关于3D打印和它在汽车制造业中的应用(2)
◆ 原型测试
原型测试即在产品开发阶段,利用3D打印做出原型件,模拟还未量产的实际零部件,并利用它进行测试和改良。目前,许多车企已经在开发阶段使用3D技术进行原型测试了。原型测试本身也分成:概念原型、设计原型、功能原型,三者对设计参数的模拟精度要求依次提高。
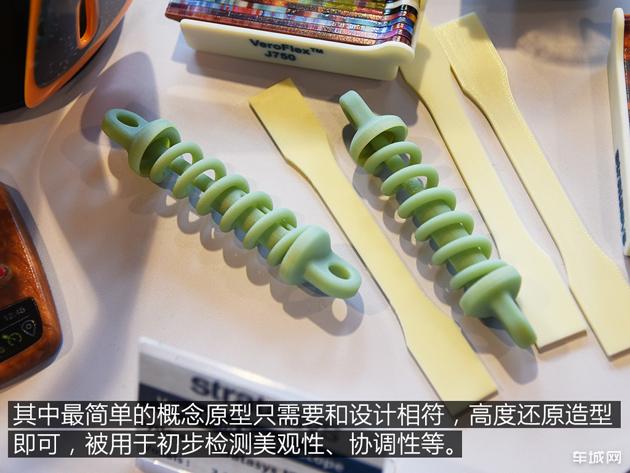
到了零部件的设计原型上,就需要3D打印原型的机械性能也与设计相符,对于材料的使用和工艺的要求大大提高。最后的功能原型与设计原型类似,但因为要放到整车上进行测试,对精度要求更高。
和仿真软件类似,3D打印技术在开发中的应用使得车企和零部件供应商不再需要每修改一版设计,就重新进行一次开模,节省了研发成本。
◆ 生产工具制造
除了用于开发测试之外,由于在少量生产上的优势,3D打印还被用在制造生产工具上,例如贴标机,很多人可能不知道这个东西,这里解释一下:产线工人在装配车牌架的时候并非用手装配,而是需要把车牌架放在如下图所示的贴标机上,然后推着贴标机将车牌架固定到车身上。
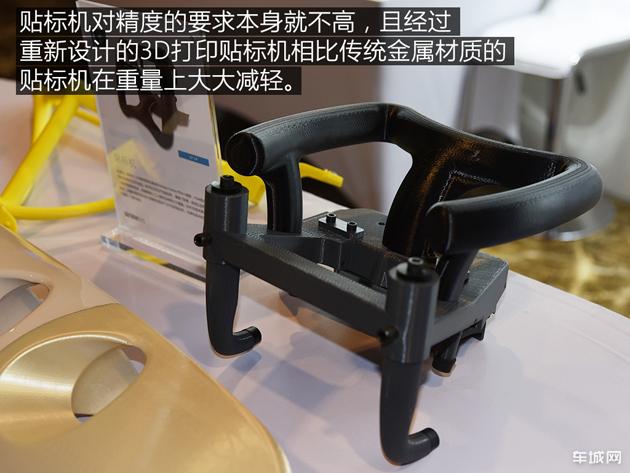
由于每个工厂贴标机只需要十几个,开模制造的均摊成本太高,如果集中制造,还需要库存和物流成本。相比之下,目前很多车企选择在工厂内使用3D打印机,随用随打,免去了开模、库存和物流成本,且一台3D打印机可以制作多种类似贴标机这类的生产工具。此前宝马也利用Stratasys的3D打印机制作了400多个工装夹具,降低了72%的重量以及58%的成本,而这个量级也是最合适使用3D打印技术的,如果再多3D打印就难以胜任了,生产效率和精度都没法和传统制造工艺相比。
◆ 整车和零部件制造
至于零部件,在目前的汽车制造业还极少有量产化的应用。不过,业内“玩家”的新奇尝试可一点不少。
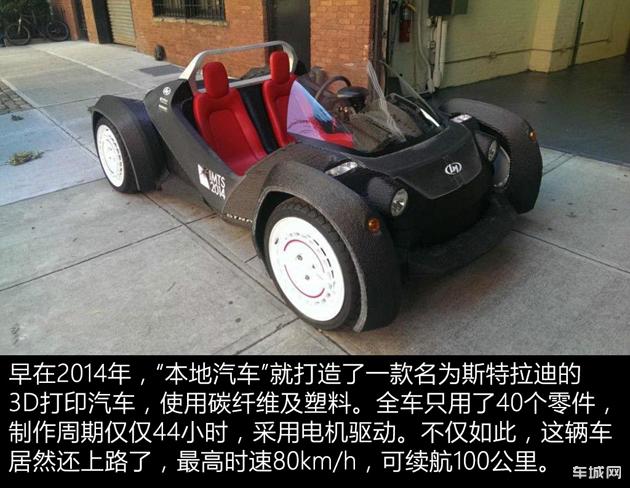
不过,尽管叫做全3D打印汽车(75%使用率),电机、传动机构等核心部件仍然是采购的,这些过于复杂的和对物理性质要求过高的部件,显然3D打印还难以胜任。
当然,除了这些“概念产品”,兰博基尼也曾使用3D打印制造发动机的进气歧管,证明了其应用于核心零部件制造的可行性。实际上,定制化的3D打印件目前就可以达到极高的机械性能,且基于独特的制作形式,我们甚至可以认为利用3D打印制造进气歧管的设计空间还要更高于传统裁切。不过现阶段,这样高度定制化的3D打印产品背后也一定代表着不菲的成本,怕是只能符合兰博基尼这种超跑制造商的定位了。
● 结语
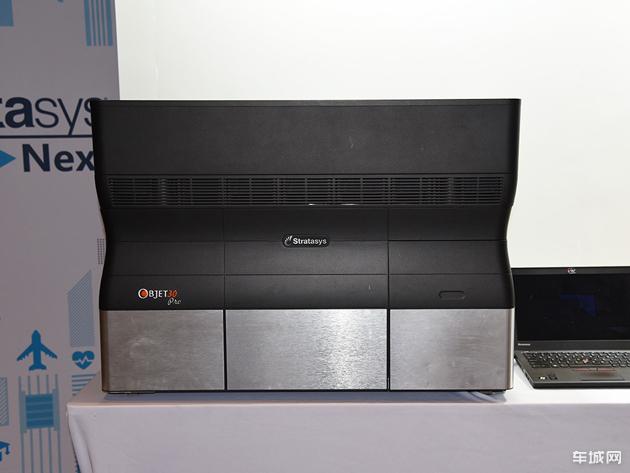
正如上文所说的,3D打印和传统开模制造各自有着明显擅长的地方,3D打印技术适用于分布式生产,在开发阶段和小批量制造上有着得天独厚的优势,但由于其精度等劣势,3D打印技术短时间内还不具备取代流水线生产的能力。然而随着技术的迭代,可以预见的是,未来3D打印一定会越来越多地应用于汽车制造领域,跑马圈地,随着应用的普及以及参与竞争的3D打印技术供应商的增多,其使用成本也会随之下降,形成一个良性循环。未来,在3D打印和传统裁切两种生产模式相互配合之下,进一步缩短开发周期并降低生产成本还是可以期待的。
(责任编辑:admin)