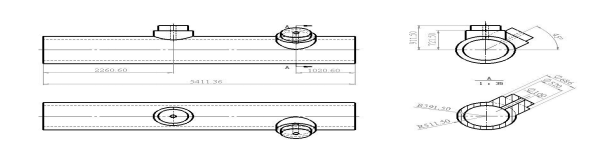
图7 AP1000 主管道锻造毛坯的设计图
为了说明C-E法的特点,以下列出《自由锻法》的成形方法要点,以资比较。
(1)《自由锻法》
目前核电制造业,只能成形实心的(无内孔),直型(不弯曲)之实体结构。
核电主管道的《自由锻法》成形工艺,为目前我国的基本成形制造方法。完成的主管道为盲孔(无内孔的实心柱体),管台成形为方形台体的锻造毛坯,见图8。按单边裕量按80 mm计算,其重量为56吨左右。自由锻工艺的钢锭材料收得率较低,钢锭按锻件重量的2.5倍计算,为56X2.5=140吨*。核电主管道的《自由锻法》采用1.2~1.5万吨自由锻液压机,生产效率很低,仅为12个月/根。显然主管道的《自由锻法》的锻造毛坯粗放,锻件重,锻造工序长,后续加工工时大,材料利用率低。
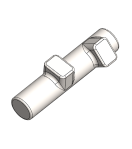
图8《自由锻法》核电主管道锻件图
(2)核电主管道成形制造的C-E工艺
CE工艺是完成核电主管道锻造毛坯的创新工艺。CE法可成形的锻造毛坯,其外径:Ф1023mm、内径:Ф 730mm,管台部分外径:Ф1200mm重量:26.4吨。
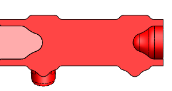
图9 AP1000 主管道C-E法的熔覆坯件图和剖面图
CE法主管道成形制造流程见图10和图11。
首先采用3D打印LCD工艺——激光熔覆工艺,熔覆成一种用于挤压的中间预制坯件。这是一种高质量的用于最终挤压的坯件,完成了预成形的坯件,除无偏析均质的重要优点之外,它还是净成形(Net Shaping)小余量坯件。
其次,对中间预制坯件进行挤压,即可获得主管道的锻造毛坯;
再其次,对主管道的锻造毛坯进行热弯曲并切削加工,即可获的用于电站装配的核电主管道零件。
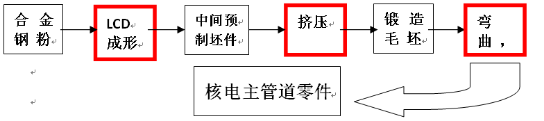
图10 CE法主管道成形制造框图流程
中间预制坯件的设计和成形制造是CE法的重要步骤。要点如下:
① 主管道的两个管台在径向均为非对称结构, 锻造难以成形,但LCD成形则没有困难,CE法采用LCD工艺成形非对称管台,是本工艺的核心步骤之一;
② 中间预制坯件的两端为具有一定深度的盲孔,左盲孔的深度大于右盲孔。盲孔是为后续内孔挤压工序准备的;
③ 中间预制坯件的中段为实心结构,而非空心(图9),其目的在于为后续挤压工序留出所需的变形量(金属流动量)。只有合适的足够的金属流动量,才能防止挤压加热时,的晶粒长大,并保证良好的动态再结晶。
④ LCD中间预制坯件为直管,挤压后也是直管,见图11。完成直管坯件后,再采用重型钢管的弯曲方法进行弯曲,以获得最终的锻造毛坯,见图12。
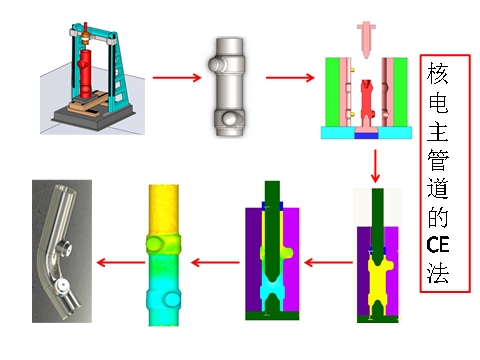
图11 CE法主管道成形制造示意流程
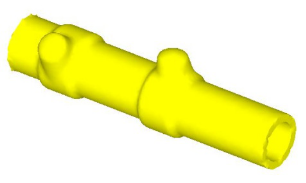
图12 CE法挤压成形件图
五、小结
C-E工艺是先进的3D打印工艺与先进挤压工艺相巧妙结合的典范,对重型高端制造来说,是开创性的。
本项具有四大优点:
(1)本工艺不采用重型钢锭,也就节省了重型冶炼、重型真空铸锭一系列重型设备和工艺过程。本技术路线采用各类金属粉末作为原材料,这一改变导致材料的利用率大大提高,原材料运输、存储的成本大大下降;
(2)本工艺不采用自由锻,而采用小型冶炼-制粉系统制粉,将粉末在微熔池中熔化并迅速凝固组装而成形,完成不存在成分和杂质偏析的,无需开坯强度就可达到要求;无需预锻,形状就可接近最终结构件精化坯件。本工艺节省大量的重型开坯和预锻设备、资金和时间;
(3)本项目采用挤压工艺,在半通用的挤压模中,挤压上述3D打印坯件而最终成形。挤压过程是提高激光熔覆工艺完成的坯件之塑性,从而提高最终结构件的冲击韧性和全面机械性能以及质量稳定性和一致性之核心步骤。
(4)C-E工艺在高端结构件领域,如航空、核电、海工等领域的核心零、部件成形制造方面,具有很强的竞争力,主要表现在节材、节能和节省工时,大大提高生产效率。
作者简介:颜永年,江苏永年激光成形技术有限公司董事长,清华大学教授、博导,从事材料成形研发40多年。第一任清华大学材料成形制造自动化研究所所长,第一任清华大学生物制造研究所所长,江苏省增材制造专委会理事长,中国3D打印技术产业联盟首席顾问,国内较早从事3D打印技术研发的专家之一,曾获国家科技进步奖二等奖两项,三等奖一项,省、部级奖五项和其它各种奖项几十项,承担并完成了多项国家自然科学重点基金、国家863计划及企业的横向合作任务。颜教授带领的研发团队在三维打印技术的工艺、设备、控制等方面取得了丰硕的成果,其中熔融挤压成形工艺的3D打印技术已在北京产业化,面向国际化生产。位于昆山的江苏永年激光成形技术有限公司主营的金属3D打印设备产品与非金属3D打印设备产品相比,其技术难度和应用价值更高,可将金属粉末直接融化、烧结、烧覆,做出技术复杂的金属零件,在模具、航空航天、汽车制造领域应用广泛。
(责任编辑:admin)
最新内容
热点内容