粉末床增材制造的有限元仿真在航空零部件上的应用技术研究
时间:2018-06-15 22:51 来源:南极熊 作者:中国3D打印网 阅读:次
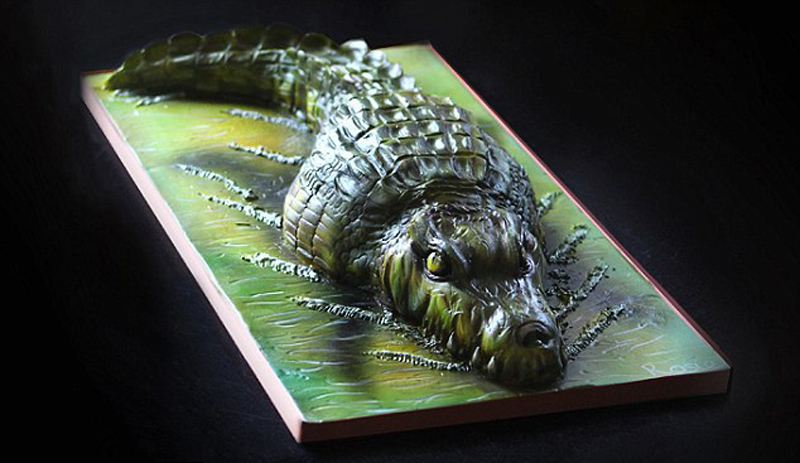
1.有限元法概况
有限元法是一种通过对有限个单元体作分片插值求解力学、物理等问题的数值求解方法。在增材制造科学研究中,有限元法常用于求解在温度场、应力场等多场耦合作用下,零件结构形状几何非线性、材料非线性等问题。
目前粉末床增材制造有限元仿真主要采用Simufact(一种包含AM在内的金属制造过程仿真软件),通过输入材料的本征参数(如化学成分、热力学性能、机械性能、应力-应变曲线等)、支撑方案、激光工艺参数(激光功率、扫描策略、激光光斑、扫描间距等)、热处理工艺、基板切割方向和支撑去除等工艺参数(如图1所示),就能够获得零件在打印、热处理、线切割、支撑去除等多个阶段应力、应变、残余应力的分布情况以及对零件尺寸(变形大小)、机械性能的影响规律,进而确保在启动制造前优化设计方案并最终制造出可被接受的零件。
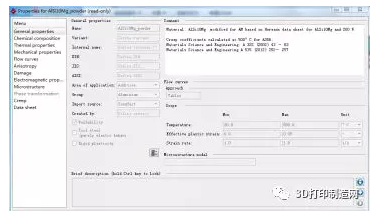
图1 Simufact软件中材料本征参数的输入界面
将有限元仿真技术应用于粉末床增材制造将带来几项变革:在零件制造前可提供精确的零件变形和残余应力结果,降低成形风险,提高“一次打印成功”的成功率;可对构造方向(水平、垂直或者其他方向)进行测试,甄别最优打印方案;对不同的支撑方案进行“无成本”检查,无需“试错”就能验证支撑方案的可行性;此外,还可以进一步处理工艺链的问题,研究构造零件过程中所采取步骤的顺序。综上所述,在粉末床增材制造中有效利用仿真技术,在制造零件前高效探索影响零件的变量,可以极大的缩短研发周期、提高机器/人工利用率、减少材料和能源消耗。由此看来,该项技术在航空零部件的快速制造上更具有推广应用前景。2.航空零部件的有限元模拟研究
2.1模拟验证试验
钛合金材料比强度远高于高强度铝合金、镁合金、高温合金和高强度钢,因此成为航空零部件制造首选的材料之一。钛合金的粉末床增材制造,尤其是零件在基板平面投影的截面积占比较大时,往往在成形过程中产生极大的残余应力,造成钛合金零件的“控形”十分困难。毫不夸张地说,零件在基板平面投影的截面积仅占据基板平面26.79%时,在打印过程中的残余应力释放将厚达25mm的不锈钢基板翘曲了5mm之多。因此,即便是横向打印钛合金的标准力学试验件,如不做后续的去应力退火而直接进行线切割,则所有的横向力学试验件均会发生2mm以上的翘曲变形,如图2所示。
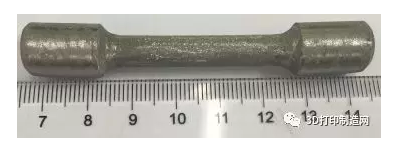
图2 钛合金打印件翘曲示意图
为了验证Simufact软件的可靠性,通过输入TC4钛合金的本征参数(锻件的本征参数),支撑方案、激光工艺参数、线切割方式进行仿真分析,计算出经打印、线切割后零件残余应力的分布情况,并获得零件在各个方向上的变形结果,如图3所示。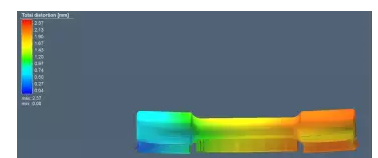
图3 TC4钛合金力学件模拟打印过程中的变形
从图3中可以看出,采用横向摆放方式的TC4钛合金力学性能件,如未经去应力退火直接进行线切割,在打印与线切割过程中产生的残余应力将在零件各个位置进行释放,在端部残余应力达到最大并引起翘曲,翘曲最大变形量达到了2.37mm。仿真结果与实际情况基本吻合,从而验证了Simufact软件的准确性与可靠性。2.2支臂的有限元模拟研究
诸如旧机型战机的支臂等航空零部件,由于国内生产线已经全部停产,但飞机仍需要执行任务,这时采用增材制造技术进行老旧零件的制造具有巨大的优势:无需恢复生产线就能够快速响应航空领域多品种、少批量构件的定制生产,避免了巨额的固定资产投入,适应现代战争“四快”:快速响应、快速制造、快速修复、快速恢复战斗力的新要求。
然而,增材制造技术并不是万能的。航空零部件的材料、形状、结构各异,并不是掌握了该类材料的工艺与支撑方案就通用于其他零部件。实际上,因为工艺的通用性、支撑设计的不合理性,导致零部件打印完后发生开裂,翘曲的现象屡见不鲜。图4即为针对支臂的三维模型,以“经验”进行支撑设计与工艺设定,结果证明采用这种“经验式”的工艺与支撑方案其实并不合理,导致在打印结束后发现支臂其实在打印初期就已经发生翘曲变形,造成大量的材料与时间的浪费。如果有一种有效的模拟方式,在打印启动前就可以评估方案的可行性,则可以避免这种经验式的错误。
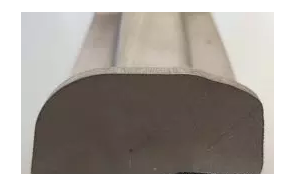
图4 支臂发生的翘曲变形
为了分析造成支臂变形的原因,将铝合金材料(参照铸件标准)的本征参数,支撑方案、激光工艺参数输入Simufact软件中,通过有限元仿真,得到支臂打印过程中的变形情况,如图5所示。从图5可知,采用实际打印工艺与支撑方案,支臂打印过程中发生严重变形的位置为零件前端,最大变形量达到3.03mm。通过模拟分析,准确的预测了实际打印过程中零件将发生变形的位置及变形量。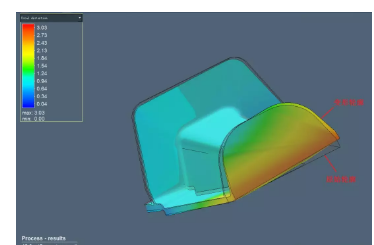
图5 支臂打印过程中的变形分析
2.3导向叶片的有限元模拟研究航空发动机及燃气轮机是工业皇冠上的明珠,其高温高压零件在复杂苛刻条件下工作,使用损伤大,制造难度高,尤其是导向叶片的制造技术仅由欧美少数国家掌握,对外严密封锁。我国虽然突破了部分关键技术并得到应用,但远不能满足新结构、新材料高温高压零件的制造需求。采用基于增材制造的逆向工程技术,能够快速制造高温高压复杂零部件,减少研发费用、缩短研制周期,摆脱受制于人的困境。
通常,用于航空发动机或燃气轮机的高温高压零件形状各异、内部流道复杂,使用的材料又十分昂贵,提高零件的一次打印成功率是降低制造成本的关键因素。如用于燃气轮机的导向叶片就属于该类零件。为了提高导向叶片的一次打印成功率,采用两种不同的摆放方式与支撑方案,通过输入相应高温合金的本征参数(参照铸件标准)、激光工艺参数、去应力退火工艺参数以及线切割方式进行仿真分析,结果如图6所示。
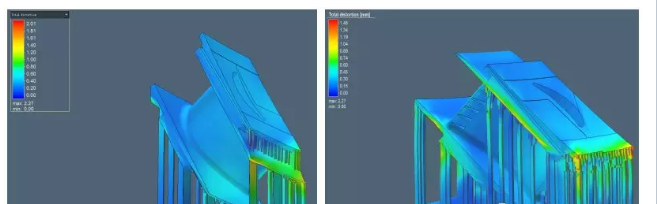
图6 不同摆放形式下导向叶片的模拟分析结果
从图6中可以看出,采用上述两种摆放方式,虽然零件的朝向完全相反(转动180°),但是从仿真结果上看,都是离基板平面的近端处存在较大的变形,最大变形量达到2.27mm。为了验证仿真的准确性,采用两种方案分别试打一件导向叶片,结果如图7所示。从图7中可以看出,实际打印的情况与模拟的结果一致,通过模拟计算获得的变形面与实际打印的变形面完全吻合。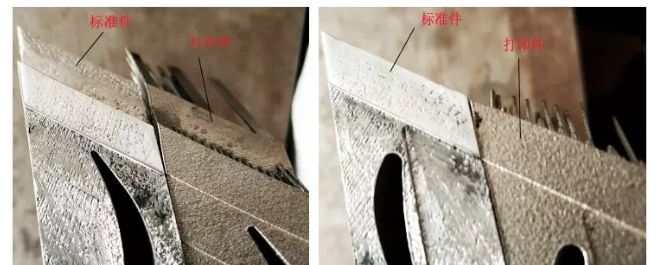
图7 不同摆放形式下导向叶片的实际打印情况
3结束语
随着模拟技术的飞速发展,该技术在增材制造方面凸显出独特的优势,为复杂航空零部件的粉末床增材制造过程中温度场、应力场、变形等提供了精确的参考依据,摆脱了传统工艺优化过程中消耗性的“试错”模式,对增材制造的机理性探索和工艺优化具有重要的指导作用。但是,现阶段的粉末床增材制造仿真技术仍存在其局限性,基于大数据的综合化与大尺寸化成为粉末床增材制造技术未来发展的重点方向。
(1)材料本征参数是关系到仿真结果精确与否的重要参数之一。目前模拟软件输入的材料本征参数绝大部分均沿用同类材料的铸、锻件指标,用于评估、预测3D打印零件特性是不完全、不准确的。因此,建立以3D打印标准试验件为基准的材料本征参数大数据十分必要;
(2)采用模拟技术能够实现增材制造工艺全流程单阶段的温度场、应力场、残余应力的计算,并通过简单叠加预测零件最终的成形效果,其综合耦合能力仍不够强,多阶段多场耦合是未来发展的趋势;
(3)目前,受限于大尺寸零件的边界条件设定、计算时间以及计算精度等问题,模拟技术仅能够对粉末床级别的零件进行精确预测,还无法实现大尺寸构件的模拟。模拟大尺寸化也是未来发展的趋势之一。
(责任编辑:admin)
最新内容
热点内容