3D打印制品的无损检测现状与展望
时间:2016-07-13 16:05 来源:无损检测NDT 作者:中国3D打印网 阅读:次
3D打印技术的出现被认为是21世纪机械制造工业领域中的一次跨时代的工艺技术革新,给现代社会带来了巨大的冲击和震撼。与传统机械制造技术,即减材制造技术(如切削加工)及等材制造技术(如锻造、铸造、粉末冶金)相比,3D打印技术有许多无法比拟的优势。但是,3D打印制品也会出现很多缺陷,要想在不破坏制品的情况下控制其质量,这个时候就该无损检测大显身手了。
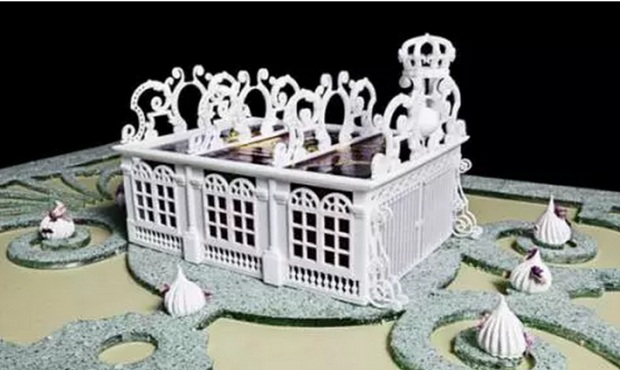
3D打印制品在制备和使用过程中,某些缺陷的产生和扩展是无法避免的。2000年,美国空军研究实验室、英国伯明翰大学以及曼彻斯特大学分别在TC4及316L不锈钢激光快速成形件内部,观察到了气孔及融合不良缺陷。因此,对该技术制造出的零件表面及内部质量检测和验收评定的关键技术的发展的好坏,直接制约了该技术在工程上的应用前景。
目前,国内外的科研人员已对该方面的应用开展了一些的工作,主要集中在研究内部缺陷的特征和形成原因,但是还未能完整地有机形成一个系统,后续还有许多工作需要我们去推进完成。
研究表明,根据3D打印材料中缺陷形成的不同特征,归纳出3D打印中产生缺陷的主要原因有两方面:
① 材料特性导致的缺陷,它由材料特性导致的无法通过优化3D打印特征参数予以解决的缺陷,主要为气孔;
② 特征参量导致的缺陷,即在3D打印中,由于工艺参数或设备等原因导致的缺陷,可以称之为特征参量导致的缺陷,主要有孔洞、翘曲变形、球化、存在未熔颗粒等。
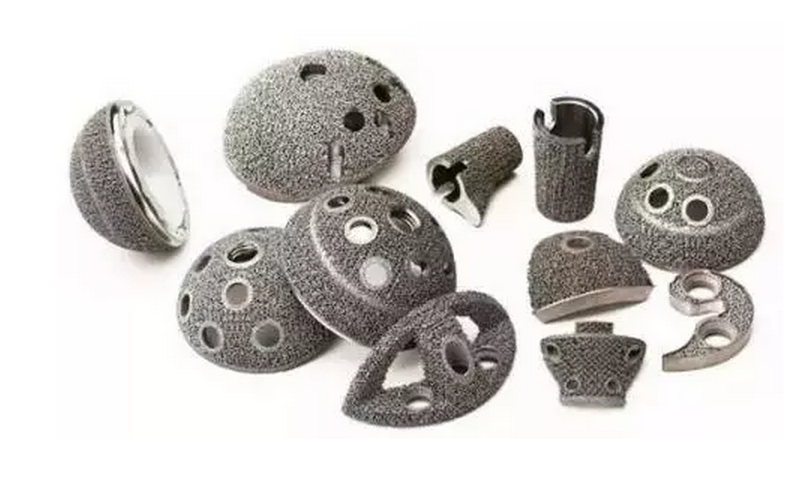
2011年,华中科技大学的研究人员就选择性激光融化成形不锈钢零件性能中粉末特性的影响做了细致研究。发现粉末的粒度、形状及粉末中氧的质量含量对零件成形质量均有较大影响。在一定范围内,粒度越小,成形件致密度越高,但太小的粒度将影响粉末的流动性,反而降低制件成形质量。
2011年,尚晓峰等人通过从工艺参数、设备性能和材料特性等方面来研究制品中形成的缺陷,发现送粉延迟会造成欠堆积或过堆积的形成,直接造成成形尺寸精度下降;比能量是产生粘粉的根本原因,不同比能量会产生不同的冷却速度,比能量越高,冷却速度越快。冷却速度过快,会造成粉末颗粒熔化不充分,未熔化的粉末颗粒粘附在成形件表面或侧壁上,降低了成形件表面质量。
2013年,西班牙加泰罗尼亚理工大学的研究人员采用高频(45MHz)自动水浸超声技术对金属粉末材料的密度、裂纹和未熔合的探测与表征做了研究测试。研究表明超声检测不仅能够用于3D打印制品内部质量检测和在役检测,还可以发展成为一个可靠的质量论证工具;甚至可作为3D打印制造工艺研究的辅助工具,指导其技术升级与创新。
2014年,澳大利亚莫纳什大学的研究人员使用多色X射线技术,对选择性激光熔融的哈斯特洛伊耐蚀镍基合金制品进行了射线检测灵敏度试验研究;研究表明射线检测的分辨率不仅与材料的厚度有关还与缺陷的位置有很大关系;对于2mm厚度的该类制品,射线检测的分辨率为0.2mm,对于10mm的厚度则不到2mm。
(责任编辑:admin)
最新内容
热点内容