收藏备查:增材制造(3D打印)术语表,以后别写错了
时间:2019-05-10 09:28 来源:南极熊 作者:中国3D打印网 阅读:次
增材制造术语
看了本标准,才知道我们很多原来经常用错了3D打印词汇了。
前言
本标准按照GB/T1.1—2009给出的规则起草。
本标准由中国机械工业联合会提出
本标准由全国增材制造标准化技术委员会(SAC/TC562)归口。
本标准起草单位:中机生产力促进中心、上海材料研究所、西安交通大学、青岛理工大学、西北工业大学、清华大学、北京国千智能制造科技硏究院有限公司、西安增材制造国家研究院有限公司、南京师范大学、武汉天昱智能制造有限公司、青岛海尔智能技术研发有限公司、上海航天设备制造总厂、湖南华曙高科技有限责任公司、华中科技大学、中关村创新服务中心、中广核工程有限公司、北京太尔时代科技有限公司。
本标准主要起草人:李海斌、薛莲、金宇飞、张培志、李涤尘、田小永、兰红波、林鑫、林峰、肖承翔、宗贵升、王晶、杨继全、张海鸥、刘永辉、王联凤、许小曙、宋波、田川、张峰、金世振。
范围
本标准规定了增材制造技术所涉及的常用术语和定义。
本标准适用于增材制造领域的研究、试验、检测和生产应用等
2
术语和定义
2.1基本术语
2.1.1
增材制造 additive manufacturing;AM
以三维模型数据为基础,通过材料堆积的方式制造零件或实物的工艺。
注:增材制造、减材制造和等材制造参见附录A。
2.1.2
增材制造系统 additive manufacturing system; additive systen; additive manufacturing equipment
增材制造所用的设备和辅助工具
2.1.3
增材制造设备 additive manufacturing machine; additive manufacturing apparatus
增材制造系统中用以完成零件或实物生产过程中一个成形周期的必要组成部分,包括硬件、设备控制软件和设置软件。
2.1.4
三维打印3D printing
利用打印头、喷嘴或其他打印技术,通过材料堆积的方式来制造零件或实物的工艺。
注:此术语通常作为增材制造的同义词,又称3D打印。
2.1.5
三维打印机3D printer
维打印所用的设备
注:又称3D打印机
2.1.6
增材制造系统用户 additive manufacturing system user
增材制造系统或其外围设备的使用者。
2.1.7
增材制造设备用户 additive manufacturing machine user
增材制造设备的使用者
2.1.8
材料供应商 material supplier
增材制造系统制造零件或实物所需的原材料的提供者
2.1.9
复合增材制造 hybrid additive manufacturing
在增材制造单步工艺过程中,同时或分步结合一种或多种増材制造、等材制造或减材制造技术,完成零件或实物制造的工艺。2.1.10
微纳增材制造 micro-nano additive manufacturing; additive micro/ nano-manufacturing
用于构造微纳尺度结构的增材制造工艺。
2.1.11
单步工艺 single-step process
用单步操作完成零件或实物制造的增材制造工艺,可以同时得到产品预期的基本几何形状和基本
性能。
注1:移除支撑结构和清洁可能是必需的,但不认为是独立的工序步骤。
注2:单步工艺和多步工艺参见附录A。
2.1.12
多步工艺 multi-step process
用两步或两步以上操作完成零件或实物制造的增材制造工艺。通常第一步操作得到零件或实物的
基本几何形状,通过后续操作使其达到预期的基本性能
注1:移除支撑结构和清洁可能是必需的,但不认为是独立的工序步骤。
注2:单步工艺和多步工艺参见附录A。
2.2工艺分类
2.2.1
粘结剂喷射 binder jetting
选择性喷射沉积液态粘结剂粘结粉末材料的增材制造工艺定向能量沉积 directed energy deposition
利用聚焦热能将材料同步熔化沉积的增材制造工艺。
注:聚焦热能是指将能量源(例如:激光、电子束、等离子束或电弧等)聚焦,熔化要沉积的材料
2.2.3
材料挤出 material extrusion
将材料通过喷嘴或孔口挤出的增材制造工艺。
注:典型的材料挤出工艺如熔融沉积成形( Fused Deposition Modeling,FDM)等。
2.2.4
材料喷射 material jetting
将材料以微滴的形式按需喷射沉积的增材制造工艺
注:典型材料包括高分子材料(例如:光敏材料)、生物分子、活性细胞、金属粉末等
2.2.5
粉末床熔融 powder bed fusion
通过热能选择性地熔化/烧结粉末床区域的增材制造工艺。
注:典型的粉末床熔融工艺包括选区激光烧结( selective laser sintering,SIS)、选区激光熔融( selective laser
melting,SLM)以及电子束熔化( electron beam melting,EBM)等
2.2.6
薄材叠层 sheet lamination
将薄层材料逐层粘结以形成实物的增材制造工艺。
2.2.7
立体光固化 vat photopolymerization; stereo lithography;SL 通过光致聚合作用选择性地固化液态光敏聚合物的增材制造工艺。
2.3工艺:基础
2.3.1
成形室 build chamber
增材制造系统中制造零件或实物的空间。
注:某些情况又可称作成形腔。
2.3.2
成形周期 build cvcle
一个或多个零件或实物在增材制造系统成形室中被制造出来的单一工艺过程。
2.3.3
成形范围 build envelope
成形尺寸 build dimension
在成形空间中可制造零件或实物的x、y和x轴方向的最大外部尺寸
注:成形空间的尺寸大于成形范围的尺寸。
2.3.4
成形平台 build platform
成形开始时提供工作面,并在成形过程中起支撑作用的平台。
注:在某些系统中,制造过程中零件或实物直接或通过支撑结构连接到成形平台。在其他一些系统中,如粉末床系统,不是必需的。
2.3.5
成形空间 build space
制造零件或实物的空间,通常在成形室中或在成形平台上
2.3.6
层 laver
材料展平、铺开所形成的薄层
2.3.7
成形面 build surface
叠加材料的平面区域,通常为最新的沉积层,作为下一层成形的基础
注1:对第一层,通常成形面为成形平台
注2:在定向能量沉积工艺中,成形面可以是已有零件或实物,在此基础上进行材料堆积成形。
注3:如果材料沉积或固化方向是变化的(或两者均变化),可以相对于成形面定义
2.3.8
成形空间体积 build volume
设备中可用来制造零件或实物的最大空间。
2.3.9
给料区 feed region
〈粉末床熔融〉设备中储存原材料,并在成形周期中持续提供原材料的区域。
2.3.10
生产序列 production run
在一个成形周期或一系列连续成形周期中,使用相同批次原材料及工艺条件的所有零件或实物的生产过程。
2.3.11
制造批次 manufacturing lot
某一生产订单中,使用相同的原材料、生产序列、增材制造系统以及后处理工艺(如果需要)等生产出来的一批零件或实物。
注:此处,增材制造系统包含一个或多个由设备制造商自行定义的增材制造设备和/或后处理设备
2.3.12
溢料区 overflow region
〈粉末床熔融系统中)在成形周期期间设备内用于收储过量粉末的区域。
注:某些设备的溢料区可以由一个或多个专用室或粉末回收系统组成
2.3.13
零件位置 part location
成形空间中零件或实物的位置。
注:零件位置通常由零件包围盒的几何中心相对于成形空间原点的x、y、z坐标定义。
2.3.14
系统设置 system set-up
增材制造系统的配置参数
2.3.15
工艺参数 process parameter
在单一成形周期内使用的一组操作参数及系统设置
2.3.16
正面 front
设备上操作者正对的操作界面和/或主要观察窗的一侧
注:除设备制造商另有指定外,通常指设备的正面。
2.3.17
原点 origin; zero point
(0,0,0)〈使用x、y、z坐标时)在坐标系中三个主轴交点处指定的通用参考点。
注:坐标系可以是笛卡尔坐标系或由设备制造商自行定义
2.3.18
成形原点 build origin
通常位于成形平台的中心,且固定于成形面上,也可以另行定义
2.3.19
设备原点 machine origin; machine home; machine zero point
由设备制造商定义的原点
2.3.20
x轴x-axis
设备坐标系中与正面平行,并且与y轴和z轴垂直的坐标轴。
注1:除设备制造商另有指定外,通常指设备的x轴。
注2:除设备制造商指定外,x轴正方向为从设备正面看去,面向成形空间原点时从左至右的方向。
注3:通常x轴处于水平位置,且与成形平台的一个边保持平行
2.3.21
轴y-axis
设备坐标系中与z轴和x轴垂直的轴
注1:除设备制造商另有指定外,通常指设备的y轴。
注2:除设备制造商指定外,y轴正方向的定义遵循GB/T19660中的坐标系右手定则。通常当z轴正向向上,此时从设备正面看去,从设备正面到背面的方向是y轴正方向;当z轴正方向朝下时,从设备正面看去,从设备背面到正面的方向是y轴正方向。
注3:通常y轴处于水平位置,并与成形平台的一个边保持平行。
2.3.22
z轴z-axis
设备坐标系中与x轴和y轴(所组成的平面)垂直的轴。
注1:除设备制造商另有指定外,通常指设备的z轴。
注2:除设备制造商指定外,z轴正方向的定义遵循GB/T1960中的坐标系右手定则。对于采用平面、材料逐层叠加的工艺,层的法向是z轴正方向;对于采用平面、材料逐层叠加的工艺,z轴正方向从第一层指向后续层的方向。
注3:材料从不同方向进行叠加时例如在某定向能量沉积系统中],κ轴可根据GB/T19660旋转或滚动确定。
2.3.23
设备坐标系 machine coordinate system
成形平台中根据某一固定点定义的三维坐标系。三个主轴分别标记为x、y、z,旋转轴分别为A、B和C。与x、y、z的角度用右手笛卡尔坐标表示,或者由设备制造商规定
2.4工艺:数据
2.4.1
三维扫描3 D scanning
三维数字化3 d digitizing
通过记录实物表面的x、y、x的坐标值以获取一个实物三维形状和尺寸,并通过软件把各坐标点转化为数字数据的方法
2.4.2
包围盒 bounding box
可以覆盖三维零件或实物表面上点的最小长方体。
注:当制造零件或实物含有附加外部特征(例如标签、标牌或浮雕字母)时,包围盒可根据检测零件或实物的几何形状来确定,检测时不包括附加外部特征。
2.4.3
任意方向包围盒 arbitrarily oriented bounding box
生成方向没有限制的包围盒
2.4.4
设备包围盒 machine bounding box
〈零件的)表面平行于设备坐标系的包围盒
2.4.5
主包围盒 master bounding box
在一次制造过程中可以包围所有零件或实物的包围盒
2.4.6
面片 facet
通常用来表示三维网格表面或模型元素的三角形或四边形等多边形。
注:在AM、AMF和STL中文件格式均使用三角面片,但在AMF文件中允许三角面片为曲面。
2.4.7
几何中心 geometric centre
〈包围盒的〉位于零件的包围盒的算术中心。
注:包围盒的中心可以位于零件或实物外部。2.4.8
初始成形方向 initial building orientation
在成形空间体积中零件或实物的初始放置方向
2.4.9
干涉 nesting
个成形周期中一组零件或实物的包围盒或任意方向包围盒相互重叠的一种状态
2.4.10
零件再定向 part reorientation
将零件或实物的包围盒从零件或实物的初始成形方向围绕几何中心旋转的过程
2.4.11
表面模型 surface model
种使用平面和/或曲面的集合来描述实物的数学或数字表达方法。
注:这种方法可以用来表示一个封闭区域,也可以表示一个非封闭区域。
2.4.12
STL standard triangulation language standard tessellation language
增材制造文件格式的一种,通过将实物表面的几何信息用三角面片的形式表达,并传递给设备,用以制造实体零件或实物
2.4.13
AMF additive manufacturing file format
增材制造数据文件格式的一种,包含三维表面几何描述,支持颜色、材料、网格、纹理、结构和元数据
注:AMF可在一个结构关系中表达一个或多个实物。与STL相似,表面几何信息用三角形网格表示,但在AMF中三角形网格可以弯曲。AMF也可以在网格中指定每个三角形的颜色以及每个体积的材料与颜色。
2.4.14
STEP standard for the exchange of product model data
产品模型数据交换标准
注:参见ISO10303
2.4.15
IGEs initial graphics exchange specification
初始图形交换规范,CAD数据交换格式的一种
注:参见ISO10303。
2.4.16
PDEs product data exchange specification
产品数据交换规范,或使用STEP的产品数据交换。
注:参见ISO10303。
2.4.17
XML extensible markup language
由万维网联盟发布的一种标准语言,用来标记信息内容,采用人机可读的格式。
注:通过使用定制表单和架构,采用统一的表达形式,从而允许内容(数据)和格式(元数据)均可以进行转换
2.5工艺:成形机理及材料
2.5.1
固化 curing
原材料由液态转化为固态的化学变化过程,以形成零件或实物的属性
2.5.2
熔融 fusion
将两单元或多单元材料以熔化的方式结合在一起形成一个单元材料的过程
2.5.3
激光烧结 laser sintering;LS
粉末床熔融工艺中,在成形室内利用一个或多个激光器将粉末材料选择性地熔融/熔化并逐层烧结叠加的过程。
注:大多数激光烧结设备会在加工过程中部分或完全熔化材料。“烧结( sintering)”这个词是过去使用的术语,是误称,因为这种工艺通常要完全或部分熔化,与传统使用浇铸和热(压力)的金属粉末烧结工艺不同
2.5.4
后处理 post treatment
增材制造成形工艺后的处理工艺,为使最终产品达到预期性能。
2.5.5
粉末床 powder bed
增材制造工艺中的成形区域,在该区域中原材料被沉积,通过热源选择性地熔化、烧结或者用粘结剂来制造零件或实物。
2.5.6
原材料 feedstock
增材制造成形过程中使用的材料
注:增材制造工艺通常可以使用多种类型的原材料,例如液体、粉末、悬浮体、丝材和薄片等。
2.5.7
零件黏附粉块 part cake
粉末床熔融工艺中,在成形周期的最后,黏附在成形零件或实物上的多余粉块
2.5.8
粉末批 powder lot
在可追溯的受控条件下生产,来自同一制造工艺周期的大量粉末。
注1:粉料的尺寸由粉末供应商定义。一般粉末供应商将粉末分批供给多个增材制造系统用户
注2:大多数粉末都要求提供可溯源文件(也被称为“合格证”工厂认可证书”或“分析报告”)
2.5.9
粉末合批 powder blend
具有相同成分的多个粉末批的大量混合粉末。
注:如果粉末合批包含原始粉末和使用过的粉末,一般由供应商和用户协商确定。
2.5.10
原始粉末 virgin powder; fresh powder
粉末批中未使用过的粉末。
2.5.11
使用过的粉末 used powder
至少在一次成形周期中被使用过的粉末。
2.5.12
粉末料 powder batch
作为原材料的粉末,可以是使用过的粉末、原始粉末或两者的混合。
注1:使用过的粉末可以是同一成形周期使用过的粉末,也可以是经过不同成形周期使用过的粉末之间的混合
注2:一个粉末料可以用于一个或多个使用不同工艺参数的生产序列。
2.6应用
2.6.1
零件
part
采用增材制造工艺成形的功能件,可以是预期的完整产品或其部件
注:一个零件的功能需求通常由预期用途决定。
2.6.2
原型 prototype
功能不一定完善,但可以用来分析、设计和评估整个产品或其部件的实体模型。
注:用作原型零件的要求仅取决于满足分析和评估的需求,一般由供应商和用户协商确定
2.6.3
原型模具 prototype tooling
可用作为原型使用的铸模、冲模等
注:有时被称为过渡模或软模具。当制造生产用模具时,原型模具有时用于试验模具设计和/或生产终端零件或实物。此时,该模具通常称为过渡模( bridge tooling)。
2.6.4
快速成形 rapid forming
快速原型 rapid prototyping;RP
快速原型制造 rapid prototy ping and manufacturing;RPM
为减少样品生产时间而使用增材制造的技术
注:应用增材制造工艺来生产原型产品从而缩短开发周期的技术。历史上,快速成形(RP)是增材制造技术在商业上的最初应用,因此被视为增材制造技术的通用术语而普遍使用
2.6.5
快速制模 rapid tooling应用增材制造技术来制造模具或模具零部件的工艺,与传统模具制造工艺相比,缩短了模具制造周期。
注1:快速模具可以由增材制造工艺直接制造模具,或者用增材制造工艺间接制造岀模型,然后再利用二次工艺加工出真正模具
注2:除增材制造工艺外,“快速制模”技术也可应用减材制造工艺来制造模具和缩短模具交付周期,如数控铣削加工等。
2.7属性
2.7.1
精度 accuracy
某一结果与可接受参考值或目标值之间的接近程度
2.7.2
成形态 as built
增材制造工艺中,除需要移除成形平台、去除支撑和/或去除原材料外,零部件在成形后和后处理工艺前的一种状态
2.7.3
近净形 near net shape
零件或实物基本不需要后处理即可满足尺寸公差要求的成形状态。
2.7.4
全致密 fully dense
材料的相对密度不小于某一特定值的一种临界状态
注:此特定值可根据需求由用户和制造商协议确定
2.7.5
孔隙率 porosity
表征零件或实物致密程度的指标,为材料中孔隙的体积占总体积的百分比。
2.7.6
重复性 repeatability
在相同环境条件下,使用相同设备对同一特性进行两次或多次测量时的一致性程度。
附录A
(资料性附录)
基本原则
A.1材料叠加成形
实物所具有的功能由其几何形状和材料特性共同决定。为此,为得到实物的预期几何形状(材料可以实现)和特性,通常将制造工艺分解为一系列操作和子工艺。
通过生产工艺改变材料形状的过程,可通过以下三种基本方法中的某一种或多种的组合实现
等材制造:所需的形状通过对原材料施加压力得到,例如:锻造、弯曲、铸造、注塑、粉末冶金或陶瓷加工中的坯体压缩等;
减材制造:所需的形状通过选择性去除材料得到,例如:铣削、车削、钻削,电火花加工等;
增材制造:所需的形状通过材料堆积得到。
除以上方法外,带有特定形状的零件或实物还可以通过物理、化学方法,将其连接形成更加复杂形状的实物,例如焊接、粘结、紧固件连接等增材制造技术利用材料叠加成形方法,通过逐层叠加材料以制造三维实体几何形状材料叠加”是指将原材料叠加并连接(例如熔融或粘结),最常见的方法是通过逐层叠加的方法制造零件或实物。工艺的决定性因素是用于叠加材料的技术。例如,由于不同材料的熔融和粘结原理不同,决定了不同种材料适用不同的工艺。总的来讲,利用增材制造工艺加工形成的产品的基本属性由以下因素决定
a)材料的种类(聚合物、金属、陶瓷或复合材料等);
b)熔融或粘结方法(熔化、固化、烧结等);
c)用作增材制造的原材料形态(液态、粉末、悬浮体、丝材、薄片等);
d)供料方式(送粉、铺粉等)
这种通过连续叠加材料以制造零件或实物的工艺,使得零件或实物材料的特性髙度依赖于增材制造操作过程中的设备类型和工艺参数。因此,如果不与特定设备和工艺参数关联起来,很难准确预测这些材料的特性。
逐层叠加以制造零件或实物的方法也会引起在零件或实物中材料特性的定向依赖性。因此,某增材制造零件或实物的材料特性还取决于加工过程中该零件或实物在成形空间里的方向和位置
A.2单步和多步增材制造工艺
增材制造工艺的基本方法是通过材料逐层叠加形成三维实物,根据不同的工艺,实物可以通过单工艺步骤即获得预期的基本几何形状和特性,即单步工艺;或者通过主要工艺步骤获得几何尺寸,再通过二级工艺步骤获得预期材料特性,即多步工艺,参见图A.1。例如,在主要工艺中,通过粘结剂将材料
连接以得到基本的几何形状,然后通过后续工艺进一步强化材料。根据零件或实物最终用途,所有的工艺都可能需要一种或多种附加的后处理操作(例如后固化、热处理、精加工等,更多内容参见ISO17296
2)以获得最终产品的所有预期特性。增材制造技术可以用作生产模具及铸模,再利用模具或铸模生产相关产品。此时,增材制造只作为制作模具的手段,而不是生产最终的产品。因此,这种情况应视为增材制造技术的间接应用。
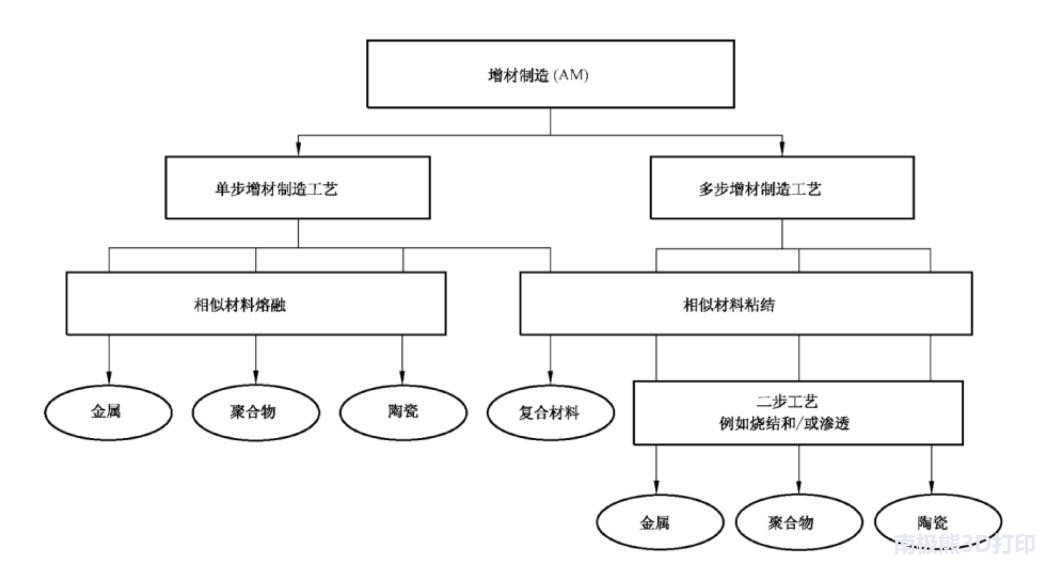
△单步和多步增材制造工艺
A.3增材制造工艺
A.3.1概述
连接材料以形成实物的方法有很多,不同类型的材料通过不同方式连接在一起:金属材料通常通过金属键连接,聚合物分子通常通过共价键连接,陶瓷材料通常通过离子和/或共价键连接,复合材料可以通过上述任一方式连接。不同种材料决定了不同的增材制造工艺,另外连接操作还受材料送入系统时的形态以及送料方法影响。对于増材制造工艺来讲,其使用的原材料通常为粉末(干燥、糊状或膏体)、丝材、片材、熔融以及未凝固的液态聚合物。根据原材料的不同形态,原材料被逐层分布到粉末床中、通过喷嘴/打印头沉积、在实物中逐层叠加,或用光加工液体、糊状或膏体。由于材料的种类众多,不同类型的原材料及送料方式,使得形成了多种可以用作增材制造的工艺原理。虽然在世界范围内已经开展了大量研究和开发工作,但是大部分工艺还没有实现,仅很少一部分已经实现商用。
A.3.2增材制造单步工艺
零件或实物在单一操作中制造,可以同时获得预期产品的基本几何形状和基本材料特性。去除支撑结构并进行清洗是必要的。图A.2~图A.4给出了金属材料、聚合物材料和陶瓷材料的增材制造单步工艺的。
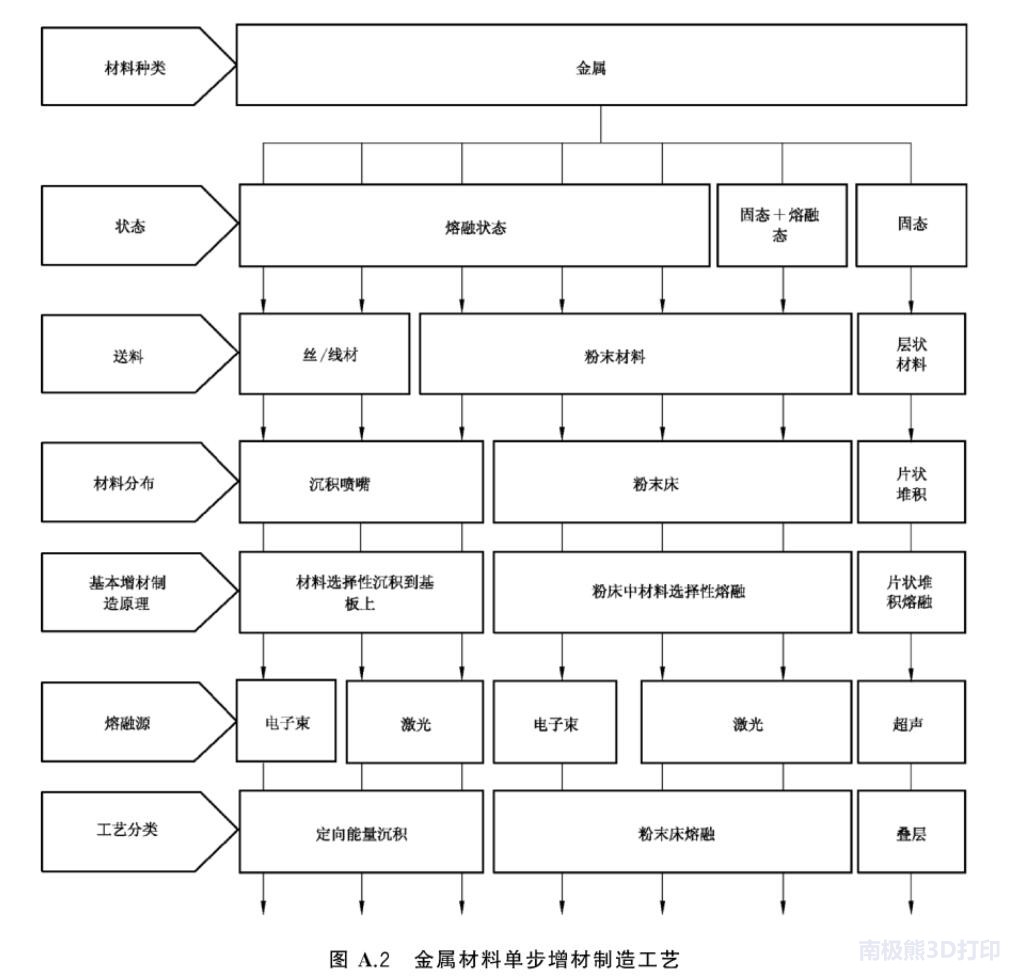
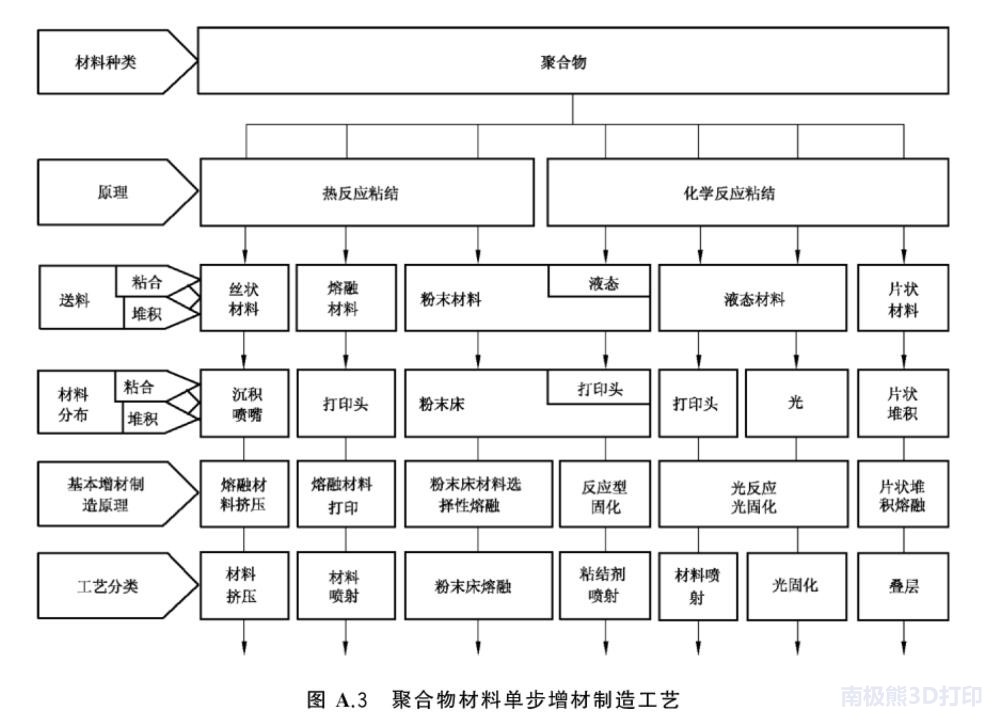
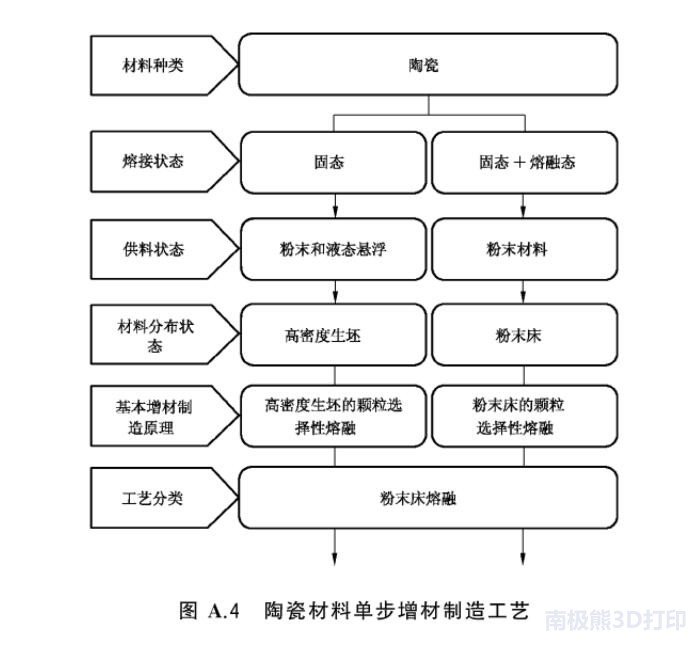
A.3.3增材制造多步工艺
零件或实物通过两步或多步操作制造,可以首先获得其基本几何形状,然后固化零件或实物以获得预期基本材料特性。理想情况下,首次操作后可以将材料粘结以形成由复合材料组成的零件或实物。
图A.5给岀了金属材料、聚合物材料和陶瓷材料的多步增材制造工艺
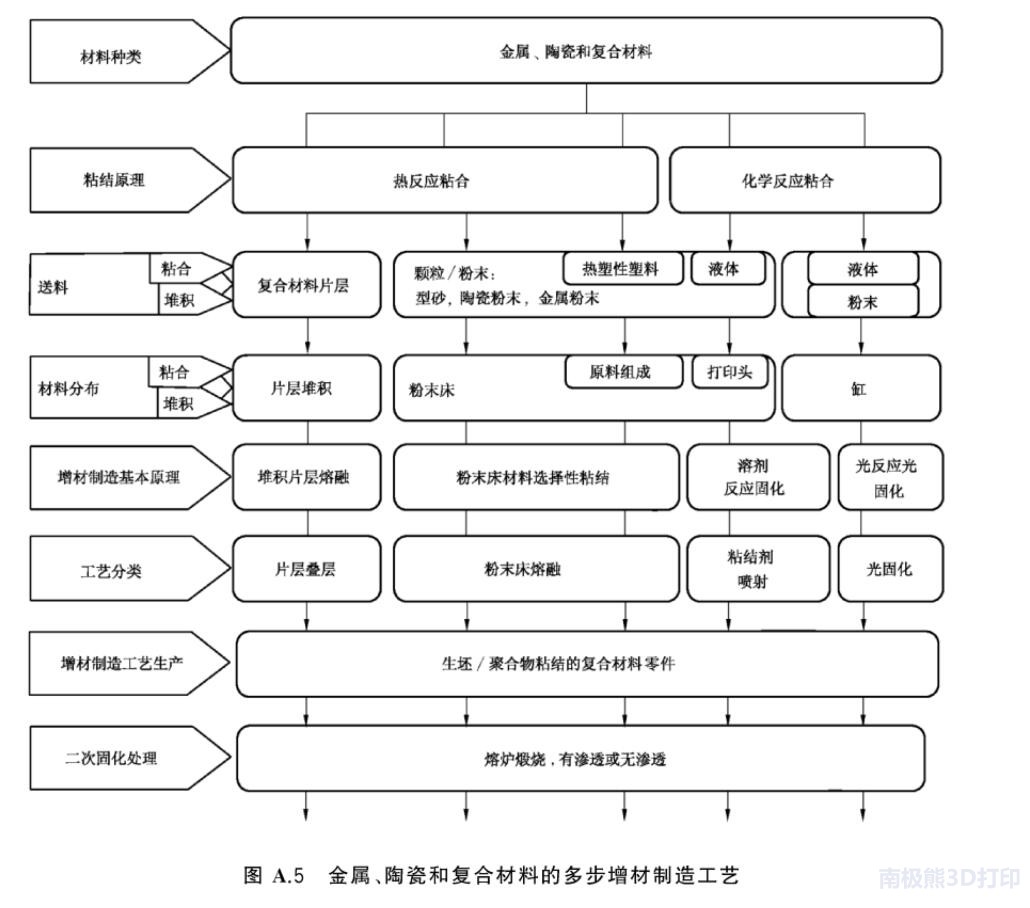
[1 ISO/ ASTM 52900 Additive manufacturing--General principles- Terminology
[2 ISO 10303 Industrial automation systems and integration-Product data representation and exchange
[3 ISO 17296-2. Additive manufacturing General principles Part 2: Overview of prrocess categories and feedstock
(责任编辑:admin)
最新内容
热点内容